Navigating the intricacies of tube processing machines requires a unique amalgamation of precision engineering and technological expertise. For industries that demand the highest standards in tube fabrication, understanding the nuances of various tube processing machines is paramount. With advancements in manufacturing processes and the integration of sophisticated technology, the landscape of tube processing is continually evolving, making it essential for businesses to stay updated with the latest trends and models.
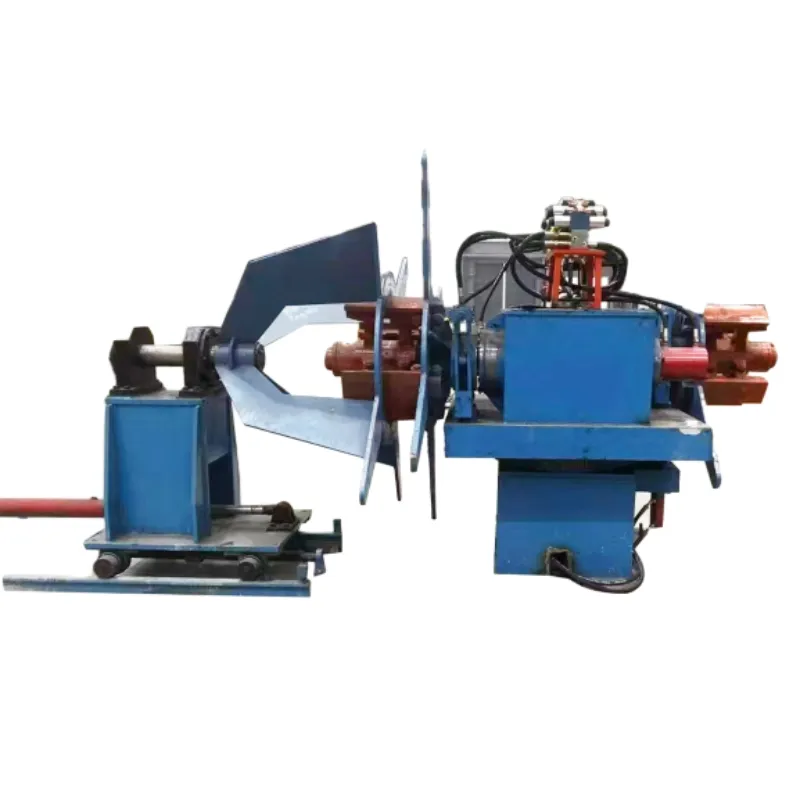
Tube processing machines are the backbone of many industrial applications, ranging from automotive to aerospace engineering. These machines are designed to perform a multitude of functions such as cutting, bending, and forming tubes into complex shapes and sizes with exacting accuracy. One of the standout features of modern tube processing machines is their ability to increase efficiency and reduce waste, thereby contributing to more sustainable manufacturing practices.
Expertise in operating tube processing machines involves a deep understanding of both the mechanical aspects and the digital controls that govern their operation. Operators must be adept at calibrating the machines for different materials, as each type, whether it be steel, aluminum, or copper, requires specific settings to achieve optimal results. Because of this, continuous professional development and training are critical to maintaining high levels of productivity and precision.
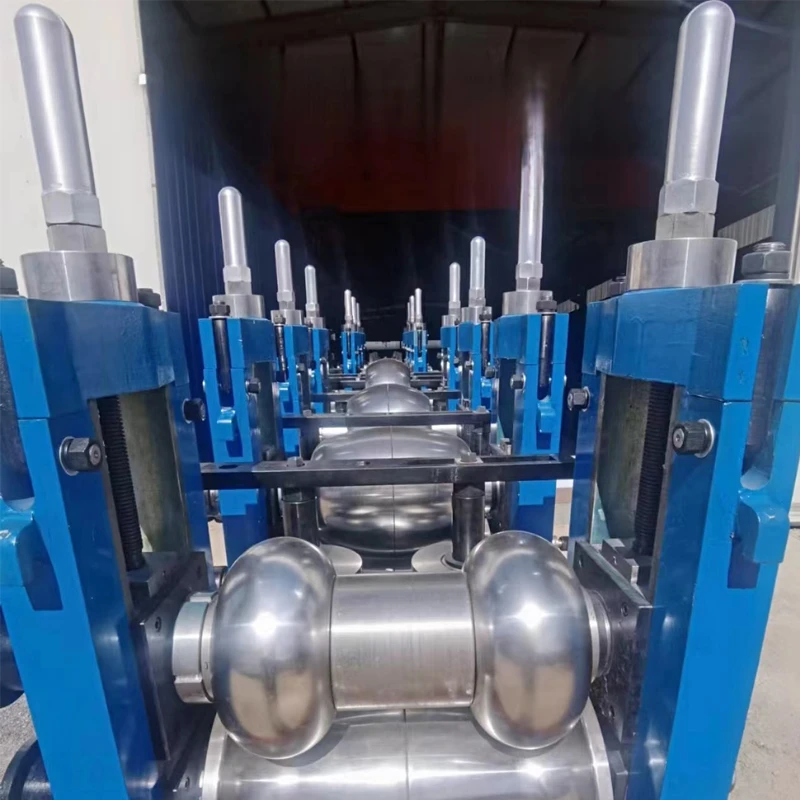
When considering the purchase of a tube processing machine, it is essential to evaluate the specific needs of your production line. Machines can vary significantly in terms of capability and functionality; thus, selecting the right equipment involves assessing your workload requirements, the materials you most frequently process, and the desired speed and accuracy. Consulting with industry experts or manufacturers can provide valuable insights into which machine will offer the best return on investment for your business.
tube processing machine
Reliability and trustworthiness in a tube processing machine are crucial for maintaining uninterrupted production. This is where the brand and model reputation become key considerations. Machines from reputable manufacturers are often accompanied by comprehensive service agreements and warranties, ensuring that any issues can be swiftly rectified, minimizing downtime. Furthermore, reputable brands are more likely to feature the latest technology in automation and user interfaces, enhancing both the usability and safety of the machines.
One of the most significant advancements in tube processing technology is the integration of smart technologies and IoT capabilities. These innovations allow for real-time monitoring and adjustments, ensuring that the production process remains as efficient and accurate as possible. By collecting data on machine performance and output quality, operators can make data-driven decisions to optimize their processes further.
Trust is another cornerstone when dealing with tube processing machines. Businesses must ensure not only that the machines are of high quality but that they also complement existing systems within the production line. Building trust with suppliers and manufacturers through transparent communication and service reliability can forge long-lasting partnerships, ensuring that businesses can rely on their equipment even in times of heightened demand.
In conclusion, tube processing machines represent a critical investment in the future of manufacturing. By focusing on technical expertise, understanding market demands, and prioritizing reliability and trust, businesses can harness the full potential of these machines. Embracing innovation while maintaining a strong foundation in traditional manufacturing best practices will position organizations to thrive in an increasingly competitive industrial landscape.