For businesses that depend on precision in metalworking and manufacturing, the integration of a small tube cutting machine into your operations can be transformative. These machines are not just a luxury but a necessity for modern manufacturing lines that emphasize precision, efficiency, and versatility. Understanding the benefits and nuances of these machines can enhance your production line’s output while ensuring quality and reliability.
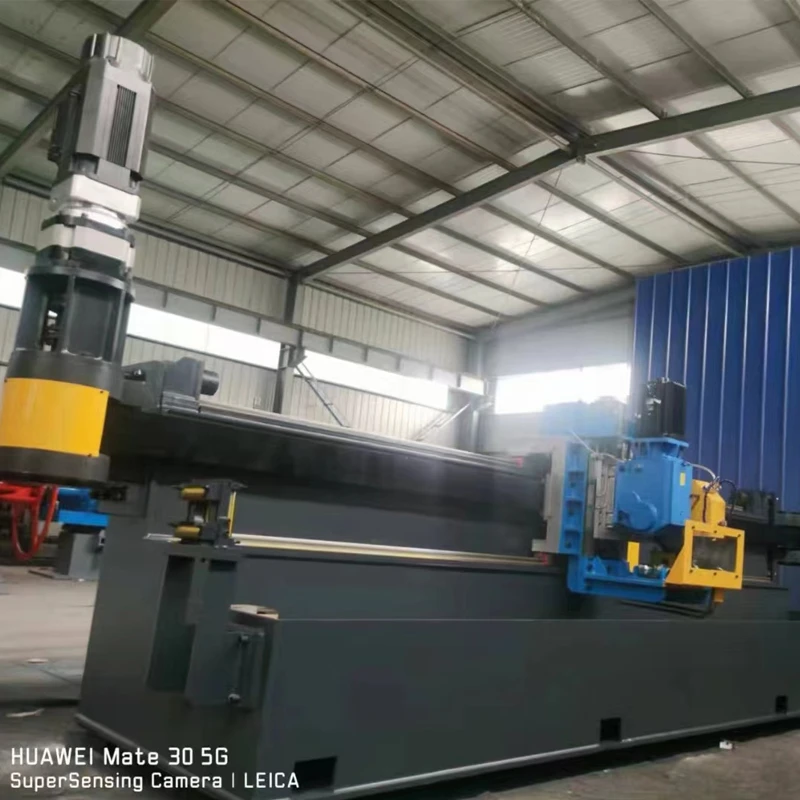
Small tube cutting machines have evolved tremendously, becoming compact yet powerful tools that address the intricate needs of diverse industries. From automotive to aerospace, and even medical fields,
the applications of these machines are vast. They are engineered to cut tubes of various materials—stainless steel, aluminum, copper, and plastics—with remarkable precision, thus ensuring that each component meets exact specifications.
The expertise required for operating a small tube cutting machine lies in understanding the nuances of tube diameters and wall thicknesses. These machines are equipped with advanced technology, including CNC (Computer Numerical Control) systems, which allow for the automation of cutting processes. This contributes significantly to reducing operator error, thereby enhancing productivity. Skilled operators can program these machines to produce repetitive, accurate cuts consistently, eliminating the discrepancies that are common with manual cutting methods.
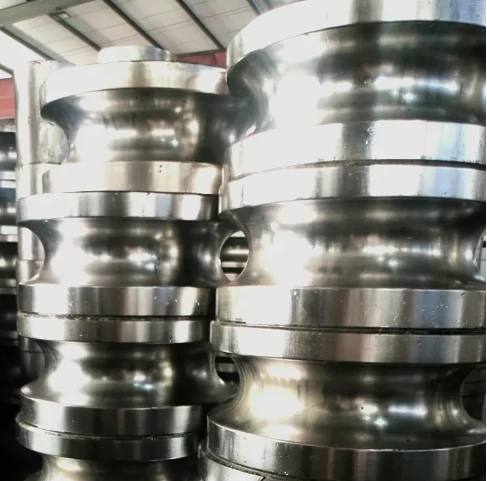
Establishing the authoritativeness of a small tube cutting machine involves recognizing the manufacturers who are pioneering advancements in this field. Companies like Bystronic, Mazak, and TRUMPF are instrumental in the development of cutting-edge machines that integrate laser technology, which not only cuts with precision but also increases the speed of the production process. These manufacturers have decades of experience and are known for their rigorous quality standards, making them the benchmark in the industry.
Moreover, investing in a small tube cutting machine from a reputable manufacturer also ensures trustworthiness in terms of after-sales service and support. Understanding that breakdowns or inefficiencies can cause costly production delays, leading manufacturers offer robust support services. This includes routine maintenance, availability of spare parts, and expert customer service teams ready to troubleshoot any issues. Reliable warranties also provide added assurance, covering any unforeseen failures or defects in the machine.
small tube cutting machine
From a real-world perspective, businesses implementing these machines have witnessed substantial improvements in their operations. For instance, a mid-sized manufacturing firm reported a 30% reduction in material wastage and a significant increase in their output rate after adopting advanced small tube cutting technologies. This efficiency results from the precision of cuts, which minimizes rework and resource waste. Moreover, the ability to handle complex cuts and patterns allows companies to diversify their product offerings, tapping into new markets without the need for additional capital investments in separate cutting equipment.
In terms of specialization, small tube cutting machines offer unparalleled versatility. They can adapt to various cutting operations such as straight cuts, beveled edges, and intricate patterns, accommodating a range of project needs. Their capability to switch between different tube sizes and materials swiftly, without extensive downtime, enhances their appeal to manufacturers looking to maintain flexibility in production schedules.
Finally, adopting a small tube cutting machine aligns with sustainable manufacturing practices. With precision cutting, material waste is significantly reduced, promoting environmental consciousness and aligning with global sustainability standards. The integration of energy-efficient technologies in modern machines further supports efforts to reduce the carbon footprint of manufacturing operations.
In conclusion, small tube cutting machines are not merely tools but integral components of a modern, efficient production line. Their ability to transform materials into precise parts with minimal waste positions them as essential equipment for any operation. Businesses looking to maintain their competitive edge should consider these machines not just as an investment in equipment, but as a commitment to quality, efficiency, and sustainable growth.