Navigating the expansive realm of high frequency tube mills unveils a captivating blend of technology, precision, and craftsmanship. These advanced machines stand at the forefront of modern manufacturing, producing high-quality pipes and tubes that cater to diverse industries ranging from construction to automotive. The journey of understanding and optimizing the use of high frequency tube mills is punctuated by insights drawn from real-world experience, comprehensive expertise, and an unyielding commitment to quality.
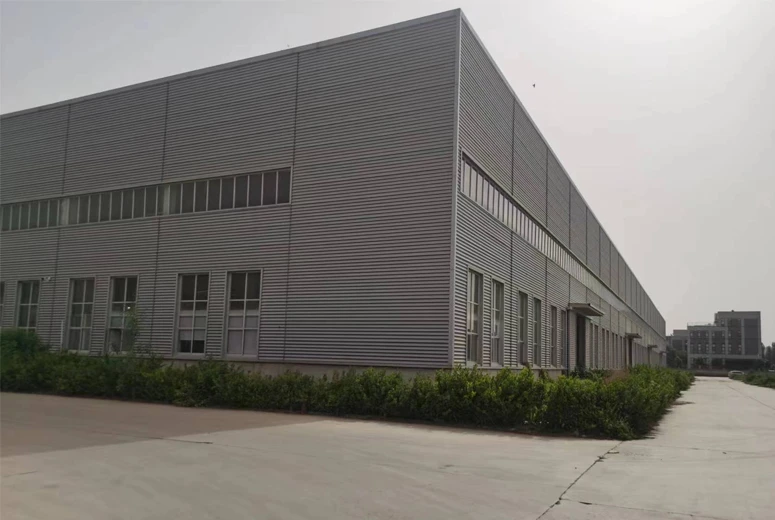
The evolution of tube mills is deeply rooted in the industry's quest for efficiency and precision.
High frequency tube mills specifically offer a significant leap in operational capacity. Unlike traditional methods, these mills employ high-frequency electrical currents to efficiently weld the seam of tubing, ensuring a robust and seamless end product. This process not only speeds up production but also guarantees the structural integrity essential for industrial applications.
Experts in the field frequently extol the virtues of high frequency welding due to its capacity to produce cleaner welds with minimal heat distortion. This precision is particularly beneficial when working with thinner materials or requiring high-strength welds. The process's adaptability makes it ideal for a wide range of materials, including carbon steel, stainless steel, and non-ferrous metals, underscoring its versatility.
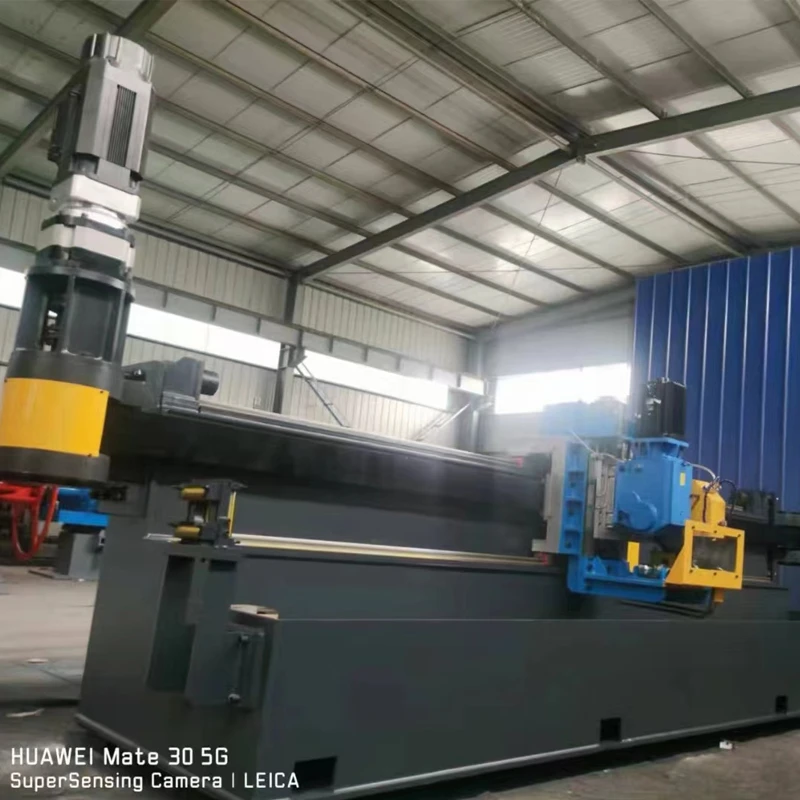
Authoritative reviews often highlight the technological advancements embedded within modern high frequency tube mills. Today’s models integrate sophisticated sensors and control systems that monitor and adjust welding parameters in real-time. These innovations significantly reduce the margin for error, ensuring consistent quality across large production runs. Additionally, the automation facilitates higher throughput rates, meeting the ever-growing demands of fast-paced industries without compromising quality.
Trustworthiness in the deployment of high frequency tube mills can be attributed to rigorous testing and adherence to international standards. Reputable manufacturers conduct exhaustive trials, simulating various operational scenarios to finetune their equipment. This meticulous approach not only fortifies the machine’s reliability but also instills confidence in end-users who rely on the equipment for critical applications.
high frequency tube mill
Real-world applications of high frequency tube mills manifest the tangible benefits that these machines offer. For instance, in the automotive industry, precision and strength are non-negotiable when producing exhaust or structural components. The seamless welds provided by high frequency mills greatly enhance the durability and performance of automotive tubes, directly translating to safer and more reliable vehicles.
The construction sector equally benefits, with high frequency tube mills supplying the backbone for robust scaffolding and framework materials. The precision welding capability ensures that even under significant stress, these structures maintain their integrity, thereby safeguarding workers and projects alike.
The conscientious selection and utilization of a high frequency tube mill require a deep understanding of its components and functionalities. Operators must be adept in machine configuration and maintenance—skills often honed through hands-on training and experience. The nuanced knowledge required to optimize settings for different materials and product specifications sets industry veterans apart, ensuring optimal machine performance and product quality.
The landscape of high frequency tube mills is one of perpetual innovation. Manufacturers continue to push the boundaries, integrating cutting-edge technology and design improvements. This constant evolution not only enhances performance and capability but also increases the accessibility of these technologies for a wider range of businesses.
Harnessing the potential of high frequency tube mills is a testament to human ingenuity in engineering and manufacturing. With their precision, reliability, and versatility, they continue to redefine possibilities across multiple sectors, embodying a fusion of expertise, technology, and trust that sets new benchmarks in industrial manufacturing.