When considering the cutting-edge technology embodied by HF (High Frequency) tube mills, it is crucial to delve into both their functionality and the advantages they offer in manufacturing robust and precise tubular products. HF tube mills represent a fusion of innovation and specialized engineering, tailored for industries ranging from construction to automotive.
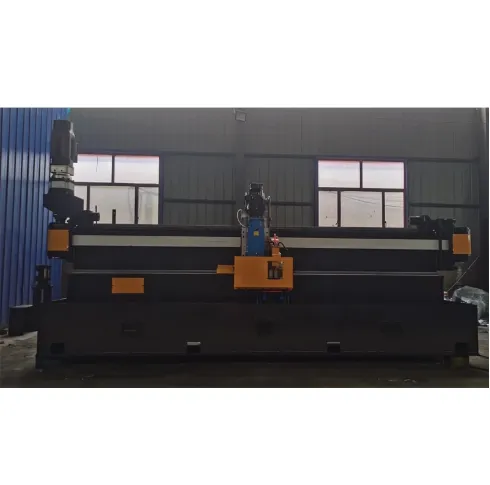
The heart of the HF tube mill's efficiency lies in its high-frequency electric current, which is used to weld the seam of the tube. This method is particularly advantageous for large-scale production owing to its speed and effectiveness, consistently producing welds with strength and uniformity. The high frequency allows the weld to be both swift and precise, minimizing any disturbances in the material structure that could compromise the integrity of the tube.
A key factor contributing to the professionalism seen in HF tube mills is their ability to produce tubes with varying thickness and diameter, adapting to unique industrial demands without compromising on quality. This adaptability is facilitated by sophisticated control systems which optimize parameters like welding speed, pressure, and current, ensuring each tube meets strict standards of quality and resilience.

Earning trust in industrial settings requires exhibiting consistent performance over time, and HF tube mills have earned a reputation as reliable workhorses. With minimal downtime and excellent throughput, these mills are engineered to support high-volume demands without compromising on product integrity. The seamless integration of automated processes not only boosts productivity but also reduces the margin of error, an essential feature for maintaining the highest levels of trust in results.
hf tube mill
High Frequency tube mills stand out with their sustainable approach to manufacturing. The precision in the welding process results in less material wastage compared to traditional methods, aligning with modern-day practices that prioritize sustainability. This efficiency extends through the lifespan of the product, where fewer raw materials translate into reduced environmental impact, garnering the trust of eco-conscious industries.
From an expert perspective, understanding the maintenance needs of HF tube mills can enhance operational longevity. Regular calibration of machinery and routine checks of the electrical components responsible for the high-frequency welding are essential to maintain peak performance. These practices not only ensure the machinery's durability but also protect the integrity of the tubes produced, reflecting a deep understanding of mechanical and industrial process integration.
Authoritative voices in the industry advocate for continual improvements in HF tube mill technologies, driven by feedback from engineers who have spent years perfecting these machines’ capabilities. When technological advancements, such as enhanced automation and real-time monitoring, are incorporated, they significantly elevate the operational efficacy of these mills.
In conclusion, the HF tube mill is a prime example of engineering excellence and manufacturing ingenuity. It merges high frequency technology with robust design principles, resulting in a manufacturing solution that is reliable, efficient, and eco-friendly. For industries seeking quality, speed, and sustainability, HF tube mills provide an authoritative answer, embodying expertise and trustworthiness in every tube rolled off its line. As industries evolve, these mills continue to adapt, setting standards and paving the way for future innovations in tube manufacturing.