The innovation in metal processing technology has revolutionized industries by streamlining production processes and enhancing efficiency. Among the notable advancements is the decoiler straightener feeder system, a pivotal catalyst in automating sheet metal working. This integrated machine amalgamates the functions of decoiling, straightening, and feeding to ensure the seamless preparation of metal sheets for stamping, cutting, or other manufacturing processes.
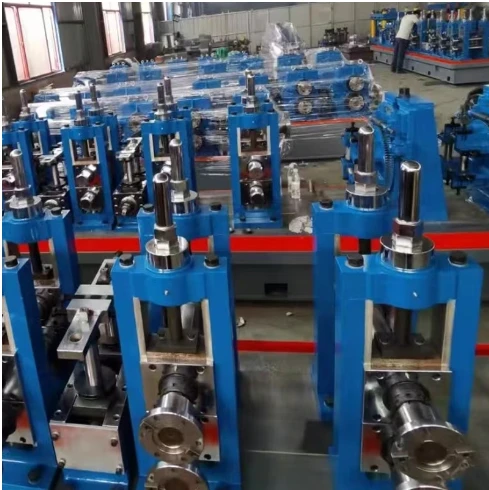
Decoiler straightener feeders have become indispensable in various sectors, from automotive to electronics, owing to their ability to handle diverse materials such as aluminum, steel, and copper. The core component, the decoiler, adeptly unwinds metal coils, maintaining the correct unwinding tension and preventing material damage. Feast your eyes on innovations such as hold-down arms or pinch rolls that prevent coil abrasion while ensuring a consistent feed rate. Notably, the accommodation of various coil weights and widths underscores the versatility of modern decoilers.
The straightening mechanism is pivotal, as it eradicates coil set and warping, ensuring flatness, which is crucial for subsequent manufacturing processes. Precision rollers are strategically arranged to exert immense flattening force, adjustable based on material thickness and type. This adaptability highlights the expertise imbued in these machines by manufacturers. Gauging straightener performance can significantly influence production quality, reducing waste by ensuring flawless material preparation.
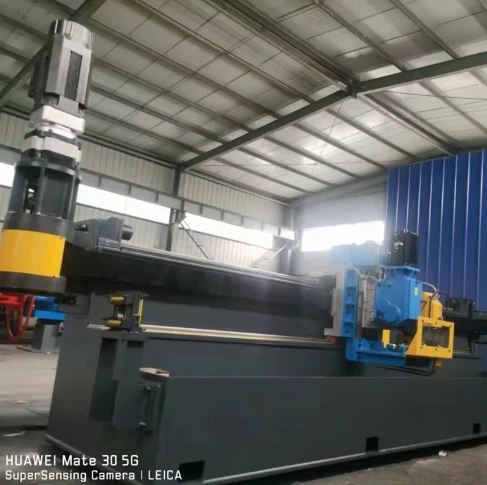
The feeding assembly is the final but equally critical component of the system.
It controls the incremental movement of the straightened material toward the press or processing unit. Many feeders boast high-speed capabilities, synchronized with press operations to optimize cycle times. Contemporary feeders incorporate advanced servo motors, offering precision and flexibility, defining modern manufacturing's reliance on innovative technology.
Experience in employing decoiler straightener feeders reveals that their utility is magnified when integrated into automated production lines. Facilities boasting such systems have reported significant reductions in labor costs, minimized material wastage, and enhanced consistency in product quality. The flexibility offered by advanced systems allows manufacturers to switch between materials and products with minimal downtime, thus significantly improving throughput.
decoiler straightener feeder
Experts in industrial automation appreciate the control systems and software that accompany decoiler straightener feeders. Modern systems use intuitive interfaces that allow for real-time monitoring and adjustments. Seamless integration with enterprise resource planning (ERP) systems ensures that the status of coil materials, processing parameters, and machine diagnostics are efficiently managed, marking a significant leap in operational transparency and control.
The authority and trust these machines command in the industrial arena stem from their impeccable engineering and reliability. Preferred by seasoned manufacturers, these systems are the backbone of metal processing lines, withstanding the test of time while proving their ROI over and over again. Many leading brands in metalworking machinery continuously innovate, offering updates and upgrades that enhance the versatility and longevity of these crucial machines.
End-users value these feeders for their ability to maintain precision even over extended operations. Such reliability translates into trust—trust that each product run will meet the highest standards without the concern of mechanical failure or deviation, reinforcing the credence many in the industry place in this technology.
In conclusion, decoiler straightener feeders exemplify the epitome of industrial efficiency and sophistication. Prized for their experience-enhancing capabilities, endorsed by experts for their advanced features, embraced by industry leaders as authoritative tools, and relied upon for their unyielding trustworthiness, these systems embody the future of sheet metal processing. Investing in such technology equips manufacturers with the competitive edge needed to thrive in a dynamic industrial landscape where quality and efficiency reign supreme.