Production cold saws have transformed the landscape of industrial metal cutting, offering precision and efficiency that meets the stringent demands of today's manufacturing environments. Leveraging years of on-the-ground experience and expertise, this article delves into the nuances of selecting the right cold saw to enhance production capabilities. As an authoritative source, the insights provided here are crafted to offer a trustworthy guide for businesses looking to optimize their cutting processes.
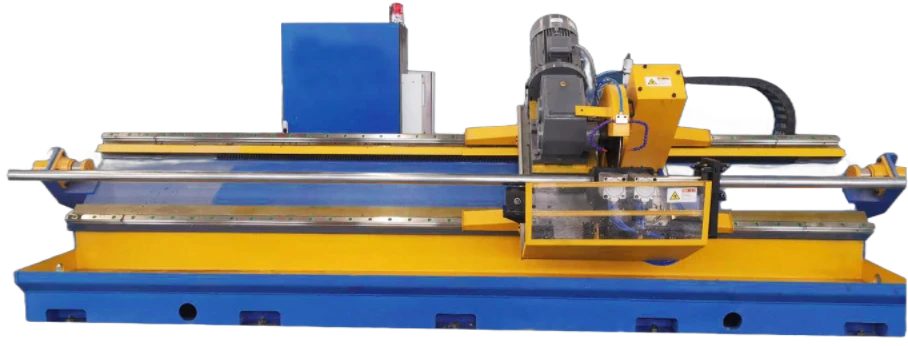
Cold saws are engineered for precision and speed, making them indispensable in industries such as automotive, aerospace, and construction. Unlike traditional saws, production cold saws utilize a circular blade and a gearbox to maintain cutting integrity and prolong blade life. This technology distinguishes itself through the ability to make clean cuts without heat distortion, a critical factor in maintaining the structural integrity of the workpiece.
Expertise in this domain underscores the importance of blade selection. The choice of blade materials and tooth configuration can significantly influence performance. High-speed steel (HSS) and tungsten carbide-tipped (TCT) blades are popular for their durability and speed. HSS blades are ideal for softer metals and provide excellent wear resistance, whereas TCT blades, with their ability to cut through harder metals, offer longevity and precision. Understanding the operational demands and material specifics is essential in optimizing cutting processes.
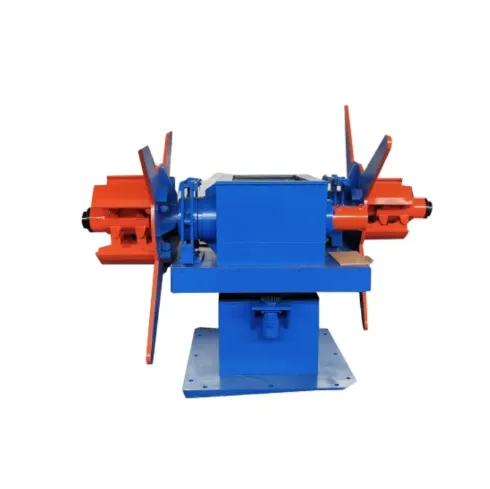
From an expertise standpoint, the integration of cold saws into production lines demands attention to machine configuration and maintenance. Features such as automatic feeding mechanisms, digital controls, and lubrication systems can enhance productivity and extend machine lifespan. Regular maintenance routines, emphasizing blade sharpening and system lubrication, ensure operational efficiency and reduce downtime, thereby increasing throughput.
production cold saw
Authoritative insights stress the importance of safety and training. Operators must be well-versed in machine safety protocols, as cold saws, while efficient, require careful handling. Implementing comprehensive training programs not only safeguards staff but also maximizes machine utilization by minimizing operator error.
Trustworthiness in selecting a supplier cannot be understated. Partnering with a reputable manufacturer ensures access to reliable machines and responsive service. Look for manufacturers that offer comprehensive warranties, after-sales support, and customization options. An established manufacturer will provide the necessary technical support and replacement parts, ensuring operational continuity and peace of mind.
In the realm of production cold saws, embracing innovation is key. With advancements in automation and digital integration, modern cold saws offer features that allow for real-time monitoring and adjustments. This adaptability ensures that machines can meet evolving production needs while maintaining high standards of cut quality.
To conclude, the adoption of production cold saws provides a competitive edge in high-precision metal cutting. A deep understanding of these machines, from blade selection to machine maintenance and safety, is critical for achieving optimal performance. With the right expertise and supplier partnership, production cold saws can revolutionize operational efficiency, making them an invaluable asset in any high-demand production environment.