Ridge forming machines have become a cornerstone in the metal forming industry, serving a myriad of applications from constructing roofing systems to creating durable structural components. This equipment is critical for businesses aiming to produce consistently high-quality profiles with a high degree of precision and efficiency. For an in-depth understanding of ridge forming machines, it is essential to delve into their operational principles, components, and the advantages they offer over traditional forming methods.
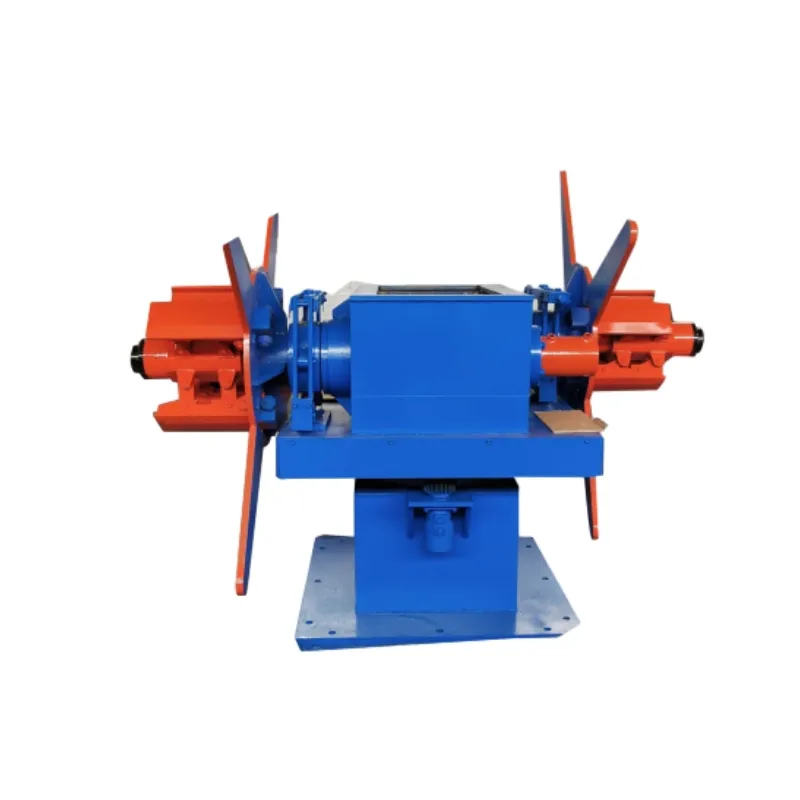
Ridge forming machines utilize rollers to shape metal into a predetermined profile. The process is not only efficient but also ensures uniformity across the length of the material. These machines are designed with specific attention to detail, featuring a series of stations, each responsible for a specific phase of the forming process. This segmented approach allows for superior control over the final product’s shape and strength.
The key components of a ridge forming machine include the decoiler, feeding mechanism, roller stations, cutting system, and control panel. The decoiler is responsible for holding and unwinding the coil of metal, ensuring a smooth and continuous feed into the machine. Feeding mechanisms guide the material accurately to the roller stations, where the actual forming takes place. These rollers are precisely engineered to bend the metal without causing stress fractures or inconsistencies, effectively determining the quality of the finished product.
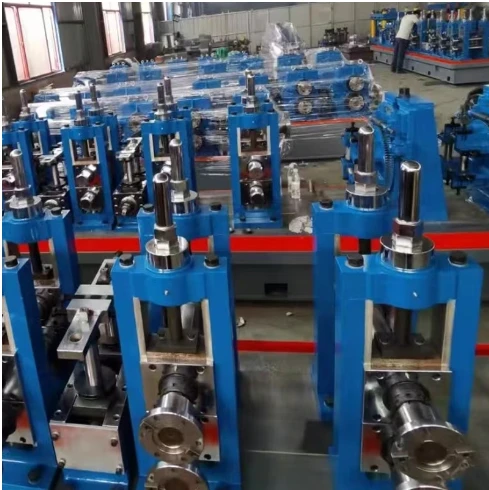
One of the most significant advantages of ridge forming machines is their ability to significantly reduce material wastage. Traditional forming techniques often require excess material to compensate for inaccuracies, but with ridge forming machines, each piece can be formed to precise specifications, minimizing scrap output. This efficiency not only conserves resources but also translates to cost savings for manufacturers.
Another compelling benefit is the machine's adaptability and ease of use. Modern ridge forming machines feature computer-aided controls that allow for quick adjustments to accommodate different dimensions or profiles, making them versatile tools capable of handling a wide range of production requirements. This flexibility is crucial for businesses that need to respond swiftly to changing market demands or custom orders.
ridge forming machine
Furthermore, the automation inherent in ridge forming machines ensures consistent product quality with minimal manual intervention. This reliability enhances the trustworthiness of manufacturers who can guarantee product specifications and quality to their clients. The decreased need for manual labor also reduces human error and increases production speed, directly impacting the bottom line through increased throughput and reliability.
The efficiency and precision of ridge forming machines make them the preferred choice in industries where product integrity and durability are non-negotiable. Industries such as construction, automotive, and aerospace have particularly benefited from the precision and strength these machines offer, enabling them to deliver products that meet stringent regulatory standards and client expectations.
Investing in a ridge forming machine is not just an upgrade in equipment but a commitment to quality and efficiency. Industry leaders recognize the importance of adopting machinery that not only meets current production needs but is also scalable for future demands. By embracing such cutting-edge technology, companies fortify their market positions and set benchmarks in product excellence and innovation.
In conclusion, the ridge forming machine exemplifies advancement in manufacturing technology, combining precision engineering with automated controls to deliver unparalleled efficiency and quality. For manufacturers committed to upholding the highest standards of production, these machines are indispensable assets that secure both market competitiveness and customer satisfaction. As the industry evolves, ridge forming machines will continue to play a pivotal role, driving innovation and setting new standards in metal forming excellence.