Creating a highly efficient hydraulic pipe bending machine combines ingenuity with expert engineering. Unlike traditional pipe bending machines, a hydraulic version leverages fluid mechanics to achieve precision and flexibility, crucial for industries where accuracy is paramount.
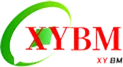
The core principle of a hydraulic pipe bending machine is simple yet potent using hydraulic pressure to stretch and bend metallic pipes into specified angles and shapes without compromising their structural integrity. This method surpasses the manual and mechanical techniques, offering a seamless and smooth bend every time.
One of the key reasons to opt for a hydraulic system is its superior control and consistency. The hydraulic power enables the machine to exert continuous pressure, which is crucial when working with sturdy metals like steel and stainless steel. The uniform pressure reduces the risk of deformities, providing exact results that meet strict engineering tolerances.
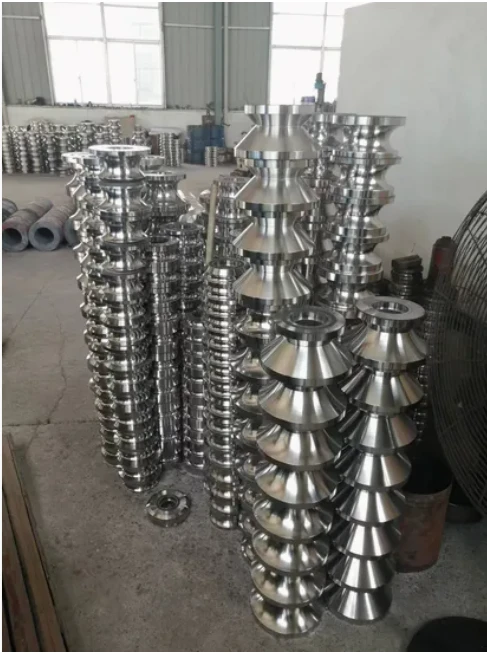
Manufacturing a hydraulic pipe bending machine begins with selecting the right components. High-quality hydraulic cylinders are crucial, as they provide the force needed to bend the pipes. The cylinder’s capacity should correspond with the size and thickness of the pipes it intends to bend. Expertly designed frames made from durable materials ensure the machine withstands the stress of continuous operations.
Equally important is the hydraulic pump system, the heart of the machine. Selecting an appropriate hydraulic pump requires understanding the required flow rate and pressure levels. Efficient pumps minimize energy consumption while maximizing output, leading to cost-effective operations. A comprehensive hydraulic system includes not only the cylinders and pump but also valves, hoses, and a reservoir designed to handle high-pressure fluids safely.
Automating these machines with programmable logic controllers (PLCs) enhances their capability, offering precision and repeatability. With a PLC, operators can set specific parameters, ensuring each bend is exact and consistent, which is vital for assembly line production settings.
making hydraulic pipe bending machine
Safety components are indispensable in a hydraulic pipe bending machine. High-pressure operations necessitate robust safety measures to prevent accidents. High-quality hydraulic seals, pressure relief valves, and emergency stops are mandatory to protect operators and maintain regulatory conformity.
In terms of maintenance, hydraulic systems require regular inspections to ensure longevity. Checking for hydraulic fluid levels, seal integrity, and pump efficiency is essential. A routine maintenance schedule prevents unexpected downtimes and extends the machine's operational life.
Trustworthiness in manufacturing hydraulic machines comes from sourcing components from reputable manufacturers who comply with industry standards. These components undergo rigorous testing to ensure they withstand operational stresses and environmental conditions.
Innovations in hydraulic technology continue to evolve, offering more adaptive machines with greater energy efficiency and reduced environmental impact. Adopting these advancements ensures that hydraulic pipe bending machines remain at the forefront of industrial applications, offering users unmatched reliability and precision.
The versatility of hydraulic pipe bending machines makes them a sought-after asset in numerous sectors, including automotive, construction, and plumbing. Organizations seeking to invest in such technology should look for manufacturers with a track record of expertise and reliability, offering machines that are not only advanced but also user-friendly and easily maintainable.
In conclusion, crafting a hydraulic pipe bending machine demands a nuanced understanding of hydraulics and machine design, where accuracy, expertise, and focus on safety converge. By leveraging these elements, businesses can significantly enhance their production capabilities, ensuring precise outcomes and operational efficiency in various high-demand engineering environments.