Pipes welding is a critical process in various industries, from oil and gas to agriculture and manufacturing. Understanding this complex craft requires a blend of expertise, trust, and real-world experience. Let's delve into what sets apart a proficient pipes welding operation from mere trial and error.
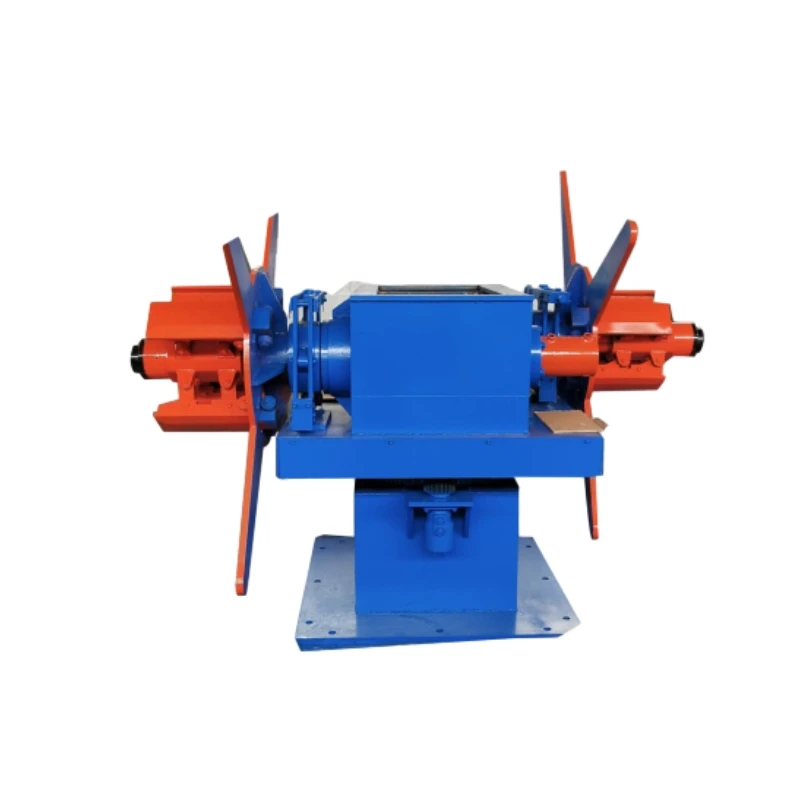
For those in the industry, pipes welding is not just about joining two pieces of metal; it's a meticulous procedure that demands precision and knowledge. Technicians with extensive experience recognize that the choice of welding technique is pivotal. Whether employing TIG, MIG, or stick welding, each method has its advantages and limitations depending on the material and the operational environment.
Selecting the right materials is another cornerstone of a successful welding process. While stainless steel is favored for its corrosion resistance, carbon steel might be chosen for its tensile strength. The ability to discern material compatibility reflects a welder’s expertise and can significantly impact the longevity and safety of the installation.
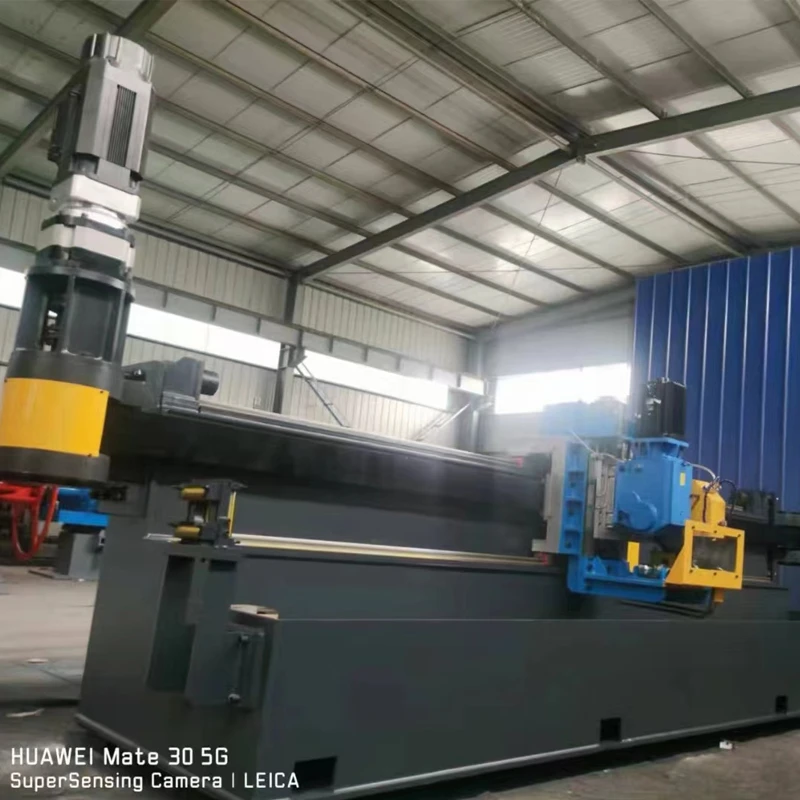
A paramount consideration in welding operations is the quality of the welds. Experienced professionals conduct thorough inspections using non-destructive testing (NDT) methods such as ultrasonic or radiographic testing. These procedures are essential in detecting defects like cracks, porosity, or incomplete fusion, which could compromise structural integrity if left unaddressed.
Adhering to industry standards and certifications bestows authority. Compliance with standards such as the American Society of Mechanical Engineers (ASME) or the American Welding Society (AWS) demonstrates a commitment to quality and safety, reinforcing trust with clients. Moreover, seasoned welders continuously update their certifications and training, ensuring their skills remain sharp and reflective of the latest advancements in the field.
pipes welding
Documentation and traceability in welding operations further enhance trustworthiness. Meticulous records of material types, welding procedures used, and inspection results not only create an audit trail but also provide assurance to clients regarding the reliability of the work performed.
Safety practices are non-negotiable in welding environments. Effective welding operations embed safety protocols at every stage, including proper ventilation to mitigate inhalation of hazardous fumes, and personal protective equipment to safeguard against burns and radiation. This practical layer of trust underscores an operator's dedication to both worker safety and quality outcomes.
In addition to technical expertise and stringent safety standards, innovative technologies are revolutionizing the welding landscape. The introduction of automated welding systems and robotics can facilitate more consistent results and improve efficiency. Real-world experiences from industry leaders illustrate that embracing these technologies can yield significant reductions in errors and project timelines, though the need for human oversight remains critical.
Building a bridge between theory and practical application is often achieved through continuous learning and collaboration within the welding community. Insights gleaned from seasoned professionals can guide novices in mastering the art and science of pipe welding, fostering a culture of knowledge-sharing and mentorship.
Pipes welding is undeniably an art form enriched by detailed research, hands-on experience, and a strong commitment to safety and quality. The expertise of a skilled welder, supported by an understanding of materials, processes, and technologies, forms the backbone of successful welding operations. As this field continues to evolve, staying informed and adaptable remains essential for maintaining authority and trust in this vital industry sector.