The sheet metal roll forming process stands as a cornerstone in the manufacturing of intricate metal components used across various industries. This technique, an assembly of both modern technology and age-old metallurgical principles, transforms flat sheets of metal into highly durable profiles. This process is indispensable for industries ranging from construction to automotive and electronics, delivering components with precision, consistency, and structural integrity.
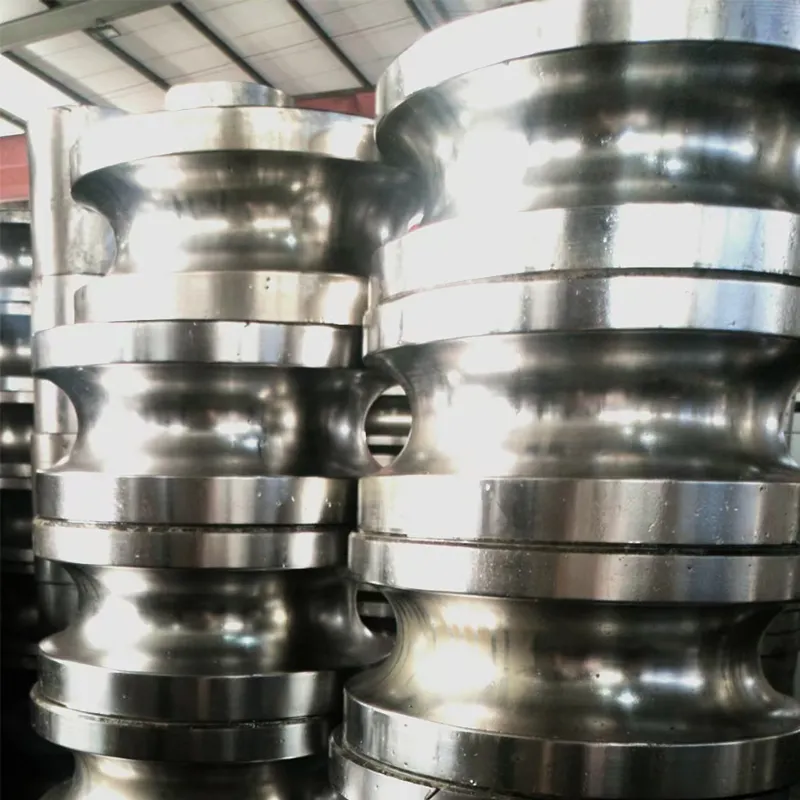
Understanding the intricacies of the roll forming process begins with the selection of the sheet metal, which is crucial for achieving the desired mechanical properties and surface finish. Engineers and technicians often opt for metals such as steel, aluminum, or copper, each chosen for their unique balance of strength, conductivity, and malleability. The initial design phase involves meticulous computer-aided design (CAD) schematics to ensure the final product meets the specific demands of its intended use.
Once the design phase concluded, the sheet metal undergoes a carefully controlled feeding process into the roll forming machinery. The machinery is comprised of a series of rolls, engineered to exact dimensions and angles, tools with unparalleled precision to shape the metal gradually as it progresses through each roll station. The number of roll stations depends on the complexity of the desired profile; more intricate designs require additional stages to minimize stress and prevent distortion.
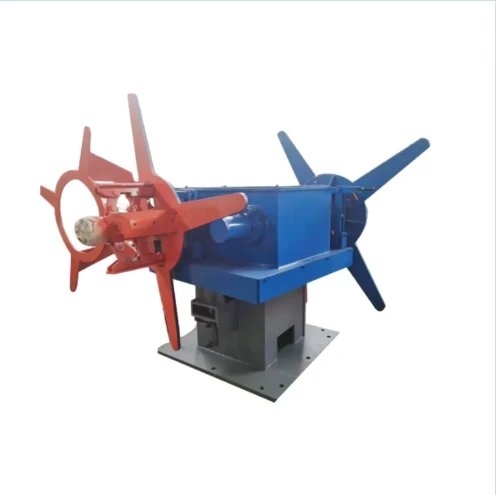
An integral part of ensuring the integrity of the roll forming process is maintaining tight tolerances throughout the production. A minor deviation in any roll station can compromise the final product's dimensions and compromise its functionality. This is where cutting-edge measurement technologies play a critical role. Laser and digital measurement systems are employed to provide real-time feedback and ensure each piece remains within precise tolerances, increasing consistency and reducing waste.
Quality assurance does not end with precision measurement. Material testing at various production stages ensures that the material properties remain uncompromised. This stage involves both destructive and non-destructive testing methods—ranging from tensile and impact tests to magnetic particle inspections—to verify that each batch meets strict industry standards. Such rigorous testing frameworks are essential in industries where structural failure is not an option, such as in aerospace or medical equipment manufacturing.
sheet metal roll forming process
One of the transformative elements of the roll forming process is its high scalability and efficiency, factors of immense value in large-scale industrial production. Unlike traditional press-forming methods, roll forming minimizes material wastage, leveraging nearly 100% of the metal while requiring less energy, thus cutting down costs. Moreover, once set up, roll forming lines can run continuously, producing long lengths of formed sections, ready for cutting to size as per customer specifications.
Advancements in automation and robotics have further augmented the capabilities of roll forming. Computer-controlled machinery not only ensures unmatched precision but also speeds up production rates while reducing labor costs. Automation systems are programmed to handle everything from the feeding of raw materials to stacking the finished products, allowing operators to focus on monitoring systems and quality checks rather than hands-on operating tasks.
The role of experienced engineers and technicians cannot be overstated in this process. Their mastery over machine operations and material science is crucial. Keeping abreast with cutting-edge research and technological progressions allows them to foresee and mitigate potential manufacturing challenges, maintain efficiency, and guarantee the highest standards of product quality and safety.
The sheet metal roll forming process is more than a manufacturing technique; it's a technological symphony where mechanics, electronics, and metallurgy coalesce. It represents not just the conversion of raw material into a usable form, but the pinnacle of precision engineering. By balancing innovation with rigorous quality control and materials expertise, roll forming plays a vital role in shaping the future of advanced engineering products, solidifying its place as an authoritative and trusted method in metal fabrication.