Roll forming machines are integral to the manufacturing industry, serving as the backbone for producing uniform cross-section components, such as roof panels, wall claddings, door frames, and various metal components. The diverse types of roll forming machines available make them suitable for a broad spectrum of applications, each designed with specific functionalities to meet different industrial demands. Understanding these machine types not only showcases technical expertise but also enhances decision-making when selecting machinery for specific production needs.
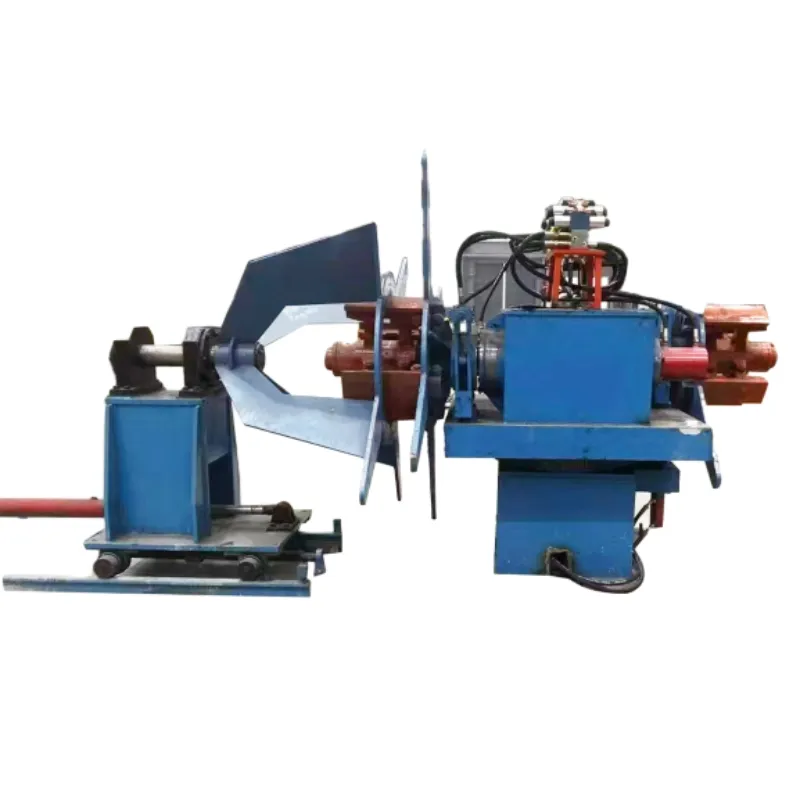
Firstly, single-duty roll forming machines are the simplest type, designed for operations where the production requirements are straightforward and consistent. These machines are optimal for manufacturing components with a single, constant profile. The straightforward nature of the machinery ensures ease of use and low maintenance, making them a cost-effective choice for companies focused on high-volume, single-profile production runs.
The next category,
multi-profile roll forming machines, offers versatility. These machines are engineered to adapt to different profiles and dimensions. They are ideal for industries that require a range of product varieties without the need for multiple machines. A significant advantage is their ability to switch swiftly between different product designs, minimizing downtime and maximizing efficiency. This adaptability is increasingly important in today's competitive markets where customer demands can shift rapidly.
