In the intricate field of piping systems, welding plays a crucial role, requiring a blend of skill, precision, and experience. For industries such as petrochemicals, construction, and manufacturing, understanding the nuances of pipe welding not only ensures durability but also enhances the safety and reliability of entire infrastructures. This article delves into the world of pipe welding, providing insights drawn from years of expertise and highlighting why it remains an authoritative method in pipeline construction.
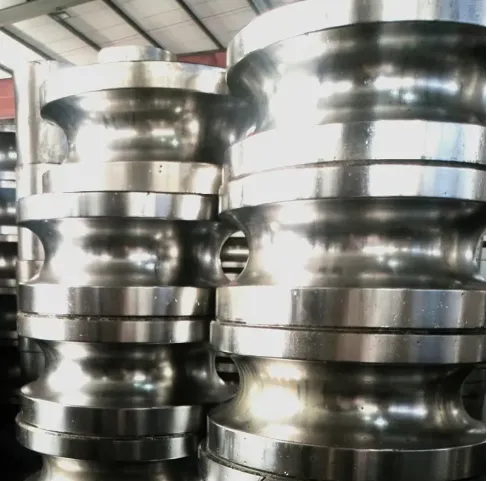
Pipe welding is an art form that marries craftsmanship with scientific understanding. Master welders are revered for their ability to create flawless seams under daunting conditions. Their expertise goes beyond merely joining pipes; it involves assessing variables such as material compatibility, environmental conditions, and intended pressure loads. This depth of knowledge is critical in preventing future systemic failures and extending the lifespan of the pipeline.
Materials play a pivotal role in the pipe welding process. With varying thermal and physical properties, materials like carbon steel, stainless steel, and alloys require specific welding techniques. For instance, carbon steel pipes are widely used due to their strength and flexibility, but welding them demands an acute understanding of preheating and post-weld heat treatment. These pre-weld preparations help mitigate temperature-induced stresses that might lead to cracking.
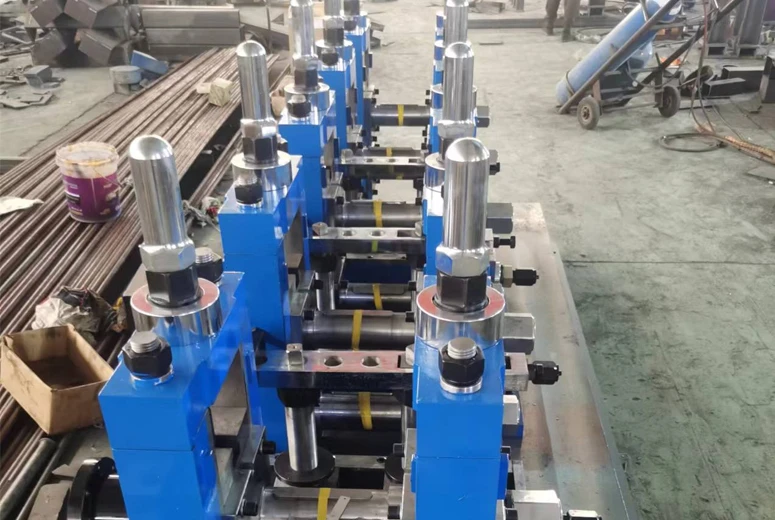
The choice of welding method significantly impacts the quality and efficiency of pipe connections. Techniques such as Shielded Metal Arc Welding (SMAW), Tungsten Inert Gas (TIG), and Gas Metal Arc Welding (GMAW) each have specific advantages tailored to different operations. TIG welding, for example, is particularly valued for its precision and ability to produce clean, high-quality welds without spatter, making it ideal for projects requiring immaculate joins. However, it requires a high degree of skill and is considerably slower compared to other methods.
In contrast, SMAW, commonly known as stick welding, is renowned for its versatility and adaptability in various environmental conditions. It remains one of the most resilient methods for outdoor pipe welding projects, offering robust performance against wind and rain. The expertise in electrode selection and amperage adjustments are fundamental for achieving optimal penetrative welds with this method.
Quality assurance in pipe welding cannot be overstated. Non-destructive testing (NDT) techniques are indispensable tools in the welder's arsenal, ensuring weld integrity without compromising the material's structural integrity. Ultrasonic testing and radiographic inspections are two of the most authoritative approaches, providing detailed insights into potential anomalies like porosities and inclusions. These tests are paramount in maintaining safety standards and have become industry benchmarks.
pipes welding
Trust in pipe welding extends to regulatory compliance. Industry standards from organizations such as the American Welding Society (AWS) and the American Society of Mechanical Engineers (ASME) provide comprehensive guidelines that govern the welding processes. Adhering to these standards is not merely a legal obligation but a testament to a company's commitment to excellence.
With technological advancements, pipe welding has witnessed significant innovations. The advent of automated welding machines has introduced a level of precision unattainable through manual methods alone. These machines operate with remarkable consistency, reducing human error and enhancing productivity. However, the human element remains irreplaceable, as skilled operators are essential in programming machines and overseeing the welding process.
Moreover, safety is an omnipresent concern in the field, underscored by rigorous training programs and safety protocols. Welders are continually educated about the hazards of exposure to fumes, ultraviolet radiation, and high temperatures. Personal protective equipment (PPE) and adequate ventilation are mandatory to safeguard workers' health, demonstrating the industry's dedication to creating safer working environments.
The future of pipe welding holds promise, influenced by the integration of artificial intelligence and augmented reality to assist welders in real-time. These technological enhancements aim to elevate the craft, offering predictive analytics and enhancing skill training to meet the ever-evolving demands of the industry.
In summary, pipe welding is not merely a technical task but a pivotal component of industrial infrastructure development. Mastery in this field demands expertise, experience, and a steadfast commitment to quality and safety. As technologies continue to advance and standards evolve, pipe welding will undoubtedly remain an indispensable craft, underpinned by its authoritative place in ensuring the seamless function of piping systems worldwide.