A decoiler with straightener is an essential piece of equipment in metalworking industries, crafted to optimize material handling and ensure precision in sheet metal processes. This advanced machinery serves a dual function—uncoiling metal coils and preparing sheets for further processing by flattening any inherent curves or warps. Through firsthand experiences in managing sheet metal operations, a deep understanding of the machine's significance is vital.
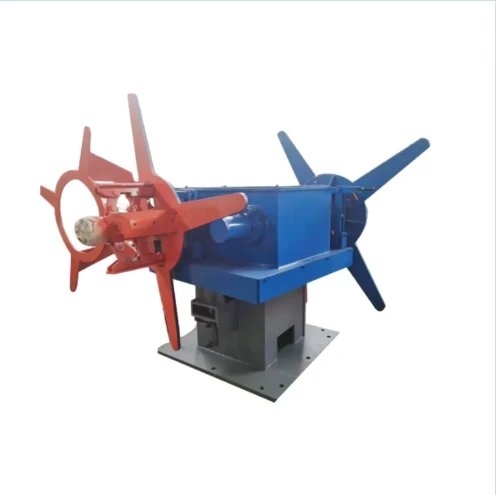
In industries ranging from automotive manufacturing to construction, the need for flat, precisely aligned metal sheets cannot be understated. An expert working with these machines will emphasize that the initial quality of the uncoiled sheet significantly impacts the final product's integrity. A decoiler with straightener ensures that coils are unwound uniformly and are flattened seamlessly, making subsequent manufacturing steps more efficient. This dual-function device saves significant time and labor costs, which is crucial in maintaining a competitive edge.
Technical knowledge of how decoilers with straighteners operate can demystify their importance. The decoiler includes a spindle that holds the metal coil in place, allowing it to unwind under controlled tension. This tension is critical because it can affect not just the speed but also the quality of the unwinding process. When considering a decoiler for a facility, assess whether the tension control mechanism accommodates different materials and thicknesses—a feature often highlighted by authoritative industry leaders.

In conjunction, the straightener usually features a series of rollers that incrementally flatten the metal sheet as it is processed. These rollers are calibrated to address the metal's memory effect, a tendency of metal to return to its coiled state. Experts advise regular maintenance checks on these rollers to avoid misalignment, which could compromise flatness. In workshops where precision is a daily demand, especially aerospace and electronics, trusting your equipment to deliver consistency can boost operational credibility.
The importance of understanding the specific requirements of your production line cannot be minimized. Industry thought leaders often share insights into customizing decoiler and straightener settings, tailored to unique materials used, be it stainless steel, aluminum, or copper. Adjusting parameters within operational guidelines can minimize metal fatigue, reduce material waste, and assure longer equipment lifespan—factors contributing to a reliable workflow and enhanced trust in product quality.
decoiler with straightener
Moreover, the integration of advanced technologies in decoilers with straighteners, such as automatic threading systems and digital interface controls, demonstrates an industry shift towards smarter, more intuitive machines. Savvy operators, through experience, recognize the advantage of these features not only in streamlining operations but also in fostering a safer working environment by reducing manual handling and associated risks.
Considerations for purchasing such a machine must also include energy efficiency and ease of integration with existing systems. Publications by experienced operators and engineers often highlight potential pitfalls if energy consumption is not gauged correctly, affecting both operational costs and environmental footprint. Trustworthy manufacturers will provide specifications and support to ensure seamless integration and adherence to sustainability standards.
In gaining authority in this domain, contributing knowledge through case studies and performance evaluations enriches the shared understanding of decoilers with straighteners. Detailed reports on return on investment (ROI) and efficiency gains post-implementation serve as endorsements of the machine's value. These analyses often form the bedrock of purchasing decisions and strategic planning, underlining the importance of data-backed insights.
In conclusion, a decoiler with straightener is more than an auxiliary tool in metal processing; it is a cornerstone that underpins the operational efficiency and quality assurance of the production line. Mastery in using this equipment, supported by professional experience, technical expertise, authoritative industry knowledge, and an unwavering commitment to credibility, ensures that businesses remain competitive and resilient in a dynamic marketplace. And as technology continues to evolve, staying abreast of advancements in these machines will further cement their roles as indispensable assets in the pursuit of manufacturing excellence.