Industrial cold cut saws, integral to precision manufacturing, have evolved immensely, enhancing efficiency and reliability across various industries. As an essential instrument for cutting metal and other materials, these saws offer unparalleled accuracy, minimal waste, and highly efficient operations—key factors elevating industries from automotive to construction.
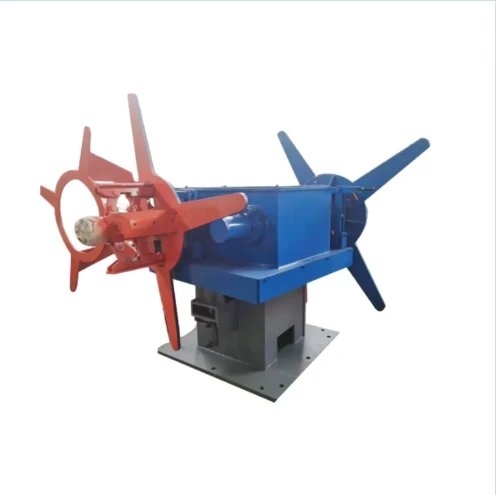
Understanding the mechanics behind industrial cold cut saws is critical. Unlike conventional saws, cold cut saws operate without generating heat, thanks to their specialized teeth configuration and cutting speed. This attribute prevents material warping and compromises to structural integrity during cutting, making them indispensable for tasks requiring pristine finish and tight tolerances. Industries utilizing these saws benefit from reduced thermal deformation, ensuring components fit accurately in assembly processes.
The versatility of industrial cold cut saws is unmatched. They can tackle a range of materials beyond metals, including plastics and composites, without altering physical properties. This adaptability grants manufacturers the flexibility to process various materials using a single machine, thus streamlining production lines and reducing equipment costs.
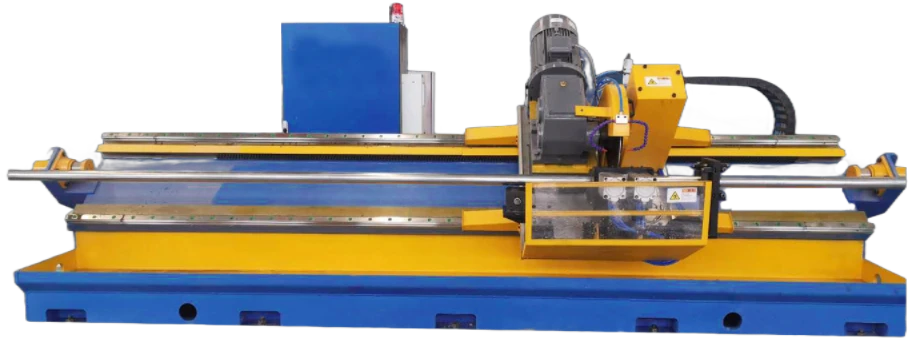
Expertise in selecting the right industrial cold cut saw is paramount for businesses aiming to optimize their manufacturing processes. When choosing a saw, factors such as blade type, motor power, and cutting capacity must align with production needs. For high-volume operations, investing in an automatic cold cut saw with advanced feed mechanisms and programmable controls can drastically enhance throughput and product consistency. Additionally, diamond-tipped blades offer superior durability, lowering operational costs through reduced blade wear and maintenance needs.
industrial cold cut saw
Renowned manufacturers continuously innovate to meet industry demands, introducing features such as noise reduction, enhanced safety mechanisms, and automated lubrication systems. These advancements not only improve worker safety and comfort but also enhance the lifespan and reliability of the saws. Companies looking for sustainable solutions will appreciate models designed to conserve energy and minimize environmental impact through efficient cutting technology.
Trustworthiness of a supplier should also play a vital role in the procurement process. Established brands provide comprehensive customer support and warranty services, ensuring that equipment downtimes are minimized. Moreover, collaborating with suppliers offering training sessions can empower operational teams, maximizing the saws' potential and ensuring their correct usage and maintenance.
In-depth real-world experience with industrial cold cut saws affirms their pivotal role in manufacturing. Testimonials from industry leaders reveal how integrating cold cut saws has paved the way for innovation, enabling the production of complex components with ease. By eliminating heat-induced stress, these saws preserve the quality of high-performance metals crucial for aerospace and automotive sectors, fostering advancements in these fields.
In conclusion, the investment in industrial cold cut saws is not merely a purchase of equipment, but a strategic enhancement of production capability and quality assurance. The expertise in harnessing their full potential lies in understanding specific operational needs and aligning them with the right technological features. As industries progress, the role of industrial cold cut saws becomes increasingly vital, proving their indispensability in achieving precise, efficient, and sustainable manufacturing solutions.