Roller die extruders are a transformative innovation within the manufacturing and materials processing industries. Embracing a blend of advanced technology and engineering design, these machines reshape how items can be produced efficiently, cost-effectively, and with precision. The following analysis will delve into the crucial aspects of roller die extruders, emphasizing their impact on production processes, their operational mechanisms, and the industries that benefit profoundly from their use.
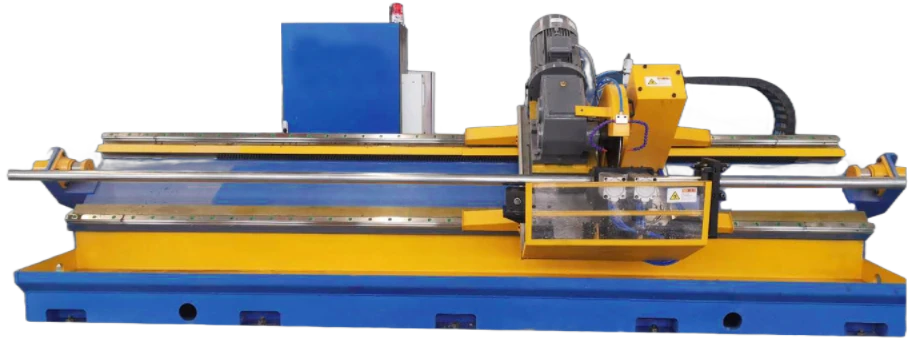
A roller die extruder is a specialized piece of equipment that integrates the function of a roller with a die. This combination serves the primary purpose of shaping and forming materials into desired profiles consistently. The roller die extruder is particularly beneficial for handling complex material compositions that require uniform thickness and texture. Unlike traditional molds, which might not accommodate variable material textures, roller die extruders employ continuous pressure and heat to produce stable and uniform products.
One of the key benefits of using roller die extruders is their ability to handle various materials, including polymers, metals, and soft composites. This adaptability makes them indispensable in industries like automotive, construction, and consumer goods, where diverse material specifications are mandatory. For instance, in the production of automotive seals and gaskets, the precision and consistency provided by roller die extruders ensure that parts meet stringent quality standards, thus enhancing vehicle safety and performance.
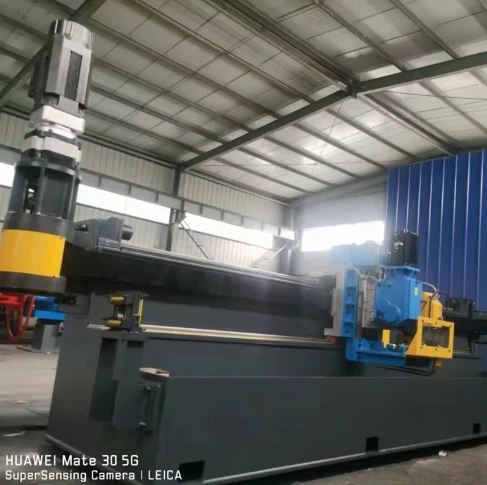
Moreover, roller die extruders contribute significantly to sustainable manufacturing practices. The design of these machines minimizes material waste, as they precisely control the amount of material needed for each product. Additionally, their ability to recycle excess material back into the production cycle aligns with eco-friendly initiatives that many companies are adopting. This not only reduces the carbon footprint of production processes but also enhances the cost-efficiency of manufacturing operations.
From a technical perspective, the operation of a roller die extruder involves several stages, each meticulously designed to ensure the best results. Initially, the chosen material is fed into the extruder, where it is heated to the optimal processing temperature. This stage is crucial as it determines the material's malleability and readiness for shaping. Following this, the material is passed through the die, which dictates the final shape and dimensions of the product. The rollers apply uniform pressure throughout, ensuring a consistent texture and thickness across the entire product surface.
roller die extruder
Despite their advantages, the successful deployment of roller die extruders requires expertise and a deep understanding of both material science and engineering principles. Operators need to be proficient in calibrating the machines to handle different materials and product specifications. Additionally, regular maintenance and monitoring are paramount to ensure the longevity and optimal performance of the equipment.
The evolution of roller die extruders also highlights the broader trend toward automation and precision in manufacturing. With advancements in computer-aided design and manufacturing technologies, roller die extruders are increasingly integrated with digital control systems. These systems allow for greater precision in production and facilitate real-time monitoring and adjustments. As a result, manufacturers can quickly adapt to changing product demands and innovate swiftly in an evolving market landscape.
Industries such as aerospace and electronics are also beginning to explore the possibilities offered by roller die extruders, particularly in reducing production times and increasing the precision of complex components. As the demand for high-quality, reliable, and efficient manufacturing processes grows, roller die extruders will likely continue to play a pivotal role in shaping the future of industrial manufacturing.
In conclusion, roller die extruders are a cornerstone of modern manufacturing, offering unparalleled benefits in terms of precision, efficiency, and sustainability. Companies leveraging this technology are well-positioned to lead in their respective fields, through enhanced production capabilities and by meeting the increasing demands for high-quality products with lower environmental impact. The ongoing innovations and improvements in roller die extruder technology promise a future where manufacturing is not only more efficient but also more adaptable and environmentally responsible.