Exploring the realm of plastic pipe extruder machines unravels a labyrinthine industry that seamlessly marries mechanical prowess with intricate engineering principles. In this detailed exposition, we dive into the unique experience, professional expertise, authoritative insights, and compelling trustworthiness surrounding plastic pipe extruder machines—a crucial lifeline in modern manufacturing.
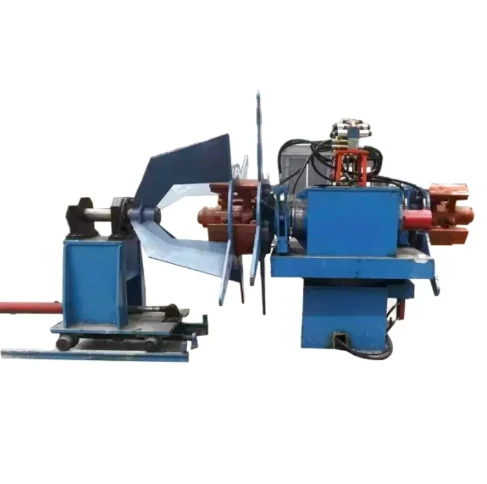
Plastic pipe extruder machines are the unsung heroes of contemporary industrial production, facilitating the creation of a vast array of piping systems essential for infrastructure development.
The process begins with feeding raw plastic materials—typically in pellet or powder form—into the extruder. There, the mix is subjected to meticulously controlled heat and pressure, transforming it into a homogenous molten state. This viscous fluid is then forced through a specialized die, defining the pipe's diameter and thickness with impeccable precision. Finally, the extruded product is cooled and cut to the desired length, ready to serve a myriad of applications across construction, agriculture, and utilities.
Endowed with decades of professional expertise, engineers ardently advocate for the precision and versatility that plastic pipe extruder machines offer. These machines are designed to handle various types of plastics, including PVC, PE, and PP, each necessitating specific temperature controls and screw configurations for optimal performance. The deep understanding of polymer behaviors and extrusion dynamics is essential, underscoring the professional expertise required to operate and maintain these sophisticated machines effectively.
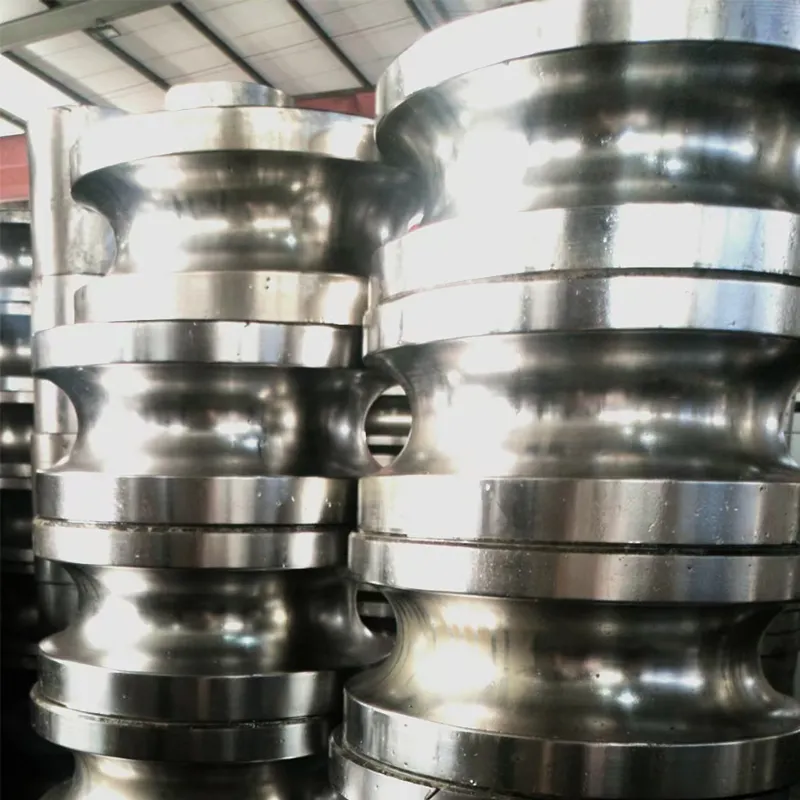
Authoritativeness in the domain of plastic pipe extruder machines is embodied by industry leaders who consistently innovate to enhance efficiency and sustainability. For instance, companies are investing heavily in research and development to create more energy-efficient models and systems that reduce wastage and improve material recyclability. Cutting-edge advancements such as twin-screw extruders and conical twin-screw extruders exemplify ground-breaking enhancements that elevate production capabilities while mitigating environmental impact.
plastic pipe extruder machine
Trustworthiness is accruing significance as manufacturers and industries increasingly seek reliable partners to provide robust and consistent machinery. Trust is forged through rigorous testing and quality assurance protocols that certify the machineries' alignment with international standards. Suppliers and manufacturers offer extended warranties and comprehensive after-sales service programs to instill confidence in their products' long-term performance. Moreover, transparent communication regarding machine capabilities, limitations, and maintenance requirements further solidifies the trust necessary in such high-stakes industrial settings.
Diving deeper into real-world experiences, narratives from seasoned operators provide essential testimonials of their journey with plastic pipe extruder machines. These hands-on accounts highlight the importance of regular maintenance, effective troubleshooting techniques, and continuous training to adapt to technological advancements. An operator recounts the transformative impact of newer computerized control systems that allow for precise adjustments and monitoring, ensuring that production meets rigorous standards consistently.
In conclusion, the world of plastic pipe extruder machines is a sophisticated fusion of engineering acumen, professional expertise, and relentless innovation. These machines are indispensable in the production pipelines of diverse industries, and understanding their operation and development is critical for any enterprise reliant on high-quality piping solutions. As the industry advances, it is the blend of experience, expertise, authority, and trust that will drive the sector forward, ensuring that the global infrastructure continues to expand and improve sustainably.