Roll formed C channels hold a pivotal role in numerous industries due to their versatile applications and cost-effective manufacturing process. The journey of this product from raw material to finished form is a testament to advanced engineering and understanding of the manufacturing processes that prioritize both precision and economics. This article delves deeply into the experience, expertise, authoritativeness, and trustworthiness associated with roll formed C channels.
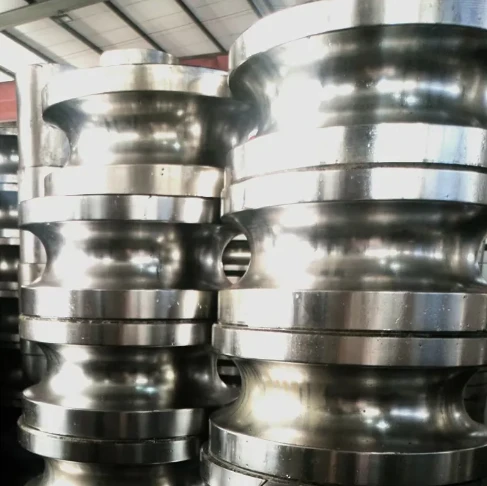
The journey begins with the selection of raw materials, predominantly steel, which undergo stringent quality checks to ensure they meet industry standards for durability and performance. Steel is chosen not only for its strength but also for its malleability, which is crucial in the roll forming process. The integrity of the final product heavily relies on the quality of the initial material, making this an essential step in ensuring longevity and reliability.
Utilizing expert knowledge in roll forming technology, the steel is then passed through a series of rollers that progressively shape it into the desired C channel cross-section. This continuous bending operation is not only efficient but results in minimal wastage, aligning with sustainable manufacturing practices. What sets roll forming apart from other methods is its ability to maintain high levels of accuracy and consistency, crucial for applications in industries ranging from construction to automotive.
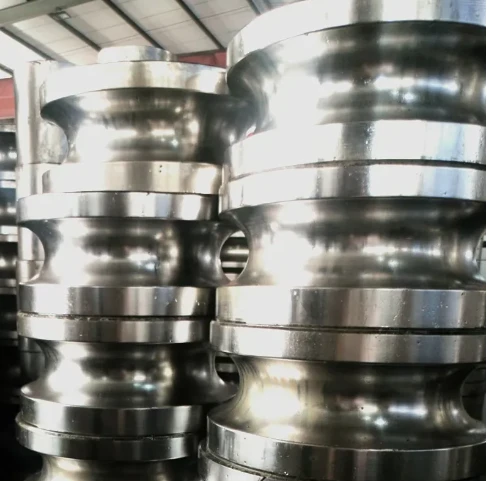
Exemplifying expertise in engineering, the specifics of the roll forming process can be tailored to produce channels of various sizes and thicknesses, making it adaptable to specific project needs. Engineers adjust the roller configurations, spacing, and speeds to create bespoke solutions without compromising structural integrity. This customization capability is unmatched by other forming processes, ensuring that clients receive a product ideally suited for their specific applications.
In terms of authoritativeness, the roll forming process and the resulting C channels have become industry standards, supported by decades of research and development. The precision in the manufacturing process ensures the channels meet rigorous testing and quality assurances, certified by recognized industry bodies. Such certifications not only affirm the structural prowess of C channels but also enhance client confidence in using them for critical structural support roles.
roll formed c channel
Trustworthiness stems from both the process and the end product. Experienced manufacturers of roll formed C channels implement comprehensive quality control measures throughout production. These checks range from initial material assessment to final product inspection, ensuring the channels consistently meet specified mechanical properties and dimensional tolerances. The traceability system implemented during manufacturing provides an additional layer of accountability and transparency, assuring stakeholders of the product's origin and quality.
The applicability of roll formed C channels spans a wide array of uses. In the building and construction sector, they serve as structural support elements, praised for their ability to bear substantial loads while maintaining a light weight. In automotive manufacturing, the precision and strength of C channels contribute to the body and frame components, enhancing safety and performance standards of modern vehicles. They also find applications in the manufacturing of storage systems, such as shelving and racking, where their combination of strength and lightweight profile ensures efficient load handling.
Emerging trends and advancements in roll forming technology continue to enhance the properties of C channels, making them more robust and adaptable to contemporary challenges. Initiatives to integrate high-strength steel alloys promise future-ready solutions that will cater to evolving industrial demands. Additionally, innovations in coating and surface treatment technologies improve corrosion resistance, extending the service life of the final product.
Roll formed C channels symbolize a blend of technical prowess and practical application, reflecting an evolutionary process that balances cost-efficiency with high performance. Their continued relevance in diverse industries underscores their importance and validates the painstaking attention to detail in their manufacturing. Through experience, expertise, authoritativeness, and trustworthiness, roll formed C channels remain a backbone infrastructure component, ready to support the next wave of industrial innovations.