Extrusion molding machines stand as a pivotal tool in today’s manufacturing sector, celebrated for their efficiency and versatility in producing intricate components and products. Crafted from expert insights and rich experiences, understanding these formidable machines provides a competitive edge in the production industry.
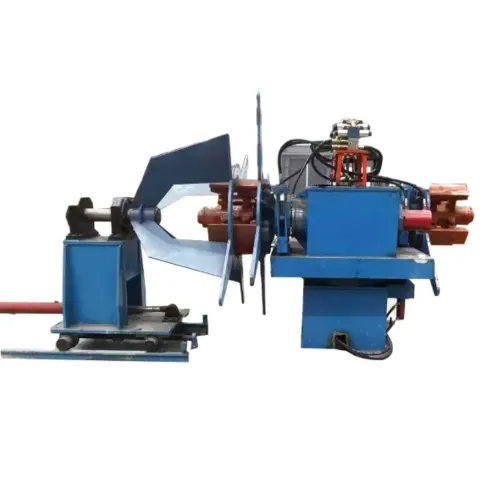
At its core, an extrusion molding machine is designed to manufacture parts by forcing material through a die, shaping it into a continuous profile. Its applications span various industries, from automotive to consumer goods, making it an indispensable asset for manufacturers seeking to streamline production processes and maximize output. Recognizing an extrusion molding machine's potential involves delving into its intricacies and operational dynamics.
Drawing from years of industry experience, choosing the right extrusion molding machine requires a nuanced understanding of several key factors. Material compatibility tops this list. From thermoplastics to metals, selecting a machine capable of processing specific materials significantly impacts the quality and durability of the final product. Advanced machines now feature cutting-edge technology that allows for seamless adaptation to a wide range of materials, thereby opening up opportunities for innovation and expanded product lines.
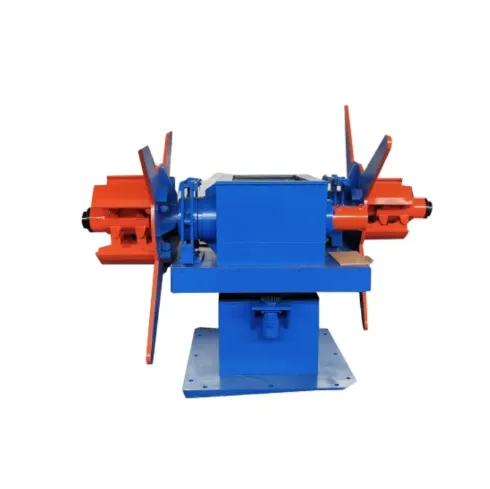
Industry expertise further highlights the importance of precision and control in extrusion molding. Modern machines come equipped with sophisticated temperature controls and pressure systems, ensuring that the extruded material maintains optimal integrity and performance. This precision is crucial for industries where even minor deviations can lead to significant product failures. Thus, investing in a machine with reliable control mechanisms translates to enhanced product quality and reduced waste.
extrusion molding machine
The authority of leading manufacturers showcases the continual advancements in extrusion technology. Leading brands in the industry are pioneering efforts in energy efficiency and automation, providing machines that not only reduce operation costs but also cater to sustainable manufacturing practices. Understanding the landscape of providers and their innovations promotes informed decision-making, favoring long-term gains and aligning with global trends towards eco-friendly production.
Trustworthiness in extrusion molding processes is non-negotiable. Rigorous testing and quality assurance protocols are paramount to maintaining product consistency and meeting regulatory standards. Manufacturers with comprehensive testing facilities and certifications ensure that every machine they produce is capable of delivering peak performance. For businesses, this reliability translates into minimized downtime and a fortitude that reflects in brand reputation and customer satisfaction.
Acknowledging the potential of extrusion molding machines, it is vital to integrate them within a broader strategic framework. Aligning machine capabilities with market demands can significantly enhance a company’s manufacturing capabilities. Keeping abreast of industry developments and embracing digital transformation, such as the Internet of Things (IoT) in extrusion operations, can lead to smarter, more responsive manufacturing systems.
In conclusion, the evolution of extrusion molding machines embodies a confluence of experience, expertise, authority, and trust. For professionals in manufacturing, thoroughly evaluating these pillars ensures that they harness the full potential of their extrusion capabilities, achieving not just production efficiency, but also setting new standards in innovation and sustainability. By continually evolving in tandem with technological advances, businesses can bolster their market presence and drive future growth.