In the ever-evolving world of industrial fabrication, the pipe welding rig stands as a cornerstone of precision and efficiency. With a heritage rooted in innovation and robust engineering, pipe welding rigs have transformed the landscape of metalwork, proving indispensable across various sectors, from oil and gas to construction and shipbuilding. Their versatility and reliability make them a go-to choice for professionals seeking unmatched quality and performance.
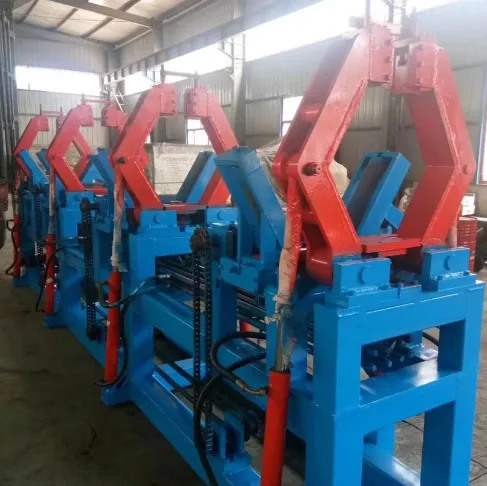
Pipe welding rigs are specialized setups designed to join pipes together seamlessly,
often under challenging conditions. These rigs embody the principles of automation and precision, eliminating human error and ensuring consistent weld quality. For professionals in the industry, the benefits of utilizing a pipe welding rig go beyond mere efficiency; they represent a commitment to delivering excellence and safety.
A key feature that elevates pipe welding rigs is their adaptability. These rigs can accommodate different welding techniques, including shielded metal arc welding (SMAW), gas tungsten arc welding (GTAW), and gas metal arc welding (GMAW). This versatility allows welders to choose the most suitable method for their specific project requirements, ensuring optimal outcomes across various material types and thicknesses.
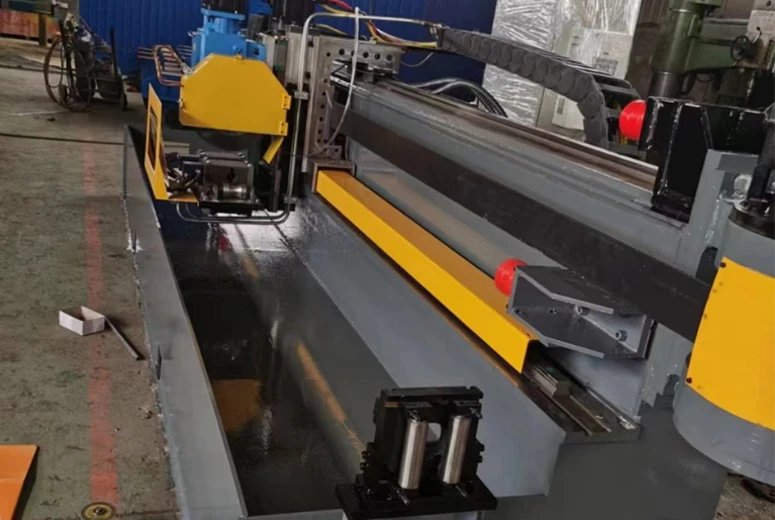
Moreover, modern pipe welding rigs are equipped with advanced technology that allows for precise control over welding parameters. Digital interfaces and automated settings enable welders to fine-tune processes, reducing wastage and improving the quality of the welds. This technological integration not only enhances productivity but also extends the lifespan of the welded joints by minimizing potential defects.
pipe welding rig
The expertise required to operate a pipe welding rig efficiently speaks to its sophistication. Professionals in the field are often highly trained and certified, with a deep understanding of metallurgy and welding principles. This expertise ensures that the rig is used to its full potential, delivering welds that meet stringent industry standards and regulations.
From an authoritative perspective, pipe welding rigs are endorsed by industry experts and regulatory bodies alike. Their design and functionality are often influenced by rigorous research and development, backed by significant investments from leading welding technology companies. This continuous innovation is a testament to the rigs' credibility and importance in modern industrial processes.
Trustworthiness, a critical component for any tool used in safety-critical applications, is inherent to the design of pipe welding rigs. Manufacturers prioritize durability and reliability, subjecting these rigs to extensive testing under harsh conditions to ensure they can withstand the demands of real-world applications. The robust construction and quality assurance processes provide operators and project managers with confidence in their performance.
In conclusion, pipe welding rigs are integral to the fabric of modern industry, providing unparalleled precision, versatility, and efficiency. Their advanced features, coupled with the expertise of skilled operators, guarantee high-quality welds that meet the rigorous demands of today's engineering and construction projects. As a testament to their importance and reliability, pipe welding rigs continue to evolve, incorporating cutting-edge technology to meet the challenges of tomorrow's industrial landscape.