In the world of manufacturing, the term roll forming tube denotes a cutting-edge process that guarantees precision, efficiency, and reliability in tube production, transcending conventional manufacturing methods. This innovative approach not only aligns with modern industrial needs but also stands as a pinnacle of engineering excellence.
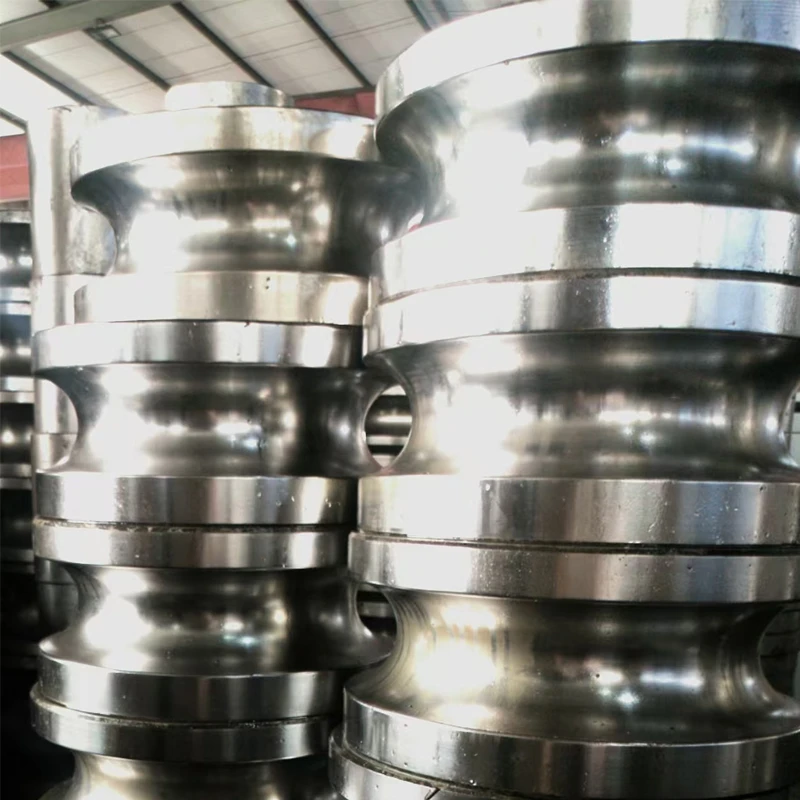
Roll forming tube production begins with a metal strip, often steel or aluminum, which is fed through a series of consecutively arranged rolls. These rolls progressively shape the metal into a continuous tubular form. One of the distinctive advantages of roll forming is its capacity to handle complex cross-sections with remarkable precision, a testament to its engineering prowess and reliability.
Professionals specializing in roll forming tubes carry a wealth of expertise. It's an art as much as it is science, requiring deft handling of machinery and profound material knowledge. The operators and engineers overseeing this process must possess an intimate understanding of metallurgy, the physics of deformation, and the mechanics of roll alignment and speed control. This expertise ensures that the final product is of the highest quality, suitable for various applications ranging from automotive parts to sophisticated construction frameworks.
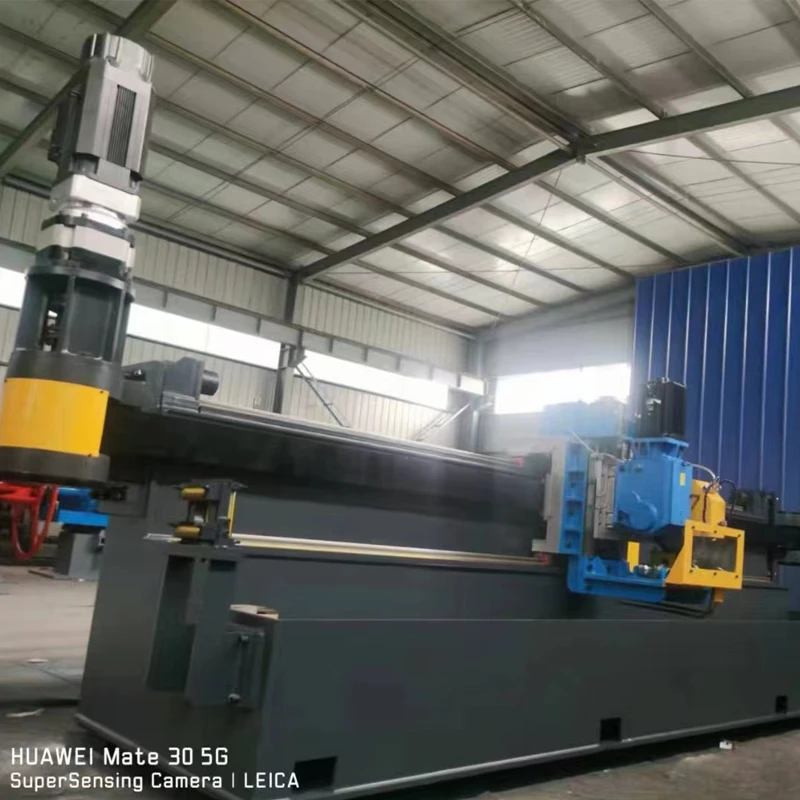
Furthermore, the authority of this process is underscored by its widespread adoption across industries globally. Leading manufacturers have turned to roll forming due to its scalability and versatility. Its use in producing lightweight yet durable components is particularly relevant in the automotive and aerospace industries, where efficiency and performance are paramount. Additionally, the power of roll forming extends to the production of green buildings and sustainable technologies, echoing an authoritative endorsement from eco-friendly industry leaders.
roll forming tube
Trustworthiness is intrinsically linked to the roll forming tube process because of its proven track record. Manufacturers rely heavily on its consistent output quality, which has been verified through rigorous testing and certifications over the years. Industry standards like ISO certifications further bolster the trust in roll-forming tube products, as they meet stringent quality and safety benchmarks. This trust is not confined to the end-users alone but is shared by stakeholders throughout the supply chain.
The experience of seasoned manufacturers speaks volumes about the roll forming tube's impact on product innovation and cost efficiency. Through years of experimentation and refinement, manufacturers have achieved optimal production speeds that reduce waste while maximizing material usage. The experience harnessed by these companies has enabled them to tailor the roll forming process to meet specific industry needs, thus creating bespoke solutions that are both innovative and economically viable.
Moreover,
the environmental benefits associated with roll forming cannot be overstated. This process significantly reduces scrap material, contributing to sustainable manufacturing practices. In a world increasingly focused on reducing carbon footprints, the efficiency of material usage in roll forming epitomizes the industry's commitment to sustainability.
In conclusion, the roll forming tube stands as a monument to modern manufacturing capabilities. The convergence of expertise, authoritative industry endorsement, trustworthiness, and rich experience makes roll forming a cornerstone of modern metalworking. Its application is a testament to human ingenuity and the relentless pursuit of innovation. As industries evolve and new challenges arise, roll forming tubes will undoubtedly continue to play a pivotal role, driving advancements and setting the standard for quality and reliability in manufacturing.