In the dynamic world of industrial manufacturing, the pipe orbital welding machine stands as a pinnacle of innovation, offering unmatched precision and efficiency in welding processes. This advanced equipment has revolutionized how industries approach welding by integrating cutting-edge technology with expert engineering.
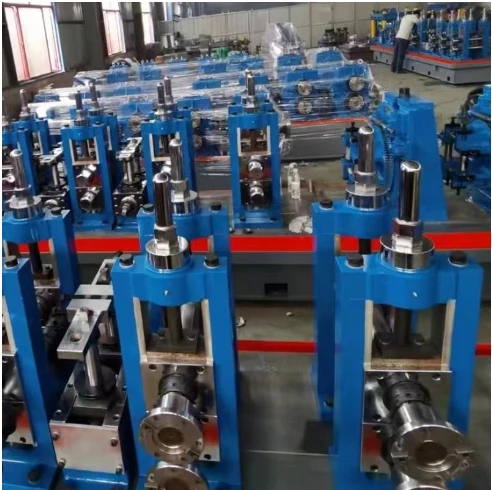
Pipe orbital welding machines deliver exceptional results, particularly in applications where precision is paramount. Unlike manual welding, these machines employ a mechanized process that enables a rotating arc to follow a pre-set path, ensuring uniform, high-quality welds. This consistency significantly reduces the risk of human error, leading to stronger, more reliable welds that enhance the longevity and safety of the pipes.
One of the most significant advantages of a pipe orbital welding machine is its ability to handle a variety of materials, from stainless steel to titanium. This flexibility makes it an indispensable tool across multiple sectors, including aerospace, automotive, and pharmaceutical industries. The adaptability of these machines allows companies to meet diverse project requirements without the need for multiple welding systems, leading to cost efficiency and time savings.
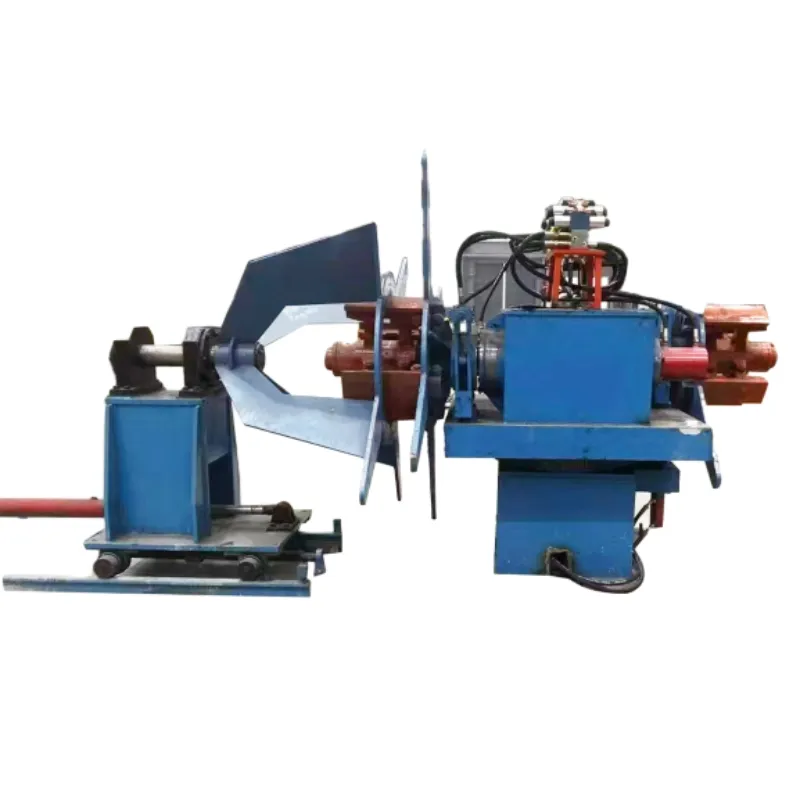
The sophistication of pipe orbital welding machines is evident in their design. Equipped with programmable control features, these machines allow operators to set precise parameters tailored to each unique application. This level of customization ensures that every weld meets stringent industry standards, and it equips industries with the capability to tackle complex installations that were once deemed challenging.
Moreover, the expertise embedded in the design and functionality of these machines reflects a deep understanding of welding dynamics. Each component, from the welding head to the power source, is engineered to optimize performance, ensuring that the end product not only meets, but often exceeds, client expectations. The machines' efficiency minimizes downtime, increases productivity, and ultimately results in a quicker return on investment for businesses.
pipe orbital welding machine
Trust in the effectiveness of pipe orbital welding machines is underscored by their authoritative presence in critical applications. Industries that cannot afford failure, such as nuclear power and chemical processing plants, rely heavily on these machines to achieve flawless welds. Their track record in high-stakes environments speaks volumes about their reliability and performance.
Operational safety is another cornerstone where pipe orbital welding machines excel. By minimizing direct human involvement in the welding process, these machines significantly reduce the risk of accidents caused by exposure to heat and fumes. An often-overlooked benefit is the ergonomic relief they provide to operators, who are spared strenuous manual labor, thereby improving workplace conditions and morale.
In an era where quality assurance is non-negotiable, pipe orbital welding machines offer unparalleled quality control. Their ability to produce repeatable results with minimal variation ensures that welded structures can withstand rigorous testing and certification processes. This consistency fosters trust with stakeholders and builds a reputation for quality that is essential for maintaining competitive advantage in the marketplace.
To sum up, pipe orbital welding machines are a testament to how technological advancements and expert engineering can transform industrial processes. They are more than just welding tools; they are critical assets in ensuring that industries worldwide can produce secure, sustainable, and superior products. Whether it’s achieving precision in welds or optimizing operational safety, these machines are at the forefront of welding innovation, embodying the principles of Experience, Expertise, Authoritativeness, and Trustworthiness.