For those who work in industries involving wire processing, a manual wire straightener stands as an indispensable tool for achieving precise results. This article explores the essential aspects of manual wire straighteners, detailing their utility, functionality, and the expertise required to utilize them effectively. A thorough understanding of manual wire straighteners can contribute significantly to enhanced productivity and quality in wire handling tasks.
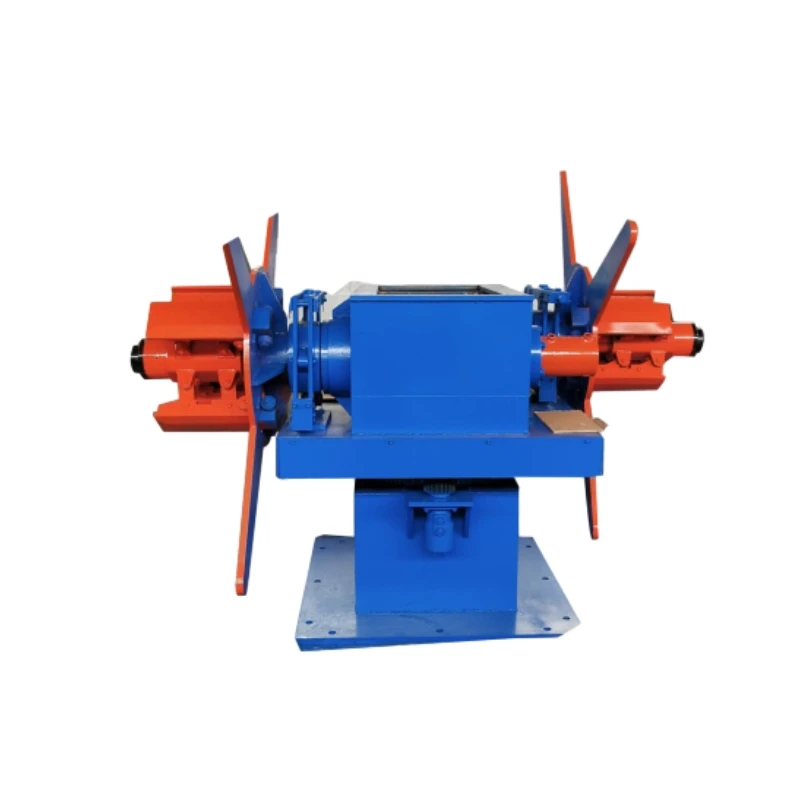
Manual wire straighteners serve a vital role in situations where wires need to be shaped precisely without causing damage or deformation. These devices are engineered to correct the inherent curvature of wires that occur during manufacturing or through shipping and handling processes. Particularly in sectors like manufacturing, aerospace, automotive, and construction, where precision is paramount, the ability to straighten wires manually provides operators with a high level of control over the final product.
One of the defining features of manual wire straighteners is their simplicity combined with effectiveness. Unlike automated systems, manual straighteners allow for careful observation and adjustment, which are crucial in handling different wire diameters and materials. Experienced operators appreciate the tactile feedback these devices provide, which plays a critical role in determining the right pressure and alignment needed to achieve desired results.
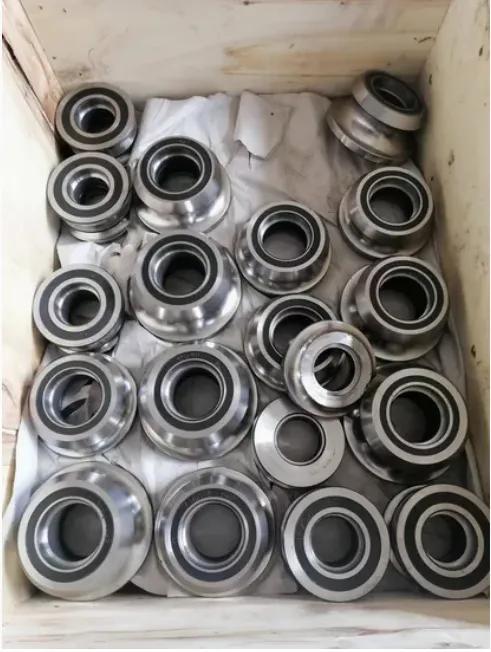
Mastering the use of a manual wire straightener requires understanding three major factors wire material, wire diameter, and the intended application.
Different materials respond variably to the straightening process. For example, softer materials like copper may require a gentler approach than harder materials like steel, which can withstand more pressure. The wire diameter also significantly influences the adjustment settings of the straightener. Technicians need to calibrate the tension and roll pressure meticulously to match the specific wire being straightened.
Furthermore, using a manual wire straightener effectively involves expertise in recognizing wire imperfections. Skilled professionals can identify and correct subtle bends and kinks that might seem negligible but can cause problems in sensitive applications. The ability to detect these issues visually and tactically ensures that the wire meets stringent quality standards, reducing the risk of defects in final products.
manual wire straightener
The industry's reliance on manual wire straighteners can be seen in the vast array of models available, each designed to cater to specific tasks and wire types. Some are designed for heavier gauges, possessing robust frames and larger rollers, while others are suited for finer, more delicate wires, featuring precise adjustments and smaller components. Selecting the appropriate model involves assessing the wire characteristics and the particular requirements of the application.
Moreover, maintenance of manual wire straighteners is crucial for their longevity and performance. Regular inspection and cleaning of the tool can prevent wear and ensure smooth operation. Users need to be adept at identifying signs of wear such as roller misalignment or uneven tension distribution which can compromise straightening quality.
Professionals in wire processing often rely on the guidance of industry experts when choosing and operating manual wire straighteners. Expertise shared through professional associations, technical workshops, and real-world experience underscores the authoritative knowledge needed to make informed decisions about equipment selection and operation. Such insights contribute to better upfront investments in tools and reduce operational costs by minimizing errors and enhancing the efficiency of manual operations.
In conclusion, the manual wire straightener is a pivotal tool in precision wire processing, demanding a blend of practical experience, meticulous attention to detail, and a profound understanding of wire properties. Mastery of this tool signifies authoritative expertise in the field, allowing for the dependable production of high-quality wire components. Skilled use of manual wire straighteners not only leads to improved outcomes but also reinforces trust in the capabilities and commitments of wire handling professionals dedicated to quality and excellence.