Understanding the landscape of machine moulding can be a transformative experience for manufacturers seeking efficiency and quality in production processes. Machine moulding is pivotal in crafting precise and intricate mouldings essential for various industries. Here's an exploration into the diverse types of machine moulding, providing insights grounded in years of expertise and authoritative industry knowledge.
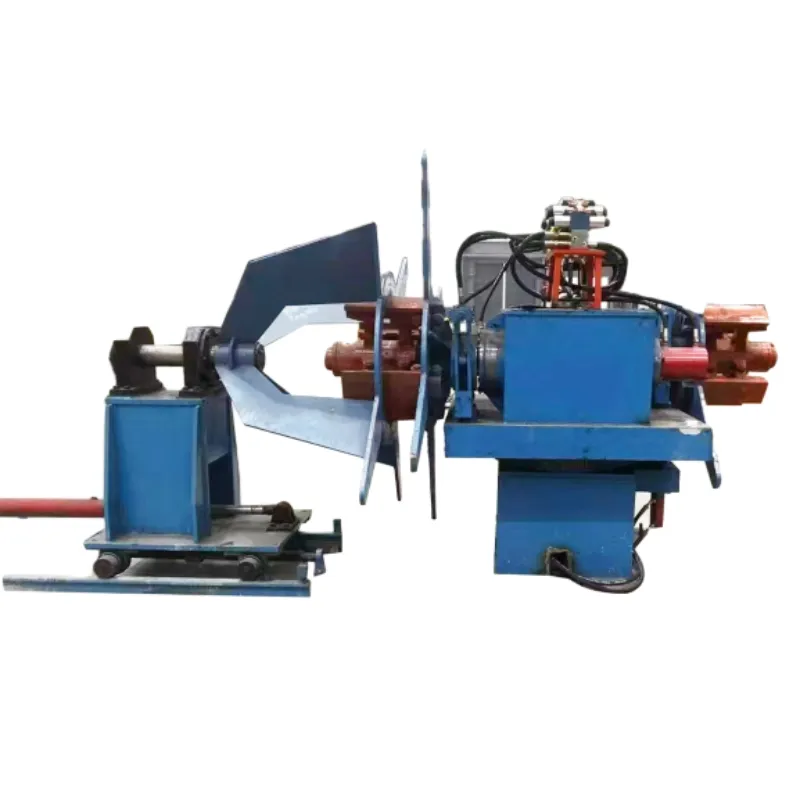
Injection Moulding A Cornerstone in Manufacturing
Injection moulding stands as one of the most prevalent and versatile methods in machine moulding.
It involves injecting molten materials into a mould to form the desired part. This process is renowned for its ability to produce large volumes of parts with high precision and is extensively used for manufacturing plastic products. Among its advantages are the minimal waste production and its suitability for multi-material moulding, which is ideal for creating complex components with varying properties.
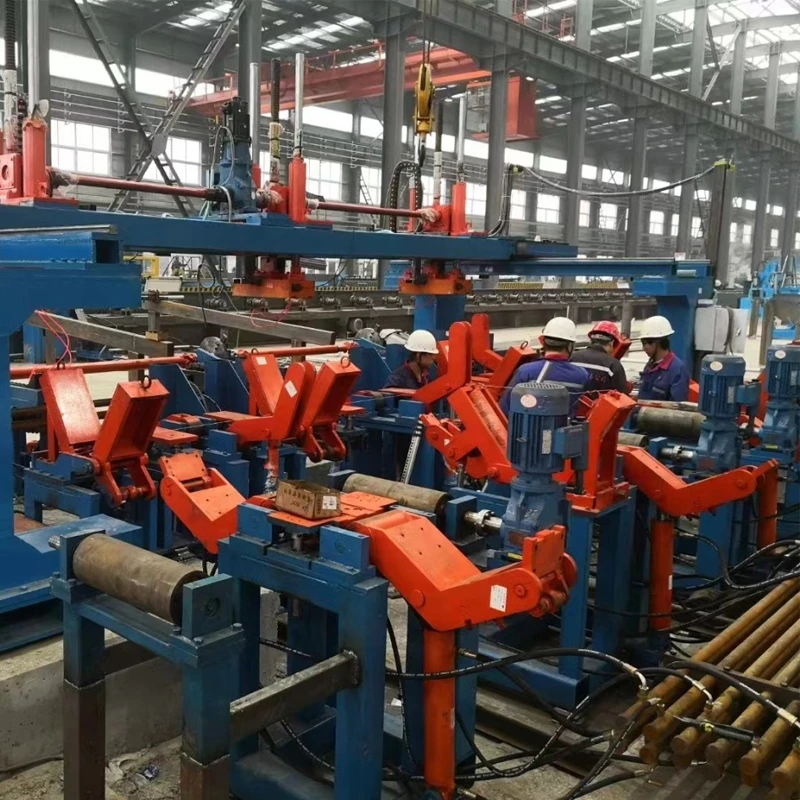
Experience over decades has shown that injection moulding is indispensable for industries like automotive, consumer goods, and healthcare, where consistency and reliability are crucial. Experts highlight the importance of understanding the material properties and the cooling process, as these can significantly impact the final product's quality.
Compression Moulding A Blend of Simplicity and Strength
Compression moulding is a unique process primarily used for producing large, durable items. The process involves placing the material into a heated mould and compressing it to take the shape of the mould cavity. This method is particularly effective for thermosetting plastics and rubber materials, making it ideal for automotive parts, appliance components, and industrial goods.
Professionals with expertise in this domain emphasize that compression moulding's simplicity often belies its robustness. Products manufactured through this process are typically known for their excellent mechanical properties and uniform thickness. Authoritative sources recommend a thorough understanding of the material’s curing cycle to optimize the process, ensuring maximum strength and longevity of the products.
types of machine moulding
Blow Moulding Creating Hollow Parts with Precision
Blow moulding is specifically designed for creating hollow, lightweight parts such as bottles and containers. This technique involves inflating a heated plastic tube within a mould cavity, which then takes the shape of the mould. Blow moulding is distinguished by its rapid production speed, cost-effectiveness, and minimal material wastage, making it favoured for mass production of packaging products.
Throughout years of experience, industry leaders pinpoint the critical importance of air pressure control and material quality in this process. Attention to detail in these areas is essential for achieving uniform wall thickness and preventing defects such as pinholes or weak spots, thus ensuring trustworthiness and satisfaction in the final products.
Rotational Moulding Versatility in Large and Detailed Products
Rotational moulding is unique for its ability to produce large, hollow items in intricate shapes. This method involves loading a liquid or powdery plastic into a mould and rotating it along two axes. The slow rotation allows the material to spread and coat the inside of the mould evenly. Industries such as furniture, toys, and storage tanks frequently utilize this method for its versatility and ability to handle complex design requirements.
Experts attest to its effectiveness in reducing production waste compared to other methods, arguing that the seamless, stress-free products it creates are invaluable in applications requiring durability and complex geometries. Mastery in rotational moulding demands a comprehensive understanding of material flow and cooling rates to produce quality outcomes consistently.
In conclusion, the variety of machine moulding techniques available today offers manufacturers multiple options to tailor their production processes to specific industry needs. With authoritative knowledge and substantial experience, manufacturers can harness these methods to achieve enhanced efficiency, superior product quality, and customer satisfaction. Aspiring industry leaders equipped with this understanding can confidently navigate the intricate landscape of machine moulding, driving innovation and excellence in their respective domains.