In the realm of metal fabrication, the precision processes of wire straightening and cutting hold paramount importance. These techniques not only shape the foundational structure of industries but also ensure exactness and efficiency across numerous applications. Harnessing the right equipment and methods in these processes can significantly transform production dynamics, enhance throughput, and boost the quality of the final product.
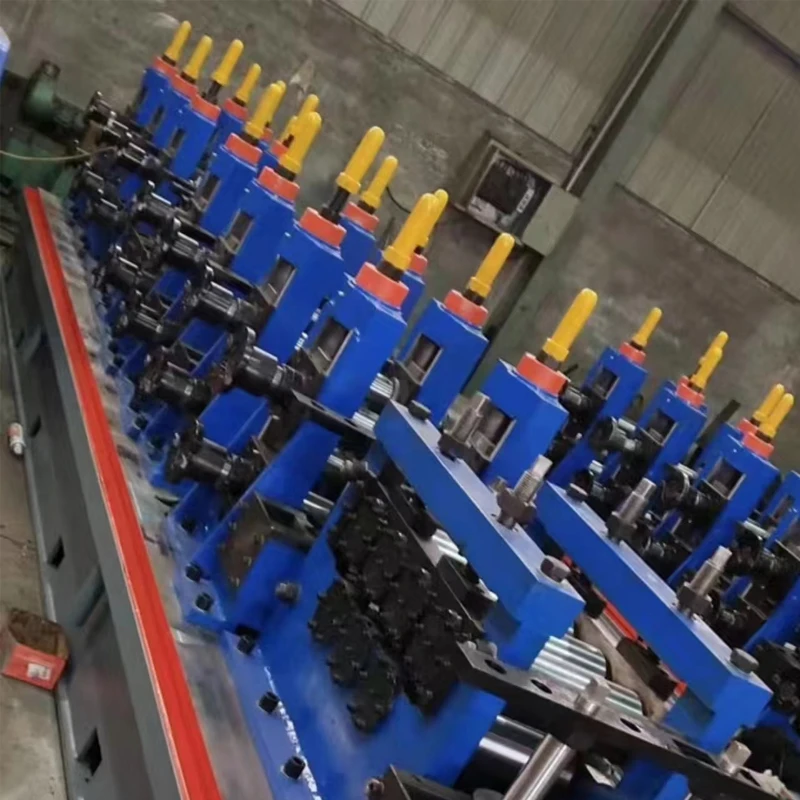
Wire straightening and cutting machinery serves as one of the most critical components in manufacturing environments that require exactitude and consistency. At its core, wire straightening aims to eliminate curvature and torsion in wire products, ensuring that they meet stringent standards for straightness and dimensional accuracy. This step is foundational because any imperfection at this early stage could lead to inefficiencies or defects in the subsequent stages of manufacturing.
In terms of expertise, achieving optimal wire straightness necessitates the employment of advanced machinery equipped with precision rollers and cutting-edge straightening mechanisms. These machines operate by leveraging driven rollers that pull the wire through a series of die plates, which progressively correct any deformity. High-speed cutting is then executed to match specified lengths with impeccable accuracy. Manufacturers employing these advanced systems favor them for their ability to reduce wastage, improve cycle times, and maintain constant tension, thus ensuring consistent high-quality results.
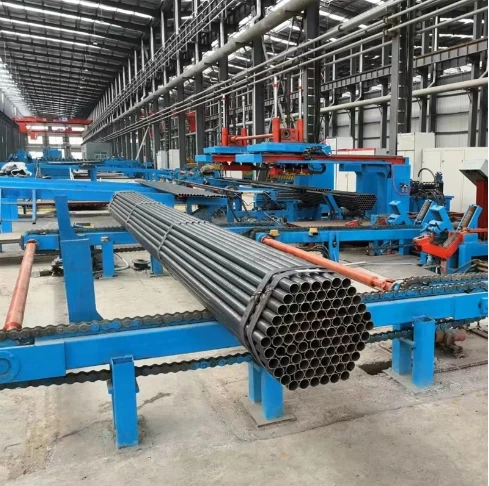
Authoritative reliability in wire straightening and cutting is marked by the selection of robust, state-of-the-art equipment researched and vetted by industry experts. Partnerships with reputable manufacturers provide warranty assurances and access to cutting-edge technological advancements. With a focus on automation, producers can integrate programmable logic controllers (PLCs) and advanced software systems to increase precision and minimize human error.
wire straightening and cutting
Establishing trustworthiness with clients in markets like aerospace, automotive, and construction requires the demonstration of compliance with international quality standards, such as ISO 9001 and other relevant certifications. Testing each batch for straightness and length tolerance ensures these standards are met and fosters long-term customer confidence.
Further, the adaptability of wire straightening and cutting machines to work with various materials—ranging from basic ferrous and non-ferrous wires to more complex alloys—underscores their versatility and value. This adaptability is crucial for manufacturers who need to maintain flexibility in responding to market demands and potentially fluctuating material costs.
From an experiential standpoint, integrating these sophisticated systems provides manufacturers with real-time feedback and analytics, allowing for continuous process improvement. Machine learning algorithms can analyze performance data to predict maintenance needs and optimize operational efficiency, providing a distinct competitive edge in lean manufacturing environments.
In conclusion, the domain of wire straightening and cutting represents a convergence of high precision, expert engineering, and reliable execution. Businesses leveraging these processes and technologies not only enhance product quality but also position themselves as leaders in their respective industries by adopting efficient, forward-thinking manufacturing practices. For any company in fields demanding the highest standards of production integrity, investing in superior wire straightening and cutting solutions is not merely an option; it is a necessity for sustained success.