Unlocking the Potential of Hydraulic Press Shear A Comprehensive Insight
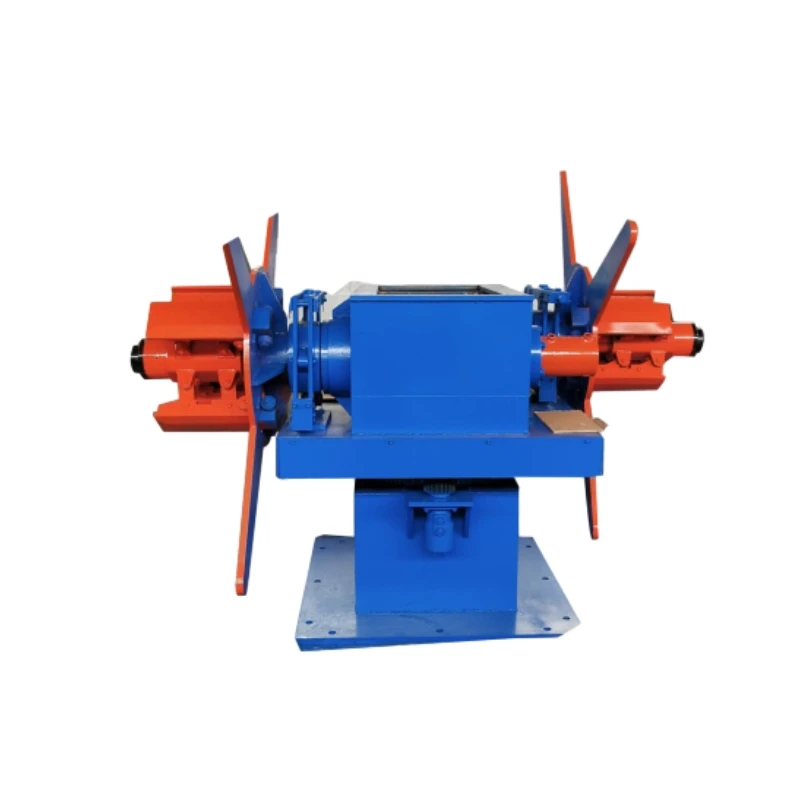
The hydraulic press shear stands as a cornerstone in the realm of industrial machinery, offering versatility and efficiency in metal fabrication processes. With its ability to cut through various materials with precision, the hydraulic press shear has revolutionized sectors ranging from automotive manufacturing to aerospace engineering. This article will delve into the intricate details of hydraulic press shears, focusing on their operation, advantages, and real-world applications, all while aligning with the E-A-T principles.
Hydraulic press shears operate on a simple yet powerful principle the conversion of hydraulic energy into mechanical force. This energy transformation is facilitated by hydraulic cylinders that exert immense pressure, enabling the cutting blades to move with precision. Due to this robust mechanism, hydraulic press shears can cut through significant thicknesses of metal, which makes them an invaluable asset for heavy-duty applications.
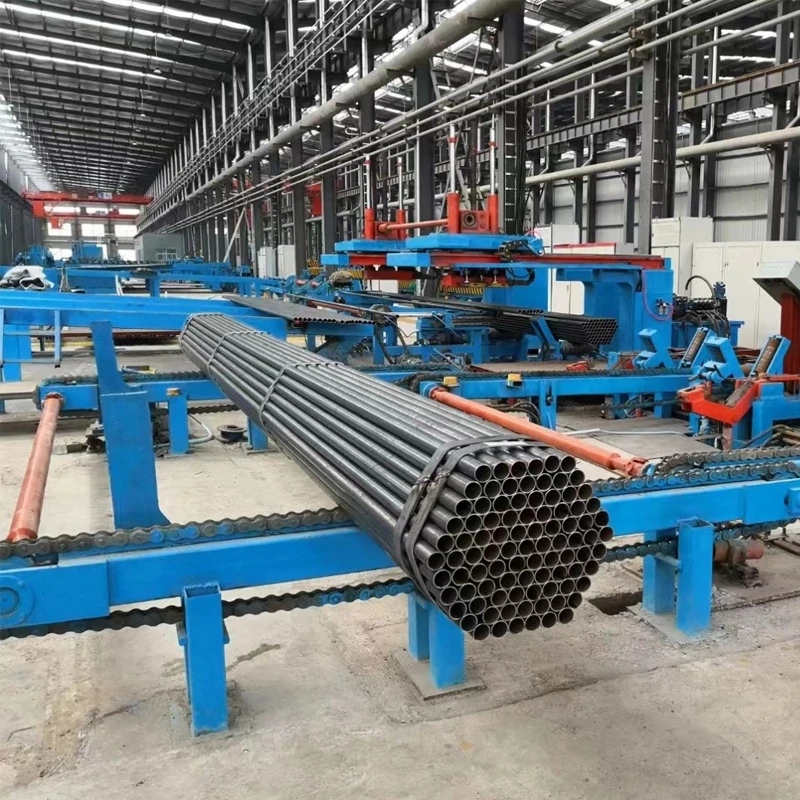
One of the standout features of hydraulic press shears is their precision and control. Unlike mechanical alternatives, hydraulic shears offer adjustable speed and force, providing operators with unparalleled control over the cutting process. This adaptability ensures minimal material waste and high-quality finishes, aligning with modern manufacturing standards that demand excellence and efficiency.
Industries leverage hydraulic press shears not only for their precision but also for their safety features. Gone are the days when operating a shear meant exposing workers to high-risk environments. Today’s hydraulic shears come equipped with advanced safety mechanisms, such as emergency stop buttons, light curtains, and pressure sensors, all designed to ensure operator safety while maintaining operational efficiency.
hydraulic press shear
Moreover, the versatility of hydraulic press shears extends beyond simple metal cutting. They are capable of executing complex processes, such as blanking, piercing, and notching, with remarkable ease. This versatility reduces the need for multiple machines, offering a cost-effective solution for businesses looking to optimize their production lines.
Real-world applications of hydraulic press shears span multiple industries. In automotive manufacturing, these shears facilitate the production of intricate car parts, ensuring that each component meets stringent specifications. The aerospace sector benefits from the precision cutting capabilities of hydraulic shears, producing components that contribute to the safety and performance of aircraft. Additionally, in the construction industry, hydraulic press shears play a pivotal role in shaping and resizing materials for large-scale projects.
While the benefits of hydraulic press shears are evident, selecting the right model for specific applications requires expertise. Factors such as material type, thickness, and desired cutting speed must be considered to ensure optimal performance. Consulting with industry professionals or manufacturers can provide valuable insights and recommendations tailored to unique operational needs.
Trustworthiness in hydraulic press shear operations is further enhanced by regular maintenance and adherence to manufacturer guidelines. Ensuring that the machinery is frequently inspected and serviced can prevent unexpected downtimes and extend its operational lifespan. Partnering with manufacturers for regular check-ups can bolster both efficiency and trust in the machinery’s capabilities.
In conclusion, the hydraulic press shear is an epitome of efficiency and precision in metal fabrication. Its ability to deliver clean cuts, coupled with its advanced safety features and versatile applications, makes it a valuable asset across various industries. By understanding the operational intricacies and maintenance requirements, businesses can fully harness the potential of hydraulic press shears, ensuring excellence in their fabrication processes. When chosen and managed correctly, these powerful machines not only elevate production quality but also reinforce a company’s commitment to safety and innovation in modern manufacturing.