Orbital pipe welding machines have revolutionized the field of pipe welding, setting a new standard for precision, efficiency, and reliability. These specialized machines are engineered for the automation of welding activities, primarily in industries where superior weld quality is crucial. The integration of orbital welding into pipe manufacturing processes has profound implications, which underscores the importance of understanding its intricacies and benefits.
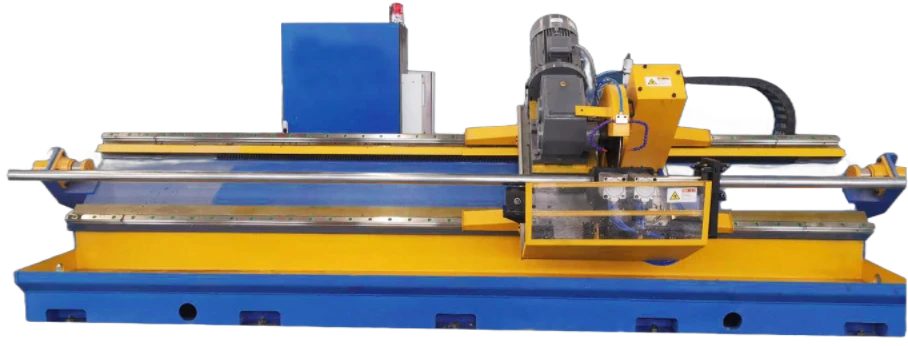
For starters, orbital pipe welding machines are renowned for their unparalleled precision. Unlike traditional welding methods, these machines offer a level of accuracy that is difficult to achieve manually. The orbital system goes around the pipe in a 360-degree motion, ensuring a uniform weld bead that is both structurally sound and aesthetically pleasing. This precision minimizes the likelihood of defects or inconsistencies, thereby reducing the need for costly reworks or repairs.
Moreover,
the efficiency of orbital pipe welding cannot be overstated. The automation inherent in these machines significantly decreases the time required for welding operations. This time efficiency does not merely result in faster project completion; it also translates into considerable cost savings. Projects that might have required extended schedules due to manual welding can now reach completion much quicker, freeing up valuable resources.
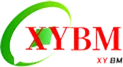
When discussing the expertise embodied in orbital pipe welding machines, one cannot ignore their ability to handle a wide variety of materials and configurations. Whether dealing with stainless steel, titanium, or other alloys, these machines are flexible enough to adapt to the requirements of diverse industrial applications. This adaptability is a testament to their advanced engineering and design, offering solutions to industries ranging from pharmaceuticals and food processing to oil and gas.
orbital pipe welding machine
In the domain of authoritativeness, the orbital pipe welding machine stands as a pillar of technological advancement. Several high-profile industries have already integrated this technology into their production lines, citing its reliability and consistent performance. The machine is equipped with sophisticated software capable of storing specific welding parameters, thus enabling repeatable and traceable results. Such features bolster its reputation as a staple tool in industries requiring the highest standards of weld integrity.
Trustworthiness is another pillar supporting the widespread use of orbital pipe welding machines. These machines undergo rigorous testing to ensure they meet international safety and quality standards. Manufacturers provide detailed documentation on operation, maintenance, and safety procedures, which adds an extra layer of trust. Additionally, many suppliers offer comprehensive customer support, ensuring that users can rely on expert assistance whenever needed.
Real-world testimonials further enhance these machines' credibility. Industry professionals consistently commend them for their durability and performance, often stating that these machines have become integral components of their operational workflow. Such endorsements from seasoned experts are invaluable, providing assurance to prospective users pondering the transition to automated welding.
In conclusion, the orbital pipe welding machine exemplifies the pinnacle of modern welding technology. Its precision, efficiency, adaptability, authoritative design, and robust trustworthiness make it an indispensable tool across numerous industries. As technology continues to evolve, the capabilities and applications of orbital welding machines are set to expand, offering ever more sophisticated solutions to meet the demands of future industrial challenges. Such innovations not only boost productivity but also set new benchmarks in quality and reliability, promising a bright future for industries poised to embrace this transformative technology.