Automatic pipeline welding machines are revolutionizing the way industries approach large-scale welding projects. These machines offer unmatched efficiency, accuracy, and cost-effectiveness by automating the welding process. In industries such as oil and gas, petrochemical, and construction, where precision and safety are paramount, incorporating an automatic pipeline welding machine presents multiple advantages over traditional manual methods.
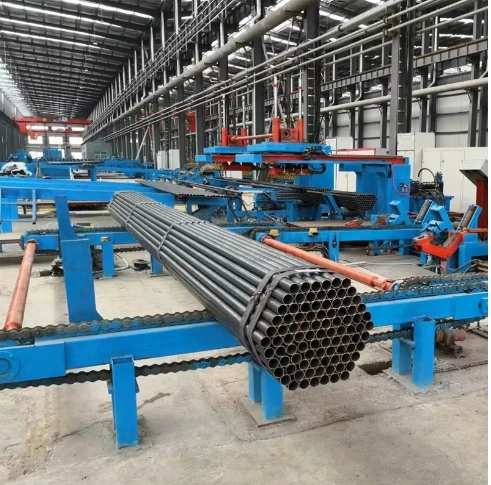
One of the most compelling reasons to adopt automatic pipeline welding technology is its ability to consistently produce high-quality welds. Unlike manual welding, where human fatigue and skill level can lead to inconsistent welds, automated machines ensure each weld meets industry standards. This repeatability mitigates the risk of defects, which, if left unchecked, could lead to costly repairs or even catastrophic failures in critical infrastructures.
Expert operators and industry professionals find that automatic pipeline welding machines significantly enhance productivity. A machine can operate for extended periods without breaks, maintaining a steady pace that would be impossible for a human welder to match. This leads to faster project completion times without sacrificing quality. In high-stakes environments where time is money, this advantage cannot be overstated.
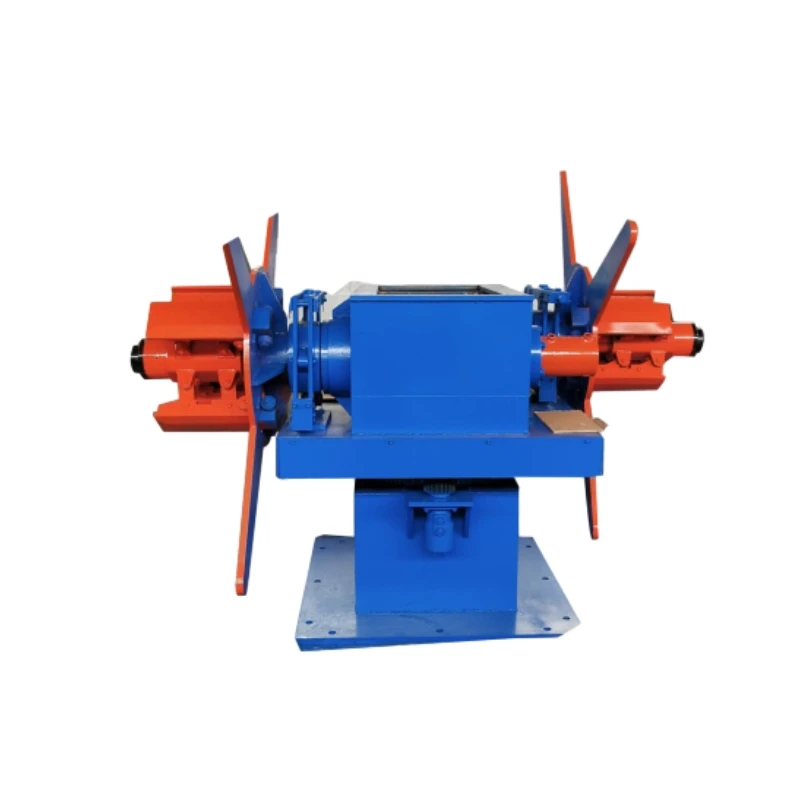
Furthermore, the accuracy with which these machines operate enhances safety on the job. By reducing the need for human welders to be in potentially hazardous environments, such as confined spaces or at great heights, the likelihood of accidents decreases. Automatic welding machines can also be equipped with advanced monitoring systems that provide real-time feedback, allowing for immediate adjustments and improving overall workplace safety.
From a cost perspective, although the initial investment in an automatic pipeline welding machine might seem substantial, the return on investment is quickly realized. Reduced labor costs, fewer material wastages, and minimized downtime translate into significant savings over time. Plus, the longevity and durability of the machine extend its utility over many projects, maximizing the return on capital expenditure.
automatic pipeline welding machine
Industry experts highlight the versatility of modern automatic welding machines, as they can be adapted for various welding techniques, including MIG, TIG, and others, depending on the material and project requirements. This adaptability makes them suitable for a wide range of applications, ensuring that whether you're dealing with thin-walled pipelines or solid steel joints, the machine can handle the task with precision.
Trustworthiness is inherent in technology that is continuously evolving. Manufacturers of automatic pipeline welding machines are committed to innovation, frequently updating their products to adhere to the latest industry codes and standards. This commitment not only assures compliance but also builds client trust, knowing that they are investing in state-of-the-art technology that prioritizes safety and quality.
As the industry moves towards more sustainable practices, automatic welding machines are also becoming environmentally friendly. By optimizing energy use, minimizing scrap, and enabling precise material utilization, these machines contribute to the reduction of the carbon footprint associated with large-scale welding projects. This aspect showcases a commitment not only to efficiency and productivity but also to global environmental initiatives.
In conclusion, incorporating automatic pipeline welding machines into your operations exemplifies a forward-thinking mindset, showcasing a commitment to quality, efficiency, and safety. By combining expertise, authority, and trustworthiness, these machines not only meet but often exceed the stringent demands of pipeline construction and maintenance. Embracing this technology is not just an investment in equipment but an investment in the future of welding craftsmanship.