Exploring the intricacies of investing in a tube making machine is essential for any company looking to streamline production processes and maintain a competitive edge. Tube making machines are versatile, catering to different industries like automotive, construction, and plumbing. However, one key consideration for anyone in the market for a tube making machine is the price, which can fluctuate widely based on several factors.
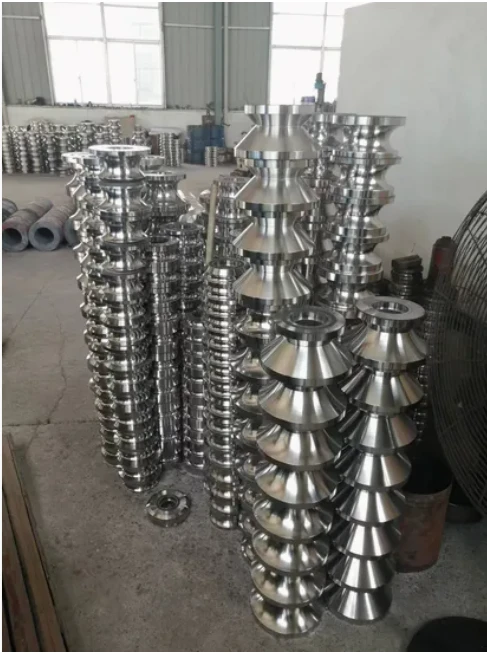
Different models cater to various production needs, such as speed, size, and thickness of the tubes. A basic manual tube making machine might suffice for small-scale operations, with prices starting around $5,000. In contrast, an automated tube making machine fitted with advanced technology and capable of high-volume production can range from $50,000 to more than $150,000.
The degree of automation contributes significantly to the pricing. Semi-automated tube making machines, while less expensive than fully automated ones, offer increased output and consistency, often priced between $20,000 and $60,000. These machines require some manual intervention but allow for greater control over production variables like dimensions and material types. Fully automated machines, although on the higher end of the price scale, minimize human error and maximize efficiency, a feature that is vital for large-scale manufacturing.
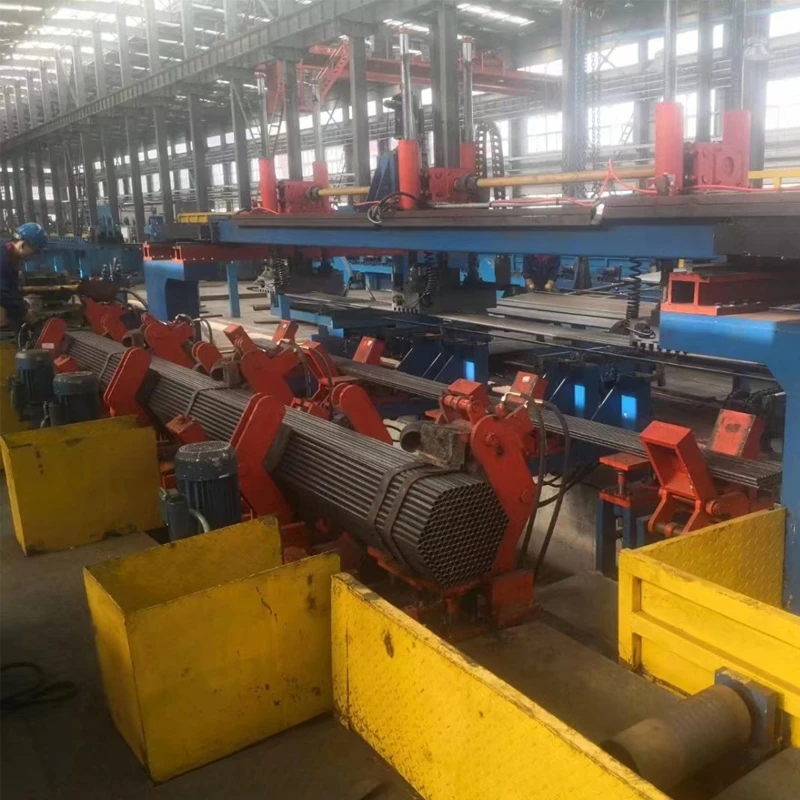
Material compatibility is another critical feature influencing price. Tubes manufactured from stainless steel, copper, or aluminum entail specific machine requirements to handle differing hardness levels and melting points. Machines specialized for particular materials often feature advanced, durable components, justified by higher price points. For instance, machines equipped to handle high-hardness materials like stainless steel are priced higher due to the robustness of components necessary to avoid wear and tear.
Energy consumption and efficiency should not be overlooked when considering the total cost of ownership. Machines that operate efficiently may have a higher initial purchase price but typically offer savings over time through reduced energy costs. Sustainable operations become increasingly relevant for companies aiming to reduce their carbon footprint, thus driving demand for energy-efficient models.
tube making machine price
Customization capabilities impact the pricing structure as well. Manufacturers often offer add-ons or custom-built features like precision cutting, bending, threading, or engraving. While these increase the initial investment, they enhance machine versatility, catering to diverse client needs across sectors and potentially increasing profitability.
Brand reputation plays a pivotal role in pricing. Established manufacturers with a track record of durability and customer support may set higher price points. Their products often come with comprehensive warranties and readily available spare parts, which add long-term value. Conversely, lesser-known brands may offer lower prices, but the accompanying risk might include unreliable support and challenges in sourcing maintenance parts.
In conclusion,
selecting a tube making machine entails more than just evaluating the immediate sticker price. Factors like automation level, material compatibility, energy efficiency, customization potential, and manufacturer reputation must align with business objectives and budget considerations. Engaging with industry experts and validating their credentials ensures an informed purchase decision, bolstering not just the production capability but also the trust in the investment made.
Consideration of these multifaceted elements reinforces the importance of due diligence. Aligning machine specifications with specific production requirements guarantees that the chosen tube making machine will offer the best return on investment over its operational life, enhancing the overall manufacturing effectiveness and reinforcing the business's competitive position in the industry.