Roll forming, an intricate process in the manufacturing industry, offers a myriad of types that cater to diverse applications, each with unique benefits and challenges. The plethora of roll forming types enables industries to tailor their manufacturing processes to precision, durability, and cost-effectiveness, ensuring that the products meet both functional and aesthetic standards. As a tried-and-true method, roll forming excels in producing long lengths of metal components efficiently, showcasing a mastery of technique inspired by years of industrial evolution and expertise.
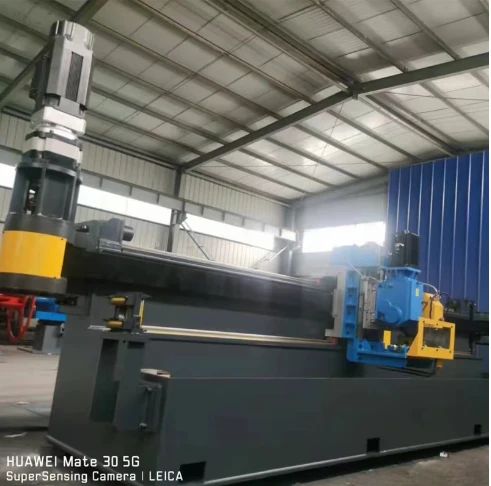
Integral to understanding roll forming is recognizing its variations, which can be broadly classified into several types standard roll forming, incremental roll forming, and flexible roll forming, each serving distinct operational needs.
Standard roll forming is arguably the most prevalent, renowned for its efficiency and straight-path production line. This type involves passing a long strip of sheet metal through a series of rollers, each carefully positioned to incrementally bend the metal into a predetermined shape. Key industries such as transportation, construction, and automotive rely heavily on standard roll forming for components like door frames and roofing panels. Its benefits include low tooling costs and the ability to handle high production volumes with consistent quality, appealing to companies aiming for cost-effectiveness without sacrificing precision.
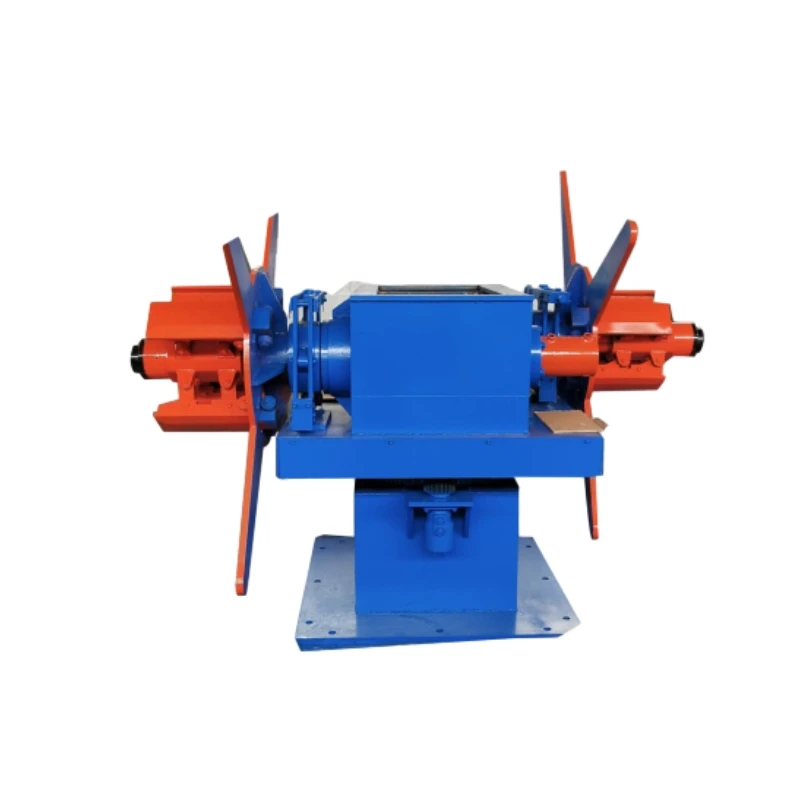
For more complex shapes and profiles,
incremental roll forming steps in as a robust option. Unlike its standard counterpart, incremental roll forming involves multiple steps and phases, allowing the production of more sophisticated shapes without altering the simplistic linear path of roll feeding. This method materializes as a prominent choice for those looking to push the boundaries of design while maintaining the structural integrity of materials. Examples of products born from incremental roll forming include intricate channels and custom profiles required in machinery and specialty construction frameworks. Its versatility is unmatched, albeit at the cost of efficiency, as the increased number of steps can elongate production time.
Flexible roll forming stands at the intersection of creativity and adaptability, accommodating frequent changes in profile design within a single production batch. This type leverages advanced computer-controlled systems to modify the spacing, configuration, and operation of rollers dynamically. It's exceptionally advantageous for industries that require high customization and short production runs, like aerospace and high-end automotive sectors, where unique and precise parts are critical. Flexible roll forming reduces the need for multiple sets of tools, a significant leap forward in addressing changeover times, and is perfectly aligned with modern just-in-time manufacturing philosophies.
types of roll forming
Though impressive in their capabilities, each roll forming type demands a nuanced understanding of material properties and machine dynamics. The choice between them hinges on several factors the complexity of the final product shape, production volume requirements, material thickness, and the specific tolerances needed.
Eminent manufacturers invest heavily in technological advancements to expand the capabilities of roll forming. Innovations such as servo-electric drives and hybrid systems have enhanced the precision and speed of the process, ensuring that these manufacturing stalwarts remain viable contenders in a rapidly advancing industrial landscape.
In the realm of sustainability, roll forming shines with its material efficiency, often resulting in minimal waste compared to other manufacturing processes. Industries continuously explore configurations that utilize less energy and produce components with longer lifespans, aligning closely with environmental and economic goals.
From standard, incremental, to the heralds of flexibility, the types of roll forming collectively represent an orchestra of precision and quality. The choice of method not only dictates the efficiency and cost-effectiveness of production but also defines the potential for innovation and the realization of complex designs. This intricate dance of metal and machinery, grounded in decades of expertise, underlines the authority and trustworthiness that roll forming has cemented within the industrial manufacturing narrative. Recognized not merely as a method but as a cornerstone of modern manufacturing, it continues to shape industries with unyielding confidence and expertise.