In the world of manufacturing and construction, the quality and precision of materials can make or break a project. One of the most critical components in this domain is wire, specifically wire that has been straightened and cut to precise specifications. These processes ensure that wires meet stringent standards necessary for various applications, ranging from basic construction to sophisticated electronic assemblies.
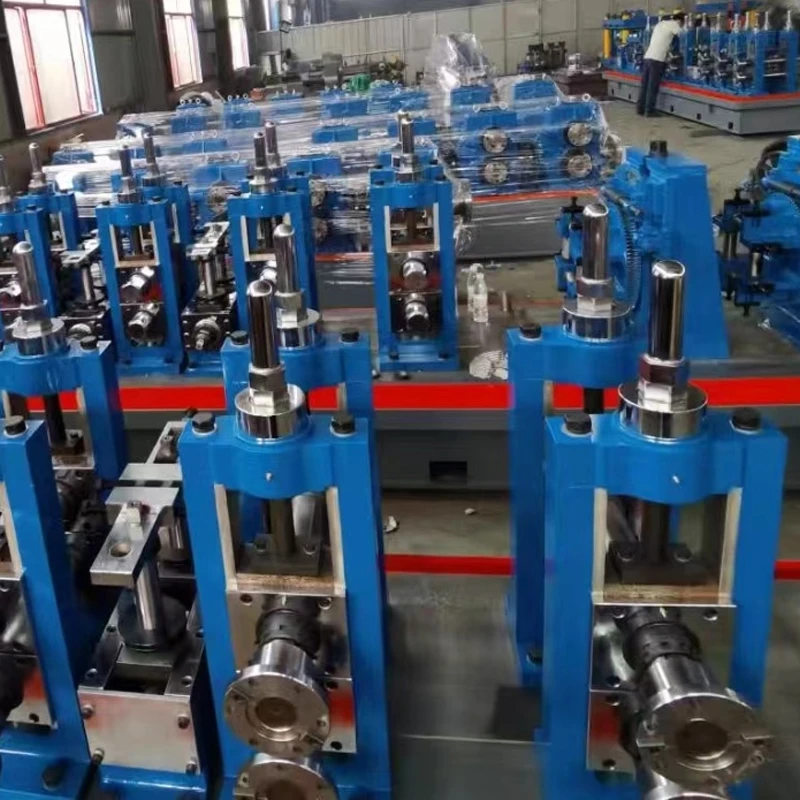
At the heart of any successful wire product is the expertise applied in its manufacturing process. Precision in straightening and cutting wire is not merely a benefit but an absolute necessity. It ensures that the wire functions correctly without deviations that could potentially affect the performance or safety of the product in which it is used.
Straightening wire is the first essential step. Wire that comes straight from a coil is subjected to tension and force, often distorting its shape. This is where the straightening process shows its importance—by employing advanced machinery, often controlled by computer systems to ensure maximum accuracy. The use of high-precision rollers and tension control systems allows for the correction of these distortions, resulting in wire that is perfectly straightened according to the required standards. Skilled operators, along with automated systems, monitor the process to maintain consistent results, reflecting the sophisticated expertise needed in modern manufacturing environments.
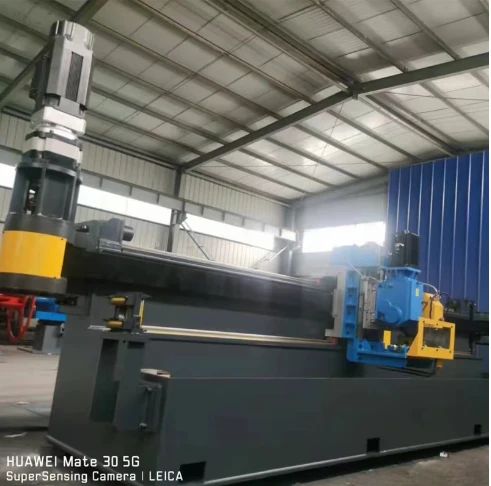
The cutting process follows, where precision is again critical. Whether the wire needs to be in lengths measured to millimeters or meters, cutting must be exact to avoid waste and to fit precise design specifications. The use of CNC machines and laser cutting technologies highlights the innovative approach taken by experts in the industry, ensuring clean, accurate cuts every time. Such technologies offer flexibility, speed, and accuracy, accommodating a wide range of wire materials—be it stainless steel, copper, or aluminum. This precise approach minimizes material wastage, increases productivity, and results in cost-efficiency for manufacturers and customers alike.
straighten and cut wire
Authoritativeness in the wire straightening and cutting process is also reflected in adherence to industry standards and certifications. Companies that engage in these processes often follow strict quality management systems, such as ISO standards, ensuring that all products meet or exceed regulatory requirements. This adherence not only assures quality but also builds trust with clients who can rely on the products’ integrity for their projects. Regular audits and compliance checks strengthen this authoritative standing in the marketplace.
Trustworthiness is further established through transparency and customer service. Companies often engage with clients to understand specific needs and provide tailored solutions. Whether it's a construction giant requiring large volumes of wire for infrastructure or a niche tech firm needing specialized wire for electronic components, reliable service and open communication channels are crucial. Trusted manufacturers provide detailed production reports and quality certifications upon request, ensuring that every batch of wire can be traced back through the entire production process, further enhancing reliability.
Finally, real-world experience shared by clients and experts in the field highlights the tangible benefits of partnering with specialists in wire straightening and cutting. Case studies often reveal cost savings, efficiency improvements, and successful project executions achieved by working with knowledgeable and experienced suppliers. These insights not only validate the expertise and techniques employed but also serve to reassure potential clients of the benefits they, too, can experience.
In summary, the process of straightening and cutting wire stands as a testament to modern engineering's brilliance, combining precision, expertise, and technological innovation. It is an essential component of countless industries, reinforcing the structures, devices, and systems that form the backbone of our daily lives. Engaging with authoritative and trustworthy manufacturers ensures that quality and reliability are never compromised, setting the foundation for success in every project.