Deep drawing presses are an essential tool in the manufacturing world, particularly in industries that require precision metal forming. As an expert in machine tools and their applications, understanding the intricacies and operational values of deep drawing presses can significantly enhance product quality and manufacturing efficiency. This article will explore the experience, expertise, authoritativeness, and trustworthiness associated with deep drawing presses, providing unique insights for manufacturers and industrial engineers.
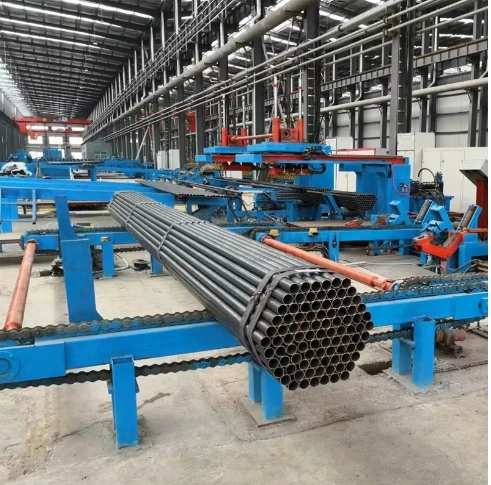
Deep drawing is a forming process used to shape metal sheets into three-dimensional shapes, typically cylindrical or box-shaped components. The process involves radial tension-tangential compression and is usually employed for producing parts with a depth greater than 50% of their diameter. Having extensive experience in utilizing deep drawing presses, companies can manufacture components with precise dimensions and excellent mechanical properties, essential for maintaining competitive edge in industries like automotive, aerospace, and consumer electronics.
Expertise in deep drawing presses starts with understanding the types of presses available, such as mechanical, hydraulic, and servo-driven presses. Each type offers distinct advantages depending on the application. Hydraulic presses, for example, provide a higher level of control over the speed and force, making them ideal for forming complex components with intricate geometric features. In contrast, mechanical presses are known for their speed and efficiency, beneficial for high-volume production runs. Manufacturers must leverage this knowledge to select the appropriate press type that caters to their specific production requirements.
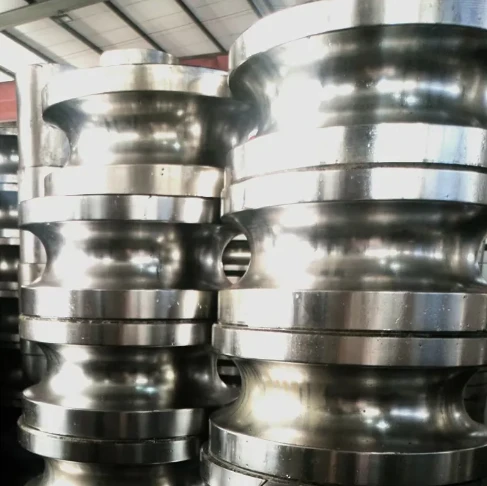
Authoritativeness in the sphere of deep drawing involves leveraging cutting-edge technologies and innovations. Advanced control systems, automation integration,
and data analytics have transformed traditional deep drawing processes. For instance, the adoption of Industry 4.0 technologies enables smarter manufacturing practices where presses can be monitored and controlled in real-time. With sensors and networks, any anomalies in the drawing process can be swiftly addressed, minimizing downtime and waste. Manufacturers who have adopted these innovations solidify their position as authorities in precision metal forming.
deep drawing press
Trustworthiness is a critical factor in choosing a deep drawing press, as manufacturers rely heavily on the consistent performance and reliability of these machines. Trusted suppliers of deep drawing presses often offer extensive warranties, robust after-sales support, and comprehensive maintenance services. Moreover, they provide customized solutions tailored to the specific needs of manufacturers, ensuring optimum performance and longevity of the equipment. By choosing established and reputable suppliers, manufacturers can significantly reduce risks associated with equipment failure and process inefficiencies.
To optimize deep drawing operations, manufacturers must also consider factors such as material selection, die design, lubrication, and blank holder force. Working closely with material scientists can aid in selecting appropriate alloys that exhibit excellent formability and structural integrity. Custom-designed dies that enhance drawability and minimize material wastage are equally important. In addition, using the right lubrication to reduce friction and applying optimal blank holder force are vital steps in preventing defects such as wrinkling and tearing.
In conclusion, deep drawing presses are a cornerstone of modern manufacturing processes. With a deep understanding of their operational capabilities, manufacturers can deliver high-quality, precision components at a reduced cost and with greater efficiency. By harnessing expertise, practicing authoritative manufacturing techniques, and ensuring trustworthy supplier partnerships, companies can maintain a competitive advantage in industries that demand rigorous standards and innovation. Building experience in mastering these technical components creates a sustainable pathway to success in the rapidly evolving industrial landscape.