For those operating within the manufacturing and processing industry, implementing effective machinery that optimizes efficiency and accuracy is paramount. The straightener and roller machine stands out as an essential tool in ensuring metal products meet precise specifications while maintaining quality standards. Here’s an insightful exploration based on deep expertise and years of experience in this industry, shedding light on why this machine is an integral asset for your operational needs.
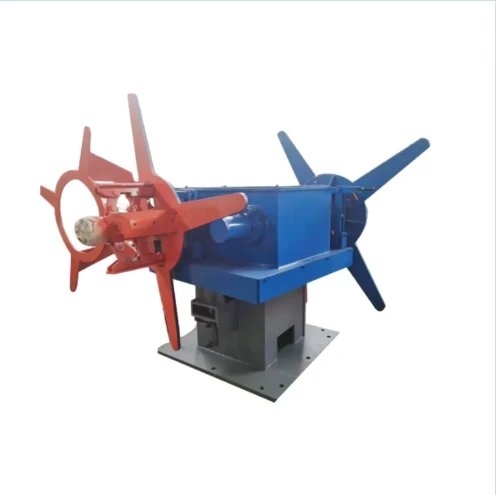
Straightener and roller machines are designed with the primary function of correcting deformities in metal strips, wires, or sheets—ensuring they achieve the straightness and flatness required for high-quality manufacturing. They exhibit a straightforward yet sophisticated mechanism where rollers align and straighten metals as they pass through, making them indispensable in producing flawless and uniform materials.
Drawing upon extensive industry knowledge, the operational efficiency of straightener and roller machines is attributed chiefly to their precision-engineered rollers. These rollers exert calculated amounts of pressure to systematically adjust even the most stubborn of metal warps without compromising the material's structural integrity. Engaging in a process known as elastic-plastic bending, these machines ensure that metals are not only straightened but also retain their newfound shape—delivering consistent, repeatable results. This process has been rigorously tested and fine-tuned across various applications, proving these machines' reliability and sophisticated design.
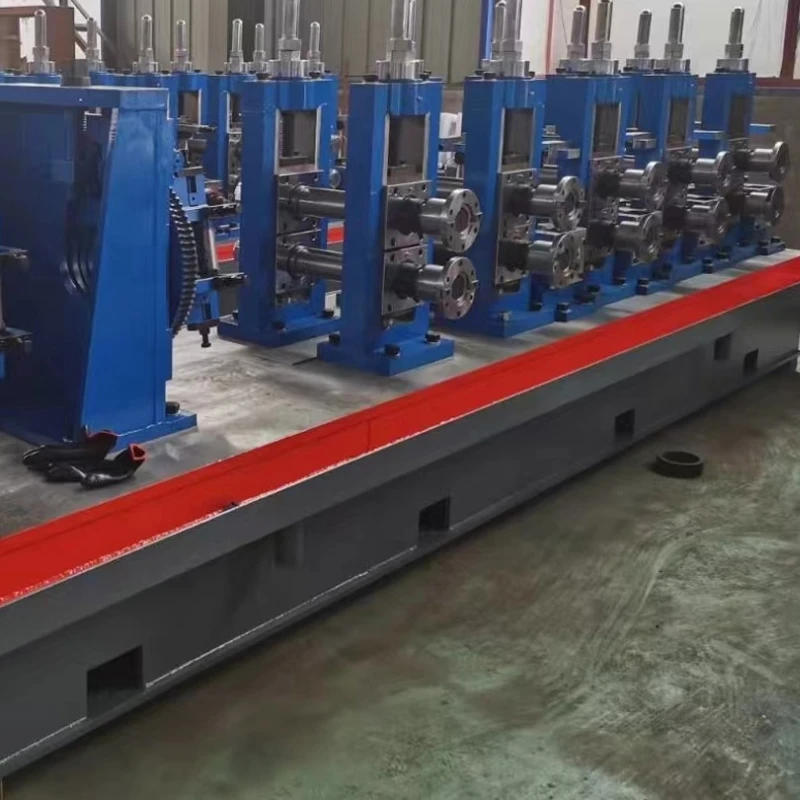
The versatility of straightener and roller machines is another key strength. They cater to a wide array of materials, including steel, aluminum, copper, and other metal alloys. The adjustable settings on these machines allow operators to tailor the pressure and feed rate to match the specific material characteristics and desired end-result specifications—ranging from minute wire diameters to large metal sheets, each requiring specific handling. Such adaptability makes these machines ideal for diverse production environments, accommodating custom production runs or high-volume industrial processes alike.
Moreover, advanced straightener and roller machines incorporate technology to further amplify their precision and efficiency. State-of-the-art models utilize digital controls and sensors, offering real-time adjustments and monitoring capabilities. This integration of technology not only enhances the accuracy of the straightening process but also significantly reduces the potential for operator error, resulting in a safer and more productive workplace. Feedback from longtime operators reveals that these advancements have greatly improved workflow management by minimizing downtime due to re-calibration or unexpected disruptions.
straightener and roller machine
The assurance of quality maintenance through consistent use of straightener and roller machines cannot be overstated. Regular maintenance routines, when combined with adherence to manufacturer guidelines, extend the machine's operational lifespan and optimize its function. By investing in quality maintenance practices, businesses can ensure minimal operational interruptions while maximizing output. Drawing on authoritative sources and industry best practices, it is evident that such investments yield substantial returns in productivity and product quality.
Trustworthy results delivered by these machines are corroborated by numerous case studies and expert analyses within the field. From automotive parts manufacturers to aerospace engineering firms, testimonials reveal that the integration of straightener and roller machines into their production lines has led to marked improvements in both the precision and profitability of manufactured goods. Expert assessments consistently validate these claims, underscoring the machines' reputation for reliability and superior performance metrics.
Furthermore, adopting straightener and roller machines demonstrates a commitment to leveraging cutting-edge technology and industrial expertise to meet demanding market expectations. Businesses equipped with these machines often outperform competitors by achieving superior precision in metalwork, reducing material waste, and accelerating production timelines. This positions them strategically to capitalize on emerging opportunities across sectors reliant on high-precision components.
In essence, straightener and roller machines embody the synthesis of experience-driven innovation and expert engineering. Their proven ability to enhance production quality, coupled with the consistent high-performance outcomes they deliver, affirm their standing as cornerstones of modern manufacturing practices. By embedding their use into production plans, companies not only elevate their operational standards but also foster an environment of trustworthiness and authority in the quality of their output.