Round pipe cutting represents a vital component in numerous industrial and manufacturing processes, requiring precision, expertise, and specialized equipment. Having transitioned from traditional methods to sophisticated technology-driven solutions, the field of round pipe cutting today marries expertise with innovation.
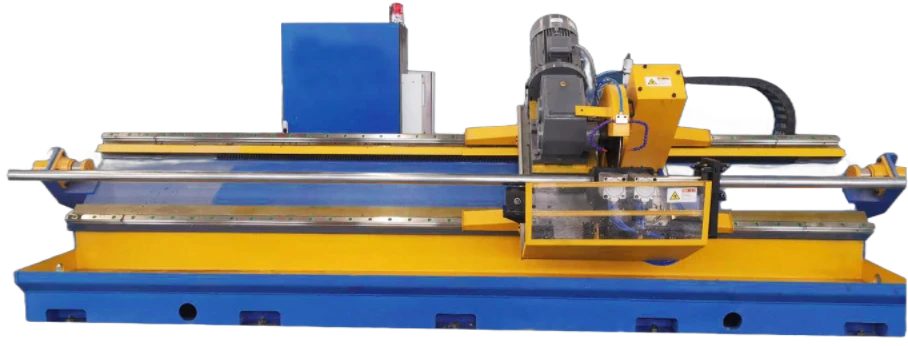
Professionals engaged in this specialty understand its significance in construction, automotive, aerospace, and more, mandating an understanding of materials from stainless steel to aluminum and beyond. The round pipe, often the backbone of structural designs and fluid systems, demands cutting solutions that ensure accuracy and efficiency. This article explores the cutting-edge techniques, pivotal equipment, and the importance of expertise in the round pipe cutting domain.
Understanding Round Pipe Cutting Techniques
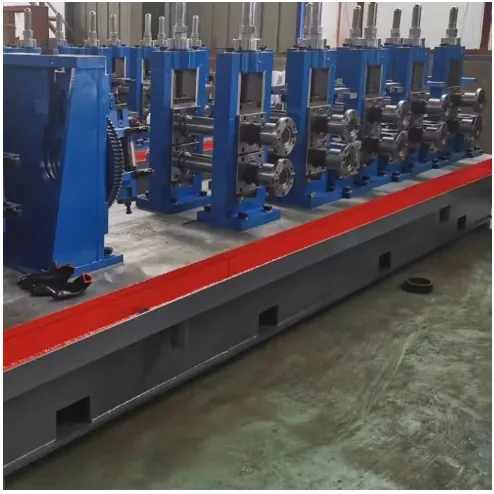
Various methods exist to cut round pipes, each with its unique attributes. Manual cutting, while traditional, is less common in high-precision industrial applications. Instead, methods such as laser cutting, water jet cutting, plasma cutting, and CNC machining take precedence.
Laser cutting offers unmatched precision and is lauded for its ability to produce clean edges, crucial in applications requiring tight tolerances. By utilizing concentrated laser beams, it effortlessly slices through metals with minimal thermal impact, reducing the risk of material deformation.
Water jet cutting, employing high-pressure water streams mixed with abrasive materials, is invaluable when thermal distortion must be avoided. This cold-cutting process is versatile, capable of handling various materials including fragile composites that might otherwise be compromised by heat.
Plasma cutting, though generating more heat, remains popular for its speed and efficiency, particularly for thicker metals. CNC machining, integrating computer-controlled precision, excels in complex designs and high-volume production runs, proving indispensable for metals and other materials.
Equipment and Innovation in Round Pipe Cutting
The selection of equipment for round pipe cutting significantly impacts efficiency and outcome quality. State-of-the-art machinery, equipped with advanced features like automation and integration with CAD software, simplifies complex cuts and enhances precision. Companies investing in these technologies often witness increased throughput, reduced waste, and more consistent results.
Advancements in cutting technology have also spurred the development of hybrid systems, combining the strengths of various cutting methods. These innovations enable operators to toggle between techniques, optimizing for speed, precision, or material constraints as needed.
Precision instruments, safety features, and user-friendly interfaces further distinguish the best equipment in the industry. Regular maintenance and updates are critical, ensuring these sophisticated machines operate at peak performance levels and align with evolving industry standards.
round pipe cutting
The Role of Expertise and Experience
In the realm of round pipe cutting, expertise and experience cannot be overstated. Professionals wielding these technologies must possess a deep understanding of both the machinery and the materials they work with.
Proper training and continuous education play key roles in cultivating this expertise.
Operators must consider specifics such as material thickness, diameter, and composition when selecting cutting methods, emphasizing the need for informed decision-making. This extends to understanding machine settings and conditions that could affect the quality and precision of cuts.
Moreover, experience fosters an intuitive approach, allowing professionals to troubleshoot and adapt to unique challenges efficiently. As round pipe cutting often forms a critical phase in larger manufacturing processes, expertise minimizes disruptions and maintains the integrity of the overall project.
Establishing Authority and Trust
Building authority in round pipe cutting involves not only mastering the physical techniques but also fostering relationships grounded in trust. Companies that demonstrate consistent quality, adhere to deadlines, and uphold safety standards naturally earn reputability.
Client trust is further reinforced through transparency in operations, such as offering insights into the processes and technologies utilized. Open communication regarding the capabilities and limitations of cutting methods encourages realistic expectations and partnerships rooted in mutual understanding.
Additionally, certifications and compliance with international standards reflect a commitment to quality and safety, further solidifying a company's authoritative standing in the industry. In an arena where precision can influence entire infrastructures, trust becomes an invaluable asset.
The Future of Round Pipe Cutting
Looking ahead, the future of round pipe cutting is intertwined with technological advancements and sustainable practices. Industry players are exploring automated solutions and AI-driven enhancements, which promise to further refine cutting precision and efficiency. Sustainability is also gaining traction, with initiatives aimed at reducing waste and energy consumption.
In this evolving landscape, embracing innovation while retaining foundational expertise is essential. Round pipe cutting will continue to be an integral part of industrial achievements, supported by professionals who unite experience with cutting-edge technology to drive forward excellence and innovation.