The rolling shutter strip making machine stands as a remarkable innovation in the realm of manufacturing, designed to offer precision, efficiency, and reliability. This machinery has become an indispensable tool for industries requiring robust and secure solutions for doors and windows, where rolling shutters are pivotal.
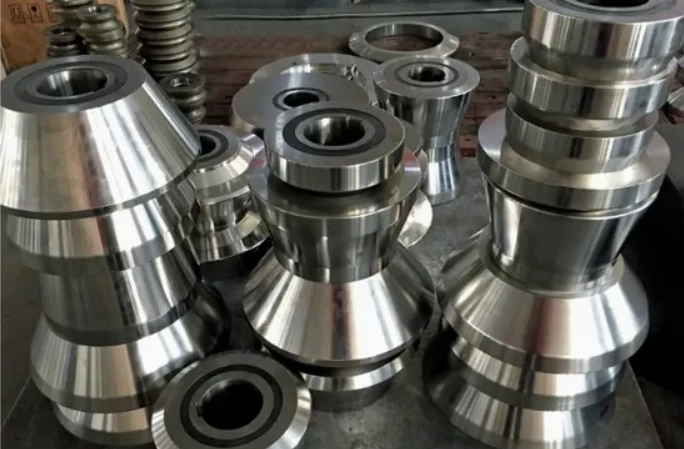
Understanding the rolling shutter strip making machine begins with grasping its functionality and the unique benefits it offers. This machinery is designed to transform sheet metal into rolling shutter strips through a series of processes, including decoiling, leveling, punching, roll forming, and cutting to length. Each of these stages is essential for ensuring the strength and durability of the final product.
One of the most compelling aspects of the rolling shutter strip making machine is its ability to produce high-quality outputs with remarkable consistency. Operators benefit from intuitive software that allows for precise control over each stage of production, ensuring that the end products not only meet but exceed industry standards. The machine’s automated nature reduces human error, an essential factor in maintaining quality across high-volume outputs.
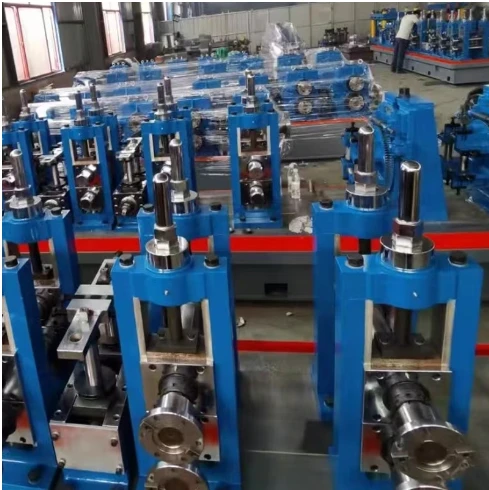
An industry expert would appreciate the proficiency of this machine in material handling and processing speed. Leveraging high-grade steel and equipped with a robust decoiler, the machine efficiently unwinds the metal sheet, minimizing any potential downtime. The leveling stage is meticulously configured to ensure the sheet is perfectly flat, which is crucial for subsequent processing accuracy.
Punching is intelligently integrated within the production line. The machine employs advanced hydraulic or servo technology to ensure precision and flexibility. This results in customizable hole patterns and hinge placements, a testament to its expertise in delivering tailored solutions without compromising on throughput.
Roll forming follows,
where the real transformation occurs. Here, the expertise of the rolling shutter strip making machine shines as it bends and shapes the metal into strips, maintaining strict adherence to the specified dimensions. This step highlights the machine’s ability to exert controlled pressure, manipulating metals of varying thicknesses with ease.
rolling shutter strip making machine
The final cutting to length stage employs high-speed shearing systems, accentuating the machine's authoritative command over precision. Operators can set specific lengths, aiding in the production of bespoke products that are ready for an array of applications.
In terms of energy efficiency, the rolling shutter strip making machine outperforms many competitors. Advanced motor technology reduces energy consumption, aligning with contemporary industrial goals for sustainability. The machine also boasts a modular design, enabling seamless integration into existing production lines, thus enhancing its authority in the manufacturing sector.
Trustworthiness is further established by the machine’s durability and low maintenance needs. Its construction involves high-quality components and a sturdy frame, ensuring a long operational lifespan. Manufacturers benefit from minimized breakdowns and reduced ongoing costs, reaffirming the machine’s role as a reliable asset in the production environment.
The safety features of the rolling shutter strip making machine cannot be overlooked. It includes automated shutdown protocols, emergency stops, and intuitive control panels that enhance operational safety. This aligns with industry standards, reinforcing the manufacturer’s reputation for producing trustworthy and employee-friendly equipment.
Lastly, when integrating a rolling shutter strip making machine into your manufacturing process, it is crucial to choose a supplier known for their expertise in installation and after-sales support. This not only ensures smooth initial operation but also offers peace of mind with accessible technical assistance and troubleshooting.
In conclusion, the rolling shutter strip making machine is a paragon of modern engineering, offering unmatched precision, efficiency, and reliability. Its ability to seamlessly integrate into production lines, coupled with expert design and trustworthy operation, makes it a premier choice for industries focused on delivering high-quality rolling shutter solutions. Embracing this technology not only enhances manufacturing capabilities but also aligns with broader business goals of sustainability and quality assurance.