The tube mill line has been a transformative development in the manufacturing industry, offering unprecedented efficiency and precision in the production of tubular products. Over the years, advances in this technology have allowed for various applications across numerous industries, from construction to automotive manufacturing. Understanding the full potential of a tube mill line is crucial for companies aiming to optimize production and maintain a competitive edge.
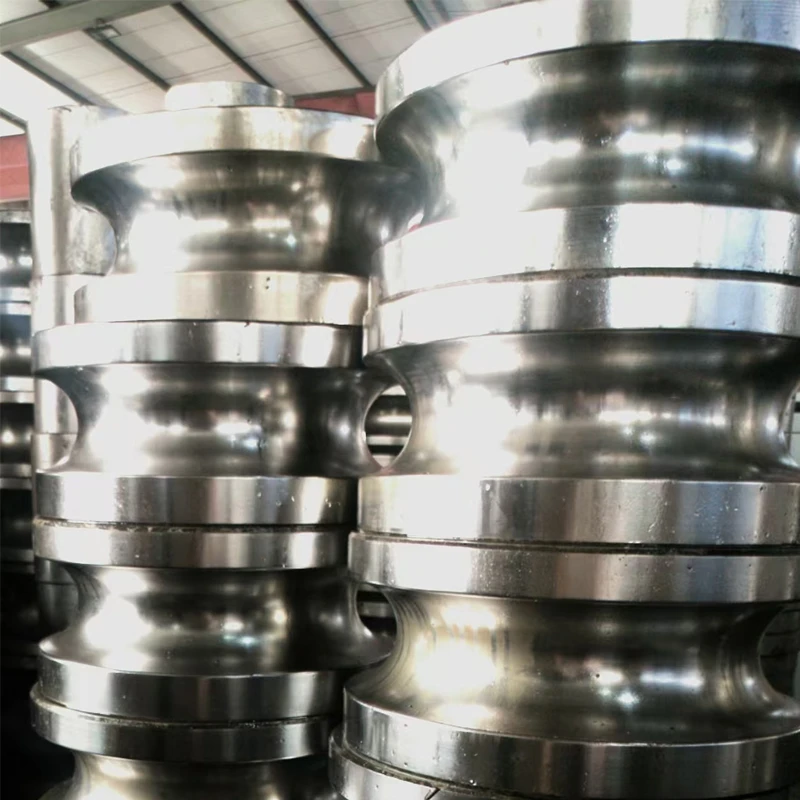
Investment in a tube mill line is a decision guided by a comprehensive understanding of specific machinery and the strategic goals of a business. At the core of its functionality, a tube mill line is designed to manufacture tubes through high-frequency welding from strip material. By refining the process through which steel tubes are shaped and cut, businesses can save on raw materials and reduce waste, contributing to more sustainable operations.
One of the primary experiences reported by industry professionals who have integrated tube mill lines into their production is the significant boost in productivity.
Traditional tube manufacturing methods can be labor-intensive and time-consuming. However, a modern tube mill line automates much of the process, drastically reducing the need for manual intervention and subsequently cutting down production time. The line is capable of maintaining consistent quality across large production volumes, ensuring that each product meets stringent industry standards.
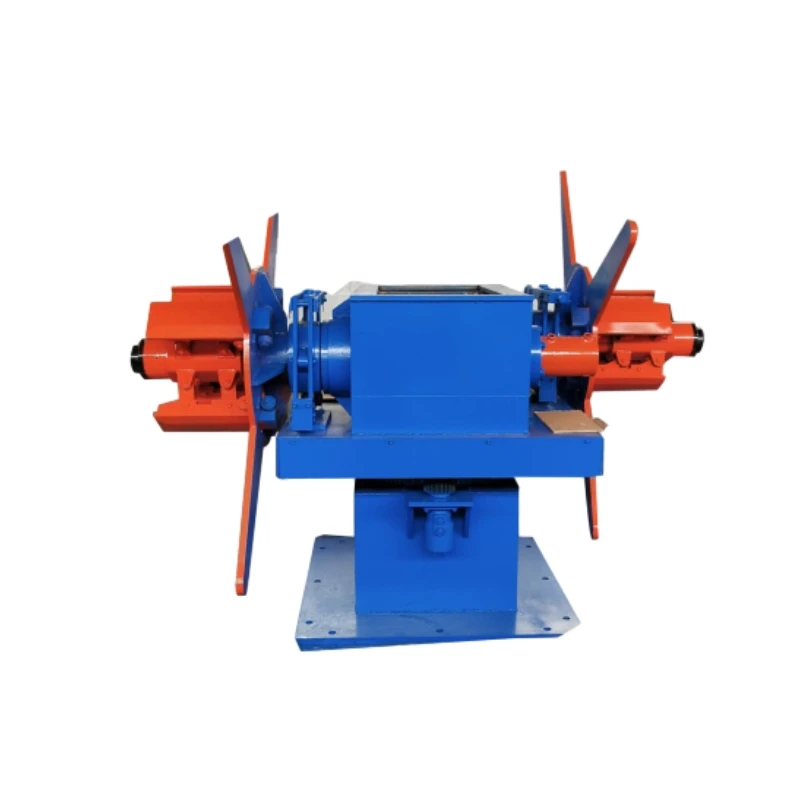
Expertise in operating a tube mill line is a distinct advantage. Ensuring that operators and technicians are well-trained can mitigate unexpected downtimes and machine failures. Regular maintenance and system checks play pivotal roles in sustaining the machine's performance. Manufacturers that invest in specialized training programs for their workforce can maximize the utility and lifespan of their tube mill lines.
In terms of authoritativeness, companies that incorporate the latest tube mill line technologies demonstrate leadership within their industry. By showcasing state-of-the-art equipment and adherence to the highest quality controls, these companies position themselves as industry leaders. Moreover, implementing technologies such as real-time data monitoring, IoT-enabled maintenance alerts, and enhanced diagnostic tools further bolsters a business's authority in delivering quality and reliability.
tube mill line
Trustworthiness is cemented through the delivery of consistent and high-quality products. Clients and partners look favorably upon manufacturers who can reliably meet contract specifications with precision. A tube mill line equipped with precision control systems ensures this level of trustworthiness by producing tubes with the exact dimensions and properties needed for various applications. When quality is non-negotiable, these systems form the backbone of accountability and reliability.
The future of tube mill lines holds even more promise as technology continues to advance. Automation and digital integration are not merely trends but essential components for future production needs. Intelligent systems capable of predictive analytics and machine learning will eventually offer insights into optimizing tube formation processes further, driving down costs and enhancing performance metrics.
For any enterprise seeking to stay competitive in today's fast-paced market, investing in a tube mill line is not merely about boosting production capacity. It's about integrating a scalable solution that can adapt to the complexities of modern manufacturing landscapes. In doing so, businesses not only meet their immediate production needs but also cultivate the potential for long-term growth and innovation.
Concluding, embracing the advanced capabilities of tube mill lines places a company at the forefront of manufacturing excellence. By leveraging new materials, refining production processes, and maintaining a focus on sustainability and precision, manufacturers can continue to expand their influence and reputation on a global scale.