The orbital pipe welding machine, a marvel in modern manufacturing, revolutionizes the way industries approach welding tasks. Designed for precision and efficiency, these machines have become indispensable in sectors where high-quality, consistent welds are paramount. Delving deep into the nuances of orbital welding can reveal its unmatched benefits and wide-ranging applications, making it an essential tool in today's industrial landscape.
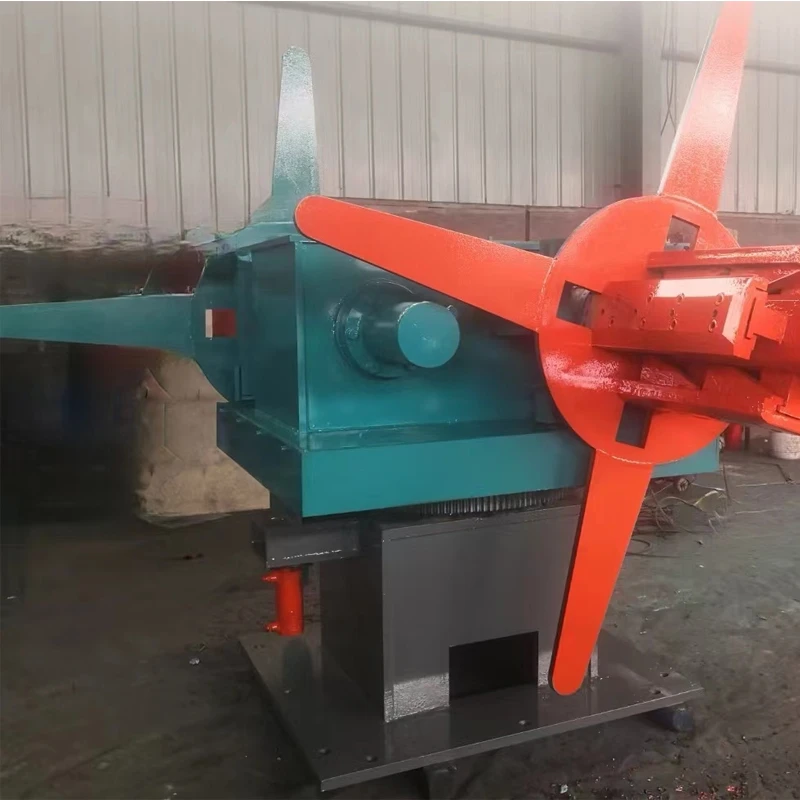
Engineered for excellence, orbital pipe welding machines cater to industries ranging from aerospace to pharmaceuticals. At the heart of its design lies the need for repeatability and precision, crucial in environments where even the smallest imperfection can lead to significant consequences. The closed-loop mechanized system of orbital welding ensures that each weld is identical, an aspect that is particularly important when dealing with high-stakes materials like stainless steel and titanium.
One of the most remarkable aspects of orbital pipe welding is its capacity to eliminate human error. Traditional welding methods often rely heavily on the skill and consistency of the welder, introducing variability that can be detrimental to specific applications. Orbital welders, by contrast, automate the process, using a computer-controlled program to achieve the desired weld specifications each time. This not only enhances the quality of the weld but also significantly reduces the time and cost involved in training skilled welders.
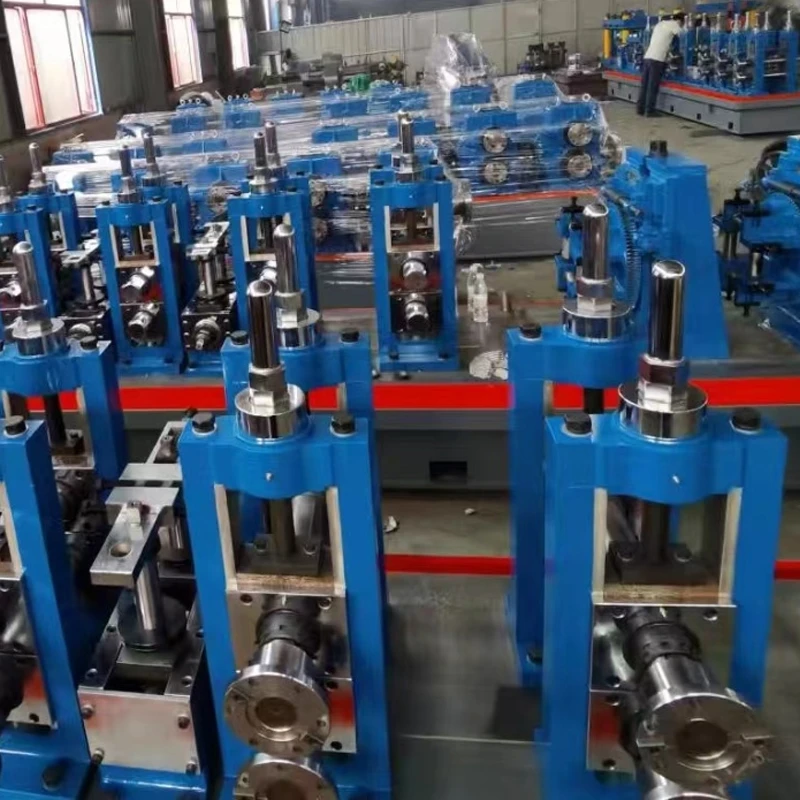
The expertise embedded in the design of each machine showcases their authority in the welding domain. Leading manufacturers employ advanced technology and rigorous testing protocols to ensure these machines meet international standards and certifications, such as ASME and AWS. What this translates to in practical terms is a level of credibility and trust that industries increasingly rely on. Companies often select orbital welding equipment not only for its performance but also for the assurance of meeting regulatory compliance, thereby avoiding potential legal and safety pitfalls.
A testament to their trustworthiness, these machines come equipped with features that simplify complex tasks. The ability to program multiple welding parameters allows for adaptability across different projects and materials. This flexibility is further enhanced by the machines' capability to document each weld, providing a complete traceability log which is crucial for quality assurance and auditing processes.
orbital pipe welding machine
Expert technicians often assert that the initial investment in orbital welders is offset by their long-term advantages. The reduction in material wastage, coupled with decreased downtime and increased production speeds, results in a compelling return on investment. Industries that have adopted this technology report not only enhanced product integrity but also an overall boost in operational efficiency.
Those seeking to harness the full potential of orbital pipe welding machines are advised to partner with reputable suppliers who offer comprehensive training and support services. Expert guidance during initial setup and routine maintenance can maximize the functionality of these machines, ensuring continued precision and reliability.
In recent years, the development of portable orbital welders has opened new possibilities for on-site applications, further broadening the scope of projects that can benefit from this technology. Whether in the construction of a new pipeline or the retrofitting of existing systems, the adaptability and precision of orbital pipe welding machines redefine what is achievable in modern welding applications.
In conclusion, orbital pipe welding machines stand as paragons of innovation in industrial welding. Their precision, reliability, and efficiency not only streamline operations but also set new standards in high-quality weld production. By investing in these machines, industries underscore their commitment to excellence, safety, and compliance, ensuring they remain at the forefront of technological advancement.