In the rapidly evolving world of manufacturing, especially when it comes to steel pipe production, the cost of machinery is frequently a topic of importance. The price of a steel pipe making machine can vary widely depending on several crucial factors, making it a significant point of consideration for manufacturers aiming to optimize production and efficiency.
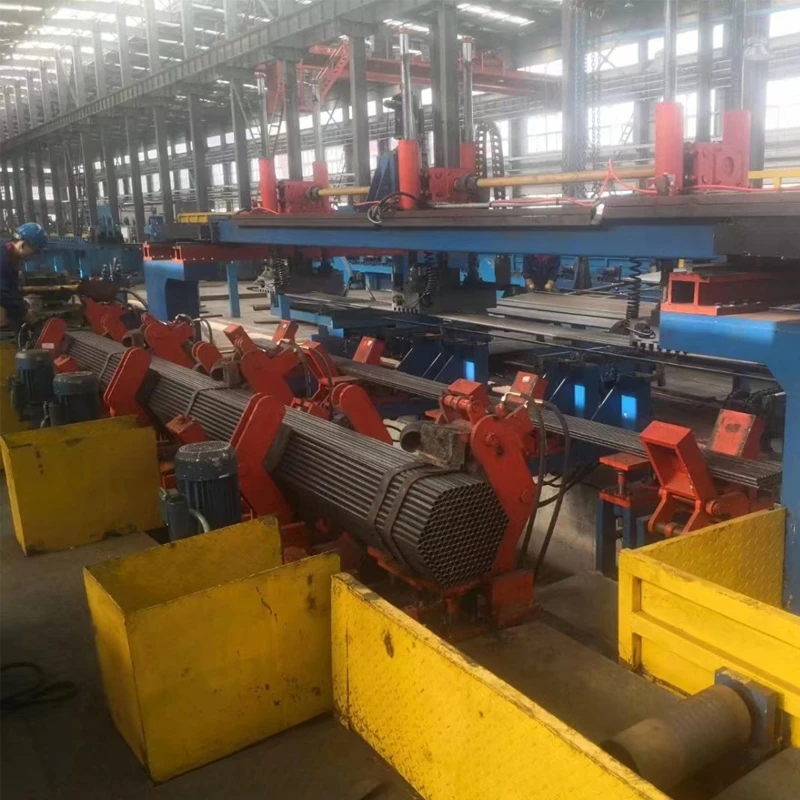
Steel pipe manufacturing machines are intricate devices engineered for precision, durability, and high output. To comprehend the true cost, one must delve into the intricacies that determine these prices. Expertise in this field dictates that we first understand the different components and capabilities these machines offer.
A primary determinant of price is the machine’s production capacity. High-capacity machines capable of producing larger pipes or higher volumes inevitably require advanced engineering, stronger materials, and more sophisticated technology, thus driving up the price. For example, a machine built for small-scale operations can cost anywhere from $10,000 to $50,000, whereas industrial machines focusing on large-scale production may range from $100,000 to several million dollars.
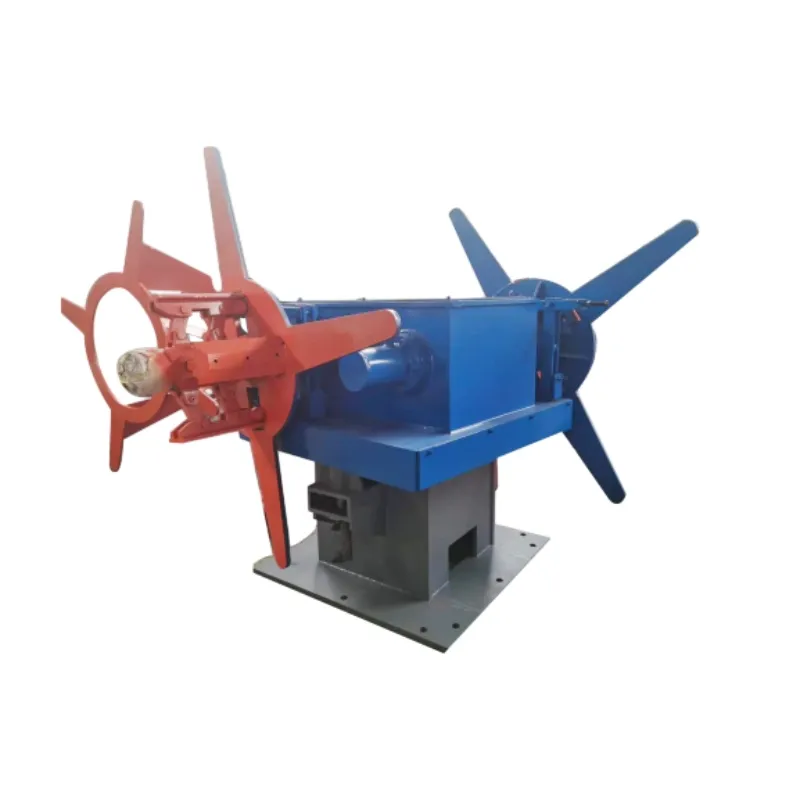
Technology integration is another critical factor influencing price. Modern steel pipe making machines often incorporate sophisticated technology such as PLC (Programmable Logic Controllers), SCADA (Supervisory Control and Data Acquisition) systems, and even AI components for enhancing operational efficiency and reducing human error. While these features increase the upfront investment, they invariably boost production efficiency and product quality, which can result in long-term savings and increased profitability.
Material quality and machine lifespan are also significant cost determinants. Machines constructed with high-grade steel and components that resist wear and tear naturally have a higher initial price but offer better longevity and lower maintenance costs. Expert operators often prefer investing in robust machinery to minimize downtime and maximize output.
Installation and after-sales service are sometimes overlooked but are integral to the overall machine price. Some manufacturers include comprehensive installation services, training for personnel, and extended warranties within their pricing strategy. Trustworthiness in this context means engaging with reputable manufacturers known for their transparent pricing and reliable customer service.
steel pipe making machine price
Geographical location and market demand also influence pricing. For instance, manufacturers in regions with access to cheaper raw materials or those situated near key shipping lines may offer competitive pricing. Conversely, a region experiencing high demand for steel infrastructure projects might see prices surge due to increased local demand for steel pipe manufacturing capabilities.
Customization options allow manufacturers to tailor machines to specific production requirements, which can impact cost. Custom machines designed for unique applications can demand premium pricing; however, they offer unmatched efficiency for niche markets.
Assessing the return on investment (ROI) is a critical step in deciding the best machine for your operation. An authoritative understanding of your production goals, market dynamics, and machine capabilities is essential for making an informed purchase. Manufacturers should consider both short-term costs and long-term advantages, such as increased production speed, reduced labor costs, and improved product consistency.
Finally, strategic financial planning and comparative analysis play a vital role. Investing in a costlier, more advanced machine might seem daunting initially but often results in superior efficiency and product quality. Researching and comparing multiple manufacturers, requesting detailed quotations, and seeking machine demonstrations are steps grounded in expertise that can clarify the true value of these machines.
In conclusion, while the upfront price of a steel pipe making machine is a significant consideration, it is paramount to weigh this against factors such as production capacity, technology integration, materials and build quality, post-sale service, and customization options. By exploring these elements with a focus on experience, expertise, authoritativeness, and trustworthiness, manufacturers can make informed decisions to boost productivity, ensure quality production, and ultimately drive profitability.