Wire straighteners are an essential tool in a wide array of industries, acting as a crucial component in the manufacturing and processing of wire products. In industries such as automotive, aerospace, and electronics, where precision is non-negotiable, the accuracy and reliability of wire straighteners can define the quality of the final product. With advancements in technology, wire straighteners have become more sophisticated, providing better results and greater efficiency. The key lies in understanding the mechanics of these machines, the innovations ushered in by recent technological progress, and how they contribute to overall productivity.
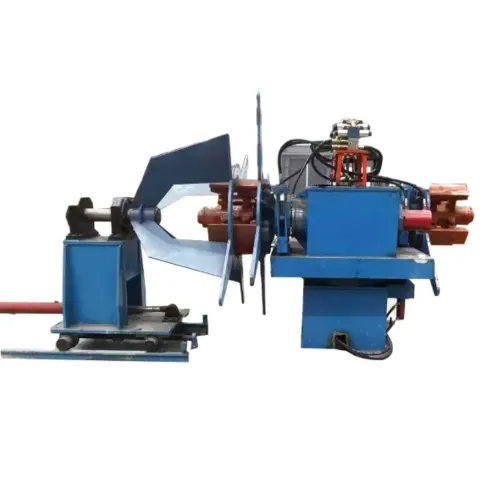
A wire straightener effectively rectifies coil set and camber issues in wires, ensuring they are perfectly straight for further processing or for end-use applications. This process not only improves the appearance of the product but also maximizes its functionality — whether that be electrical conductivity, load-bearing capacity, or precise fit into mechanical components. At the core of wire straightening technology is its ability to eliminate torsional stress and uneven material distribution, which can compromise both performance and safety.
A display of expertise in wire straightening technology begins with understanding the diversity in models and mechanics. Traditional models were manually-operated, offering limited precision. However, modern wire straighteners have evolved, incorporating hydraulic, pneumatic, and digital controls which offer unprecedented accuracy and efficiency. Digital controllers especially have revolutionized the industry, allowing operators to set precise specifications and monitor functioning in real time. These advanced controls ensure that operators can handle a variety of different wire materials and sizes with minimal adjustments, drastically reducing downtime and increasing output.
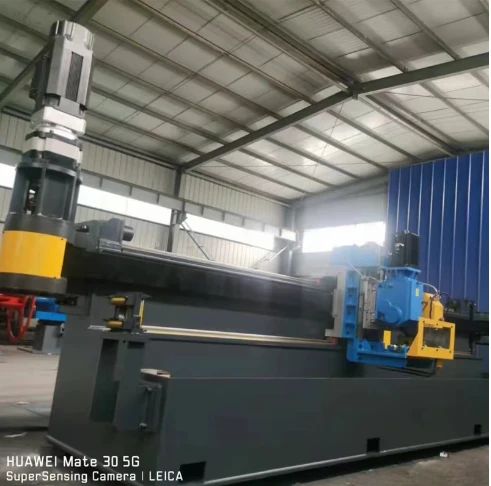
The expertise and authority in the use of wire straighteners are also highlighted by the variety of wire types these machines can handle.
Stainless steel, copper, and aluminum wires all interact with the straightening process differently. An authoritative understanding of metallurgy and material science is crucial in optimizing the straightening process for each type. Advanced models can be equipped with sensors that adjust for temperature, tensile strength, and diameter changes, ensuring uniformity regardless of external conditions.
wire straightener
Further expressing authoritativeness, many leading manufacturers now offer customization options, hand-in-hand with seasoned technicians who bring a wealth of experience to bear. They can help tailor a wire straightener to fit specific industry needs, whether it’s integrating with other manufacturing systems or adapting to unique wire compositions. As a result, businesses can achieve higher efficiency and product quality, reducing waste, saving time, and cutting costs.
The trustworthiness of a wire straightener rests upon its safety features and user-friendly design. Industry-grade safety protocols now often come standard, such as automatic shutoffs and emergency stop functions that protect operators and equipment alike. Additionally, the design of these machines has progressively become more intuitive. User interfaces are developed to minimize operator error, and maintenance systems are simplified, ensuring that even those less technically inclined can manage the machine effectively.
Real-world experience demonstrates that investing in a high-quality wire straightener offers significant returns. Testimonials from various sectors confirm that enhanced precision leads to fewer manufacturing errors, thereby increasing customer satisfaction and company reputation. In a competitive market, the capability to consistently produce high-quality products reinforces a company's standing as a trustworthy partner. It underlines the importance of implementing robust wire straightening systems as part of a larger strategy to optimize manufacturing processes.
In conclusion, wire straighteners are transforming industries where precision and efficiency are paramount. Modern technological advancements have pushed the boundaries of what was once thought possible. As they continue to evolve, wire straighteners will play an increasingly critical role in streamlining operations across sectors. Choosing the right equipment, equipped with contemporary features and backed by expert knowledge, will indisputably provide a competitive edge, reaffirming the essential nature of these machines in a manufacturer's arsenal. Investing in quality wire straightening solutions not only prepares a company for the challenges of today but also positions it advantageously for the promising opportunities of tomorrow.