Roll forming systems have revolutionized the way industries produce long-length metal components, favoring continuous bending operations to create profiles with a constant cross-section. These systems, indispensable in construction, automotive, and renewable energy sectors, are designed to tailor the manufacturing process with precision and efficiency.
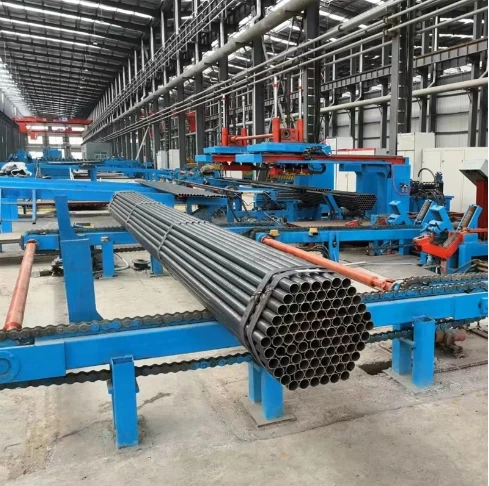
From an experiential standpoint, roll forming systems offer a seamless transformation of metal coils into your desired shape, marrying complexity with speed. Companies that embrace roll forming technologies often report increased productivity and reduced waste, enhancing the overall profitability and sustainability of their operations. As a testament to user experience, businesses can expect reduced lead times and consistent product quality, crucial for maintaining competitive advantage in today's fast-paced market.
The expertise involved in roll forming is both intricate and fascinating. These systems require a nuanced understanding of material behavior under stress, the mechanics of roll design, and the physics of metal conduction. Professionals operating roll forming machines acquire a unique skill set — they not only master the mechanics but also become adept at troubleshooting and customization. They ensure the synchronization across various stages of the process, including feeding, pre-cutting, post-cutting, and inline punching, affirming the intricacy and technical prowess required in roll forming systems.
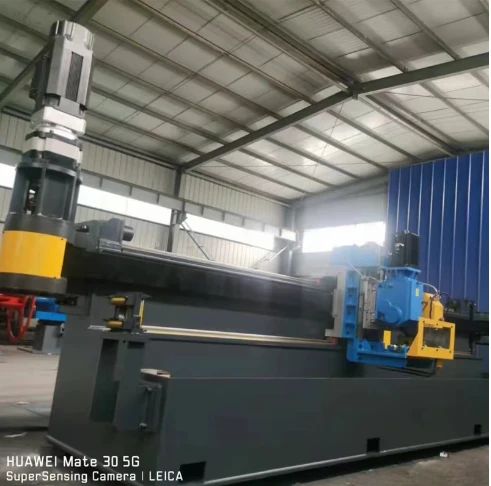
When speaking to the authoritativeness of roll forming systems, it is essential to highlight their impact on industrial standards and regulation adherence. Roll forming systems are engineered to comply with stringent quality control measures, ensuring that finished products meet national and international standards. This compliance reinforces their authority in sectors that demand precision and reliability, such as aerospace and defense, where quality cannot be compromised.
roll forming systems
Trustworthiness in roll forming systems is derived from both their technological robustness and the seasoned expertise of operators and engineers who manage them. Leading manufacturers provide comprehensive support, including machine setup, training, and maintenance services, to ensure seamless operations at client facilities. Their dedication to customer service builds long-term relationships, verifying the integrity and reliability of the roll forming systems they deliver.
Furthermore, customization plays a pivotal role in why roll forming systems are trusted by industries globally. These systems are adaptable to a vast array of specifications — from simple to intricate profiles, varying material thickness, and different metal types, including steel, aluminum, copper, and brass. Such versatility ensures that roll forming systems continue to adapt to the evolving demands of diverse industries, solidifying their place as a cornerstone technology in modern manufacturing.
In conclusion, roll forming systems stand as a pillar of efficiency and precision in manufacturing. Embodying rich experiential benefits and technical expertise, these systems drive operational excellence. Their authoritative compliance with industry standards and the trustworthy support from manufacturers embody the quintessential attributes that attract industries across the globe. Embracing roll forming systems means investing in a future of innovation, reliability, and unparalleled production capability.