The stainless steel pipe manufacturing industry has seen remarkable advancement due to technological innovations within industrial machinery. As global demand for durable and corrosion-resistant piping solutions continues to rise, investing in a high-quality stainless steel pipe manufacturing machine is crucial for companies seeking efficiency and excellence.
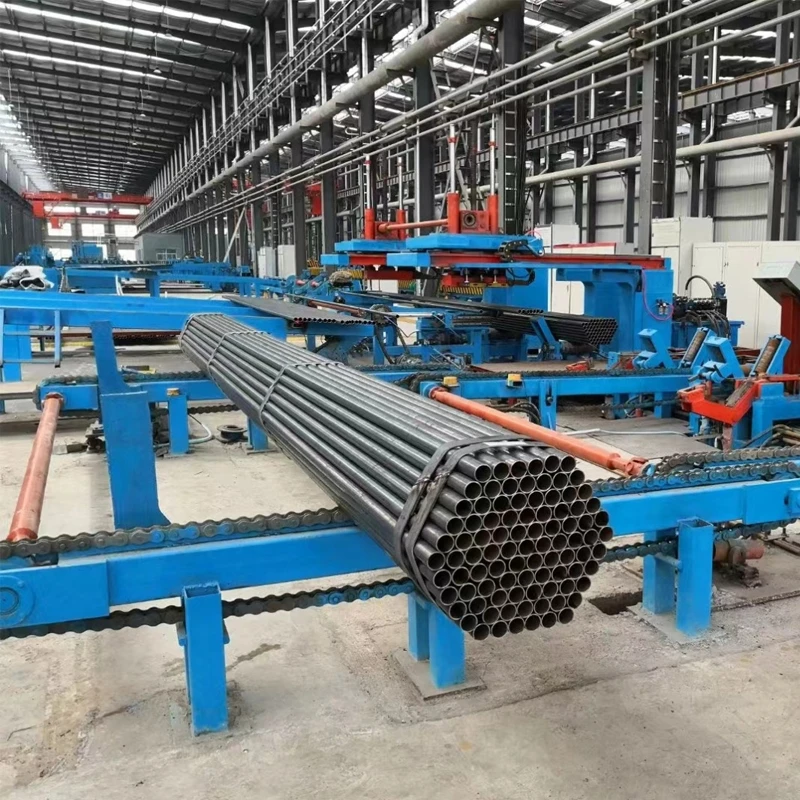
Understanding stainless steel pipe manufacturing begins with grasping the fundamentals of the machines employed in production. These machines are engineered to withstand intense operational demands, delivering precision, consistency, and reliability. Their core components typically include forming sections, welding systems, cutting units, and sophisticated control panels, each designed to integrate seamlessly for smooth, continuous processing.
The forming section of a stainless steel pipe manufacturing machine is where the initial transformation occurs. Raw stainless steel sheets or strips are expertly manipulated into the desired round or rectangular shape. This process demands a machine that excels in precision engineering, ensuring the sheets retain their structural integrity throughout the bending actions. Machines that offer advanced roll forming capabilities stand out in this area, providing consistency across batches.
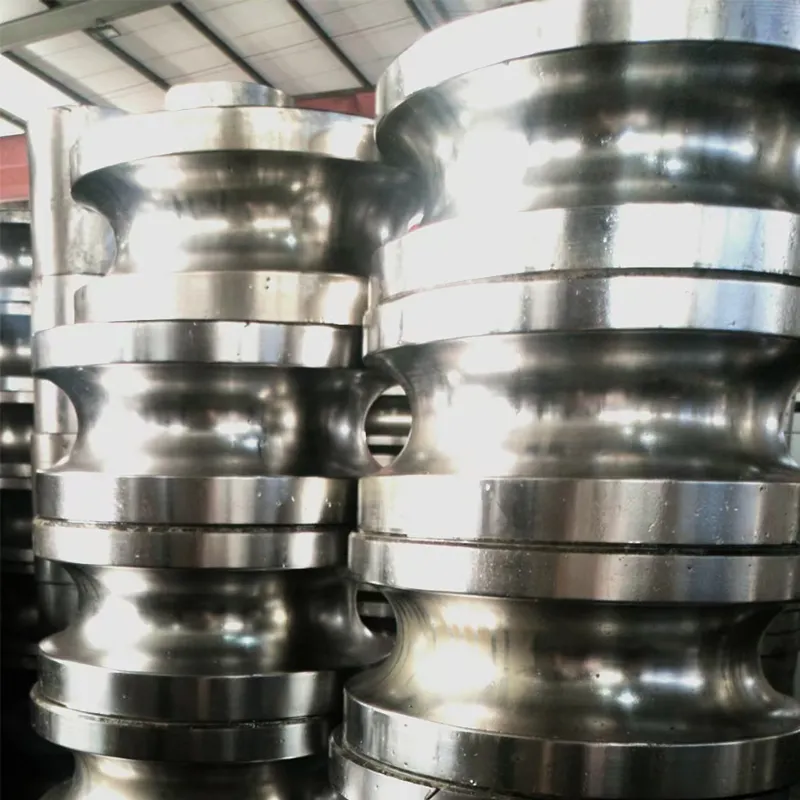
Welding is a pivotal phase in the production of stainless steel pipes. Modern manufacturing machines may use different welding techniques, such as Tungsten Inert Gas (TIG) or plasma welding, each suiting specific requirements based on pipe diameter and expected application. High-frequency induction welding is increasingly popular for its efficiency and ability to maintain seamless joints — an essential criterion in ensuring the pipes' strength and reliability under stress.
Accuracy doesn't stop at forming and welding; cutting mechanisms are integral to the quality of the final product. Sophisticated machines employ laser cutting technology, which offers unparalleled precision and clean cuts that require minimal finishing. This capability is crucial for manufacturers catering to industries where millimeter-perfect dimensions are vital.
stainless steel pipe manufacturing machine
The brain of the operation is undoubtedly the control panel. A state-of-the-art stainless steel pipe manufacturing machine integrates advanced software solutions that allow operators to customize operations with ease. These systems facilitate real-time monitoring and provide analytics that support timely adjustments and maintenance scheduling, thus maximizing machine uptime and productivity.
Investing in a dependable stainless steel pipe manufacturing machine also involves evaluating the expertise and customer support provided by manufacturers. Leaders in the industry not only offer top-of-the-line machinery but also demonstrate a deep understanding of metallurgy, mechanical design, and industrial applications. Companies renowned for their technical support establish trust by offering comprehensive training programs and after-sales service, allowing organizations to focus on what they do best — producing top-quality pipes.
Sustainability is another dimension gaining traction in the pipe manufacturing sector. As environmental regulations tighten globally, machines that incorporate eco-friendly technologies, such as energy-efficient motors and recyclable material use, are becoming more attractive. These features not only reduce the carbon footprint but also enhance the cost-effectiveness of the manufacturing process by minimizing waste and conserving resources.
The testimony of industry players further amplifies the credibility of specific machines. Case studies and real-world testimonials from established enterprises leveraging these machines underscore their value. These insights reveal tangible benefits such as reduced production times, enhanced product quality, and significant operational savings.
To conclude, selecting the right stainless steel pipe manufacturing machine transcends beyond making a purchase. It is about forming a partnership with technology that heralds growth, innovation, and sustainability. Companies must prioritize machinery that embodies superior engineering, is backed by substantial technical expertise, and is from trusted, authoritative providers. As the industry evolves, staying ahead of the curve involves making informed, strategic decisions that align with both current needs and future aspirations. Such investment empowers businesses to meet market demands competently, thereby solidifying their competitive edge.