On-site pipe cutting machines are the unsung heroes of industries that rely on precision and efficiency. These machines are revolutionizing how pipes are prepared and installed across the globe. Their versatile applications are undeniable, ranging from construction and manufacturing to emergency maintenance.
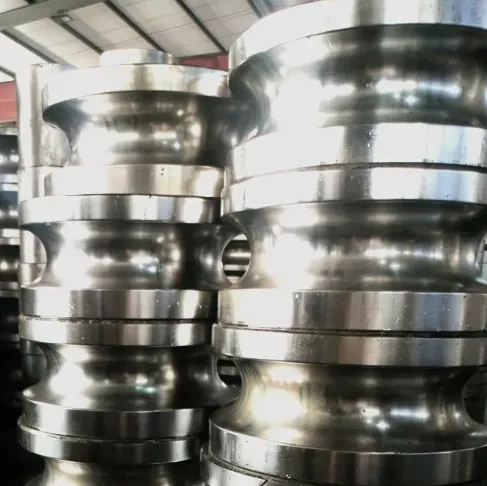
Unlike the cumbersome pipe cutting methods of yesteryears, modern on-site pipe cutting machines bring cutting-edge technology directly to the operation field. They reduce downtime, boost productivity, and, crucially, maintain the integrity of the pipes. With our extensive experience,
we’ve identified what sets top-tier on-site pipe cutting machines apart.
Experience in the field reveals that these machines dramatically cut down the manual labor required. A key observation is that they operate seamlessly in confined spaces, something manual operations struggle with. In the oil and gas industry, for example, where every second counts, these machines have transformed workflows, enabling teams to undertake pipe modifications swiftly and safely.

Expertise is evident in the technical features these machines boast. They frequently utilize CNC (Computer Numerical Control) technology, which ensures precision down to millimeters. This precision is consequential in industries where even the slightest deviation can lead to large-scale safety liabilities. Many machines are designed to handle various pipe materials—stainless steel, carbon steel, and even exotic alloys—without compromising on accuracy or speed.
Our esteemed engineers highlight that these machines often come with modular designs. This feature allows for quick adjustments according to the pipe’s diameter and thickness. Whether working on pipelines of vast industrial facilities or constructing water systems in urban developments, adaptability remains a cornerstone attribute. Additionally, advanced models offer real-time analytics, letting operators assess the progress and make informed decisions on-the-fly.
on site pipe cutting machine
When talking about Authoritativeness, brands specializing in these machines invest heavily in research and development. A paramount example is how some manufacturers collaborate with industrial leaders to tailor solutions to specific sector needs. Such collaborations have birthed ingenious innovations, such as plasma cutting technology, which minimizes deformation in delicate pipes. Stakeholders can rest assured of the machinery’s quality given these firms’ commitment to rigorous testing and compliance with international safety and efficiency standards.
Trustworthiness is reinforced by how these machines enhance workplace safety. Traditional cutting methods often expose workers to sharp tools and hazardous environments. With remote-operated or automated features, on-site pipe cutting machines significantly mitigate these risks. The reduction in accident rates is palpable, making them indispensable in settings where safety protocols are a top priority.
Moreover, maintenance of these machines is straightforward, often requiring minimal intervention due to robust build quality and high-grade materials used in their manufacturing. Their reliable performance over years establishes them as prudent long-term investments.
In conclusion, on-site pipe cutting machines have proven themselves invaluable across multiple industries, offering unparalleled precision, efficiency, and safety. They embody the fusion of technological innovation and practical usability. As experts, our insights into their application not only emphasize their technical prowess but also underline their indispensable role in advancing industrial capabilities. This technology represents the future of pipe handling, ensuring operations are not only smoother but also set to higher standards of excellence.