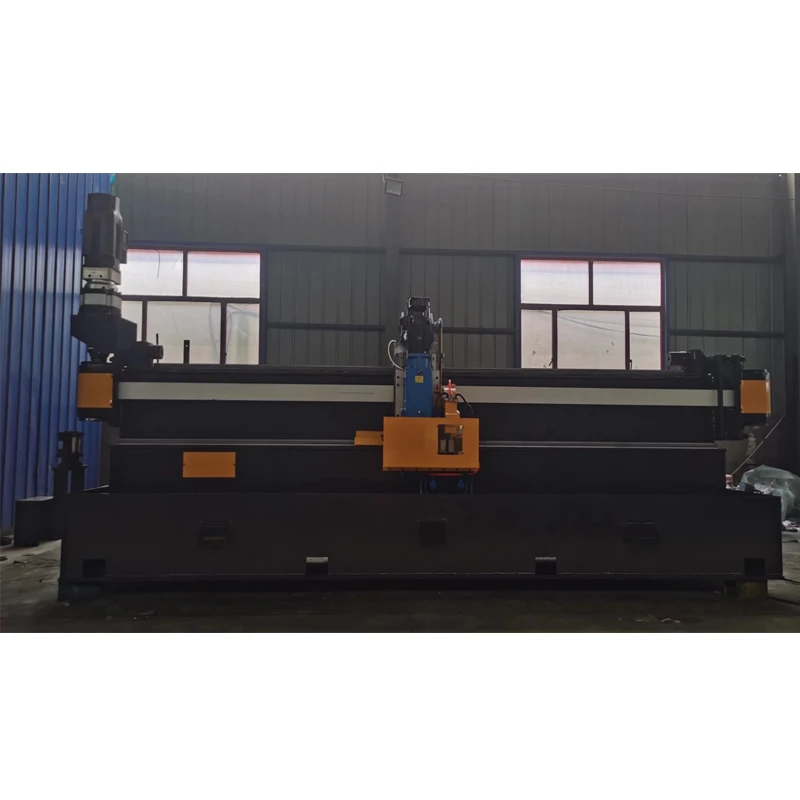
For industries focused on high-strength materials, the reinforced roll forming machines come into play. These machines are specifically designed to handle thicker and harder metals like steel and aluminum alloys. Equipped with enhanced structural frameworks and advanced tooling systems, reinforced roll forming machines ensure precision in rolling operations without compromising the mechanical integrity of the materials being processed. They are crucial in sectors such as automotive and aerospace, where material strength and precision are paramount.
In contrast, flexible roll forming machines are designed for dynamic production environments. These machines can adjust their rollers to create variable cross-section profiles along the length of the material. This capability allows for the creation of highly specialized and complex products, often used in architectural applications where aesthetics and functionality must align perfectly. The seamless integration of servomotors and computer control systems in these machines exemplifies modern advancements in manufacturing technology, highlighting expertise and a forward-thinking approach in production processes.
types of roll forming machine
Custom roll forming machines represent a pinnacle of specialization. Tailor-made to meet specific client specifications, these machines are often the result of collaborative engineering efforts and detailed analysis of production needs. Custom machines embrace the unique requirements of niche markets, providing bespoke solutions that standard machinery could not accommodate. Their design and development process exemplify expertise in engineering, fabrication, and intricate knowledge of material behavior, cementing their status as authoritative figures in niche manufacturing sectors.
Furthermore, double-high roll forming machines have gained traction for their efficiency in using space and resources. By doubling the horizontal space, they allow the simultaneous production of two different profiles, effectively doubling the output without requiring additional floor space. This innovation is ideal for manufacturers looking to maximize their production capabilities while adhering to spatial constraints. The dual production lines within a single machine highlight both the efficiency in design and the potential for increased profitability, emphasizing a trustworthy investment for future-oriented businesses.
Finally, portable roll forming machines hold significance for on-site operations. Lightweight and easily transportable, these machines allow for the manufacturing of components directly on location, making them invaluable in construction and large-scale installations. They enable real-time adjustments and customizations, reducing the lead time and logistical complexities associated with off-site production. The portability and onsite customization abilities ensure that businesses can meet the ever-evolving demands of the construction industry with reliability and precision.
In conclusion, roll forming machines, with their diverse types and applications, underscore the importance of matching machine capabilities with manufacturing requirements. Whether focusing on efficiency, adaptability, strength, or customization, each type of machine plays a vital role in advancing industrial capabilities. Leveraging their specific advantages not only ensures optimal production processes but also solidifies a company’s standing as a leader in quality and innovation. Understanding and choosing the right type of roll forming machine is pivotal to maintaining competitive advantage and operational excellence in the fast-paced world of manufacturing.