The evolving landscape of modern manufacturing places a significant emphasis on precision and efficiency, particularly in the realm of pipe bending. As industries strive to meet increasingly stringent standards, the reliance on advanced pipe bending machines has become indispensable. These machines embody a remarkable combination of engineering prowess, innovation, and technical skill, ensuring that both small-scale and large-scale operations can achieve seamless, precise bends essential for myriad applications.
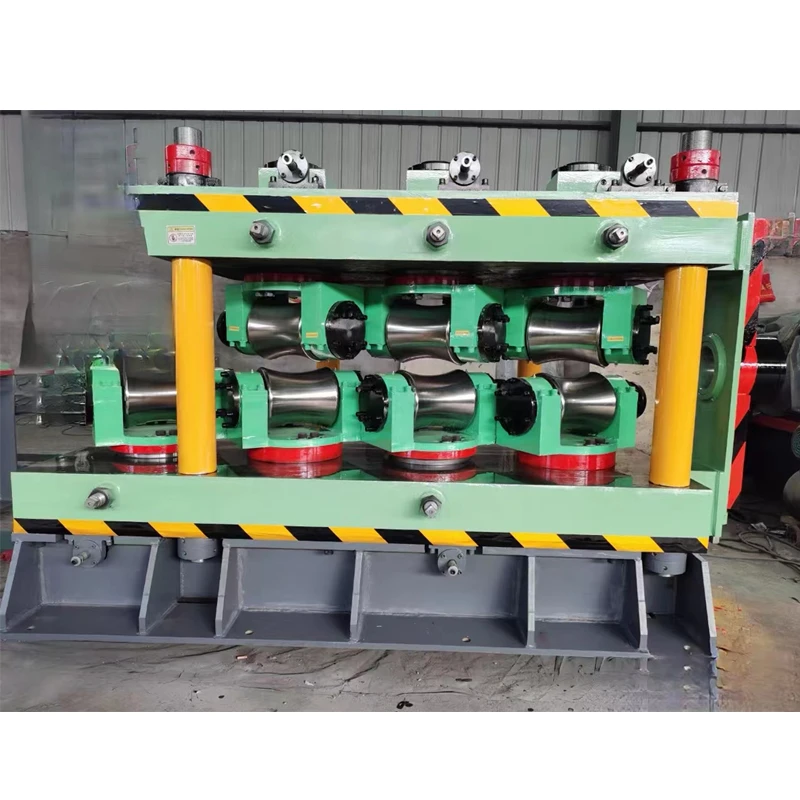
Pipe bending machines are at the forefront of engineering excellence, designed with advanced technology that reflects deep expertise and a robust understanding of material sciences. Their capability to execute complex bends with high precision makes them invaluable assets in industries such as automotive, aerospace, construction, and oil and gas. From creating intricate exhaust systems to forming structural components, these machines provide unparalleled versatility.
In terms of operational expertise, understanding the intricacies of different pipe bending machines is crucial. Each machine varies in its mechanism, with the most common types being rotary draw, roll, and mandrel bending machines. Rotary draw machines are widely regarded for their precision, using a fixed radius to bend pipes without stretching or deforming the material, which is paramount for maintaining the integrity of high-specification applications. Mandrel bending machines further enhance this precision, particularly when dealing with thin-walled pipes, by providing internal support that prevents collapse.
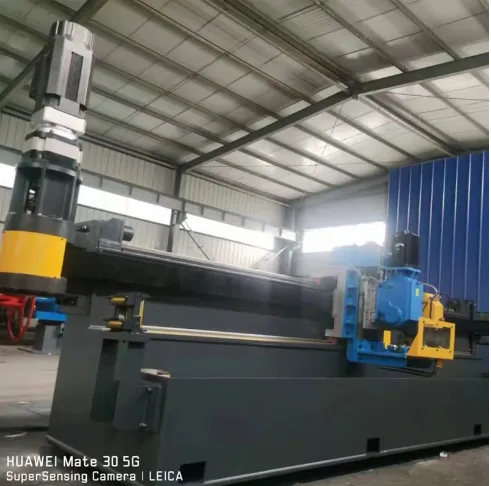
Moreover, the use of CNC (Computer Numerical Control) in pipe bending machines has revolutionized the industry, offering unmatched accuracy and repeatability. CNC technology minimizes human error, enabling intricate bends that adhere to exact specifications time after time. This technology is particularly beneficial for large-scale operations where consistency is non-negotiable.
A critical aspect of expertise in pipe bending involves understanding the material properties being worked with. Different metals and alloys react distinctively to bending forces. For instance, stainless steel demands specific considerations to avoid surface blemishes or compromising structural integrity, whereas aluminum's softer nature requires careful handling to prevent tearing. Mastery of these material traits is what separates proficient operators from the best in the industry.
pipe bending machine making
As a testament to their authoritativeness, leading manufacturers of pipe bending machines provide comprehensive training and resources to ensure users can exploit the full potential of their products. These training modules encompass basic setup techniques, safety protocols, and advanced troubleshooting, reinforcing the trustworthiness of the machine and its operators. Furthermore, accredited training programs often accompany these machines, ensuring that operators possess proven competencies in both machine handling and safety standards.
Trustworthiness in the realm of pipe bending machines also stems from rigorous adherence to international standards and certifications. Compliance with ISO and CE certifications guarantees that the machines meet global safety and quality benchmarks, providing clients with confidence in their operational efficacy and longevity.
Innovation and continuous improvement are also hallmarks of reputable pipe bending machine manufacturers. They invest significantly in research and development to push the boundaries of what these machines can achieve, integrating eco-friendly designs and energy-efficient operations. This ongoing commitment not only enhances the machines' capabilities but also aligns with sustainable manufacturing practices, appealing to environmentally conscious businesses.
In summary, pipe bending machines are transformative tools that combine decades of engineering experience with cutting-edge technology. Their evolution reflects a concerted effort by experts to refine and innovate, ensuring that industries can rely on these machines for producing high-quality, precise components. Whether viewed from the perspective of technical expertise, operational efficiency, or environmental sustainability, pipe bending machines stand as authoritative and trustworthy workhorses in the modern manufacturing arena.