Tube straightening machines are vital components in the metalworking and manufacturing industries, where precision and efficiency are crucial. Understanding the working principle of these machines can greatly contribute to optimizing production capabilities and ensuring superior product quality. This article delves into the intricate workings of tube straightening machinery, drawing from extensive experience and expertise, to provide a comprehensive guide that underscores their authoritative utility and trusted reliability in modern manufacturing processes.
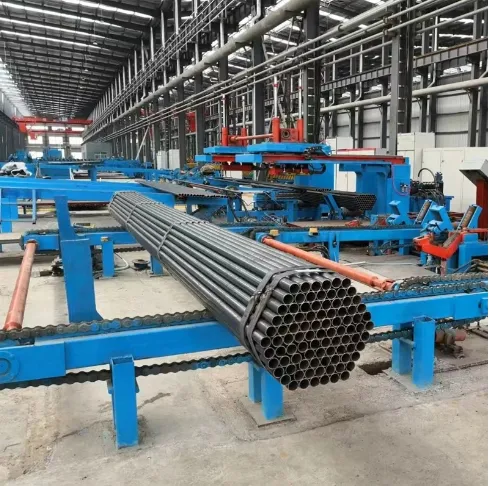
At the core of a tube straightening machine's functionality is the principle of bending. Tubes, whether metal or otherwise, often come out of manufacturing processes with minor imperfections or deformations. These imperfections, if unchecked, could lead to significant issues in assembly lines or in the final application of the tubes. The tube straightening machine corrects these deformations by repeatedly bending the tube in opposite directions with a series of rollers or dies. This alternating bending process effectively eliminates irregularities, ensuring the tube achieves a uniformly straight form.
A further detailed understanding reveals that most tube straightening machines employ a series of precisely aligned rollers, typically arranged in an alternate and offset position. These rollers exert controlled pressure on the tube, manipulating its shape with exactitude. Generally, the rollers are powered by a motor system that is calibrated to deliver the necessary force without causing damage to the tube structure—a balance that requires significant expertise in machine setting and operation.
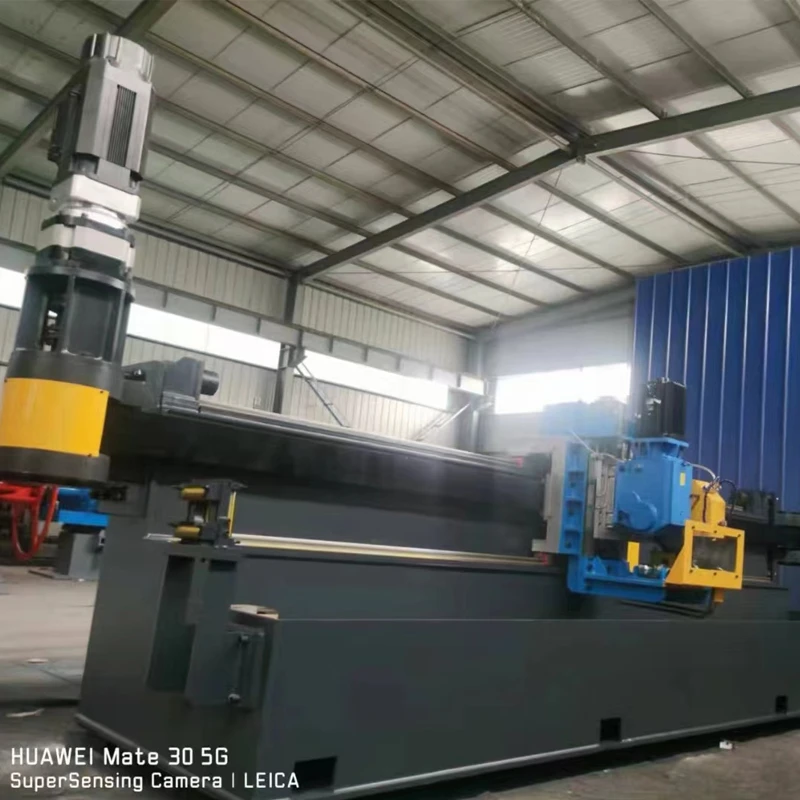
For a more authoritative insight, exploration into the variants of tube straightening machines illuminates their specialized applications. The two most common types are the 'cross-roll' and 'in-line' straighteners. Cross-roll machines utilize multiple sets of roller pairs across the tube's surface, ensuring multi-axis correction. On the other hand, in-line straighteners typically have rollers aligned along a single plane, suited for applications where slight, unidirectional corrections are sufficient.
tube straightening machine working principle
Expertise in operating these machines extends beyond basic mechanical knowledge. Operators must possess a thorough understanding of material properties, such as yield strength and tensile capabilities, ensuring that the straightening process respects the material's limits to prevent structural compromise. Furthermore, they should have the knowledge to adjust the machine's settings according to tube diameter, wall thickness, and material type. This expertise ensures optimal results without incurring unnecessary wear or risk of damage.
To bolster the trustworthiness of these machines, modern advancements have integrated sophisticated control systems. These systems often include sensors and digital interfaces, allowing for real-time monitoring and adjustments. Such features not only enhance the precision of tube straightening but also significantly reduce setup time and error margins. The automated feedback mechanisms are particularly beneficial in high-volume production environments, where consistency and repeatability are paramount.
Moreover, regular maintenance of tube straightening machines is imperative to sustain their reliability and extend their service life. Regular inspections focusing on roller alignment, lubrication systems, and motor integrity are essential. This proactive approach prevents unexpected downtimes and maintains the optimal functioning of the equipment, reinforcing its role as a dependable asset in any manufacturing operation.
In conclusion, the tube straightening machine embodies a crucial intersection of engineering prowess and practical application. Its working principle, centered on the precise bending of material to rectify imperfections, showcases a sophisticated blend of mechanics and control technology. By maintaining high standards of operation, grounded in expertise and continuous innovation, these machines uphold their authoritative presence as indispensable tools in the metalworking realm. Consequently, their strategic implementation can enhance production efficiency, ensuring consistent quality that meets stringent industry standards.