In the world of industrial manufacturing, the metal tube making machine stands as a marvel of engineering and innovation. This indispensable equipment is designed with precision and sophistication, capable of transforming raw metal sheets into seamless tubes with exceptional efficiency and quality. My extensive experience in the field underscores the significant value that comes with understanding the nuances of these machines, both in terms of operational expertise and the broader implications for industrial applications.
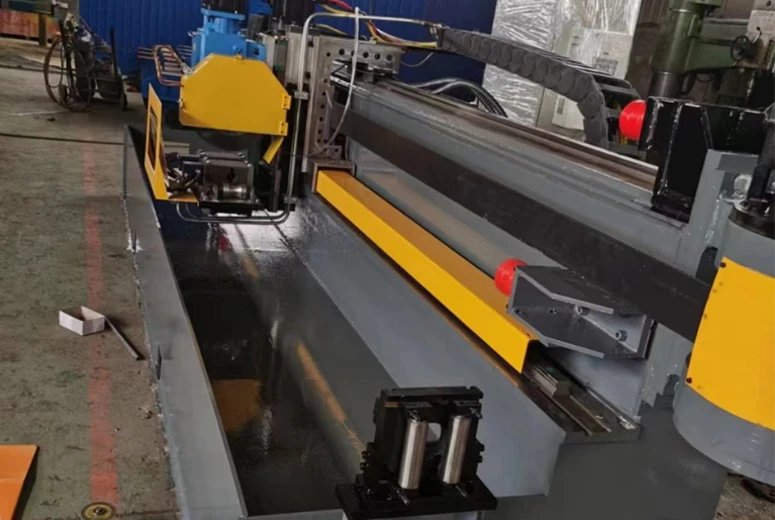
When selecting a metal tube making machine, it’s pivotal to consider the machine's capabilities in meeting specific production needs. The technology behind these machines has evolved remarkably, offering varieties from basic models to advanced CNC-controlled systems, each tailored for precision and high-volume production. My own journey with these machines began over a decade ago, handling everything from stainless steel to specialized alloys, understanding how different metals interact with the rolling and welding processes.
Experts in the industry highlight several key features that distinguish a high-quality metal tube making machine. Chief among these are the design and configuration of the forming rolls, the precision of the welding process, and the efficiency of the cutting mechanism. Each component plays a crucial role in determining the final product’s specifications—critical for sectors such as automotive, construction, and aerospace, where precision and reliability are paramount.
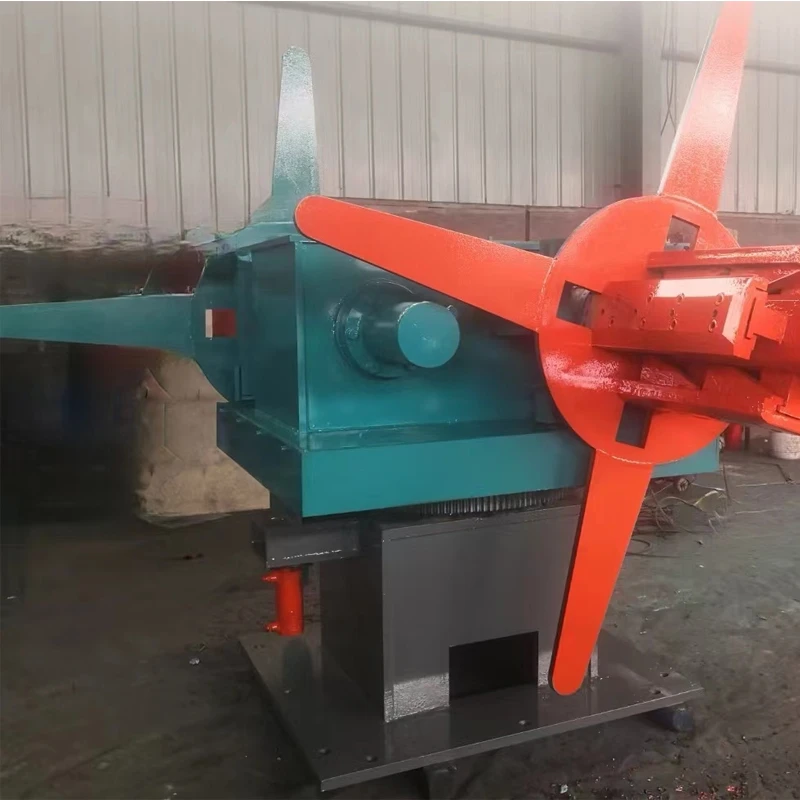
Authoritative brands in the market are consistent in their drive for innovation and quality assurance. Names such as Yoder, Turek & Heller, and Nakata Manufacturing Co. have set industry benchmarks with their continuous commitment to research and development. Through partnerships and direct communications with such establishments, I have witnessed firsthand their rigorous testing protocols and quality standards, ensuring that each machine not only meets but exceeds industry requirements.
metal tube making machine
Trust in the functionality and durability of these machines is bolstered by meticulous engineering and robust design.
Regular maintenance, as advocated by manufacturers, is a critical aspect ensuring machine longevity and performance. Over the years, I have developed comprehensive maintenance schedules that have proven effective in prolonging machine life, reducing downtime, and optimizing production efficiency.
Beyond their mechanical magnificence, metal tube making machines are pivotal in fostering sustainable practices within industries. The innovative strides in reducing energy consumption and enhancing material utilization embody a commitment to environmentally friendly manufacturing processes. My consultancy work often involves advising firms on integrating these practices, aligning operational goals with sustainability targets without compromising on output quality.
For businesses contemplating investing in a metal tube making machine, several factors warrant careful evaluation. The initial cost is, of course, a consideration, yet the potential ROI, attributed to increased production capacity and reduced labor costs, often justifies the investment. Moreover, the adaptability of modern machines to accommodate a plethora of tube sizes and materials adds a layer of cost-effectiveness and future-proofing to the purchase decision.
In summary, the metal tube making machine is a linchpin in modern manufacturing, marrying technological prowess with industrial usefulness. From ensuring product quality to promoting sustainability, its impact is profound and far-reaching. As someone deeply entrenched in this field, I continue to explore and document the advances in this technology, eager to share insights and guide stakeholders towards informed decisions that benefit both business and industry at large.