In exploring the intricate world of roller formers, one uncovers a sophisticated piece of machinery that has revolutionized manufacturing processes across industries. At its core, a roller former is a versatile machine used in the metal forming industry, designed to take sheet or strip material and form it into complex cross-section profiles. These machines are predominantly used in sectors such as automotive, construction, and aerospace, where precision and consistency are non-negotiable.
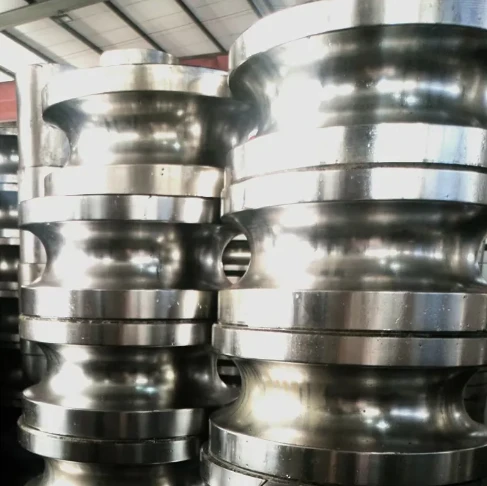
The roller former presents an engineering marvel that distinguishes itself through its ability to produce long profiles in large volumes with high uniformity. Unlike pressing, which might dent or distort materials under stress, roller forming maintains the integrity of the material, yielding superior results. This process not only enhances efficiency but also reduces material wastage, allowing industries to cut costs significantly while improving product quality.
Delving into the specifics of its operation, a typical roller former consists of multiple stations, each featuring a pair of rolls. These rolls are carefully crafted and aligned to perform incremental bending operations, gradually shaping the metal into its required profile. The techniqueness in roller forming lies in its step-by-step approach, distributing strain over numerous steps rather than imposing it all at once. This is pivotal in ensuring material properties are preserved, which is especially critical when working with specialized metals like stainless steel or high-strength alloys.
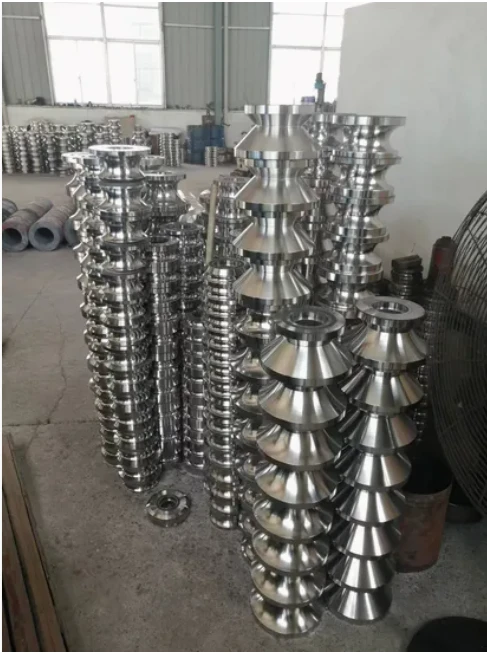
Beyond its mechanical prowess, the roller former represents a convergence of traditional craftsmanship and modern technology. Recent advancements have seen the integration of computer numerical control (CNC) systems, which provide unmatched accuracy and repeatability. With CNC, operators can program exact specifications for the material profile, and the roller former executes these with pinpoint precision. This digital edge not only enhances the capabilities of roller formers but also provides a competitive advantage.
For manufacturers, investing in a roller former signifies a commitment to quality, precision, and efficiency. However, selecting the right machine requires an understanding of several key factors, such as material type, desired profile geometry, and production volume. Consulting with engineers and technicians who possess specialized knowledge in roller forming can provide valuable insights and aid in making an informed decision that aligns with industry requirements.
roller former
In the realm of product development, the adaptability of roller formers is unrivaled. The ability to quickly adjust setups for different projects means manufacturers can swiftly pivot their production lines to accommodate new designs or modifications.
Additionally, with the emergence of Industry 4.0, integrating roller formers into smart factory systems bolsters this flexibility. Incorporating sensors and IoT technology, real-time data collection becomes possible, enabling predictive maintenance and minimizing machine downtime.
Authorities in the field of metal forming continually underscore the importance of regular maintenance and calibration to uphold the performance of roller formers. Ensuring that rolls are correctly aligned and maintained extends the lifespan of the machine, thereby enhancing its return on investment. Furthermore, training staff to handle the complex setups involved allows for smoother operations and minimizes errors.
Trust in the reliability of roller formers comes from decades of industry application, with countless success stories cementing their status as indispensable assets in manufacturing. These machines not only meet the stringent demands of modern production but often exceed expectations, proving essential for companies striving for excellence in their product offerings.
On a closing note, while the upfront investment in a roller former may seem substantial, the long-term benefits - manifested in productivity, consistency, and cost savings - are overwhelmingly positive. For any business aspiring to lead in its sector, staying at the forefront of technological advancements with robust, adaptable, and efficient machinery like the roller former is a step in the right direction.