The world of pipeline construction has been revolutionized by the advent of automatic pipeline welding machines, which stand as a testament to technological advancement in this domain. These machines possess the capability to make a significant impact on both the efficiency and quality of pipeline projects, offering unparalleled benefits over traditional welding methods.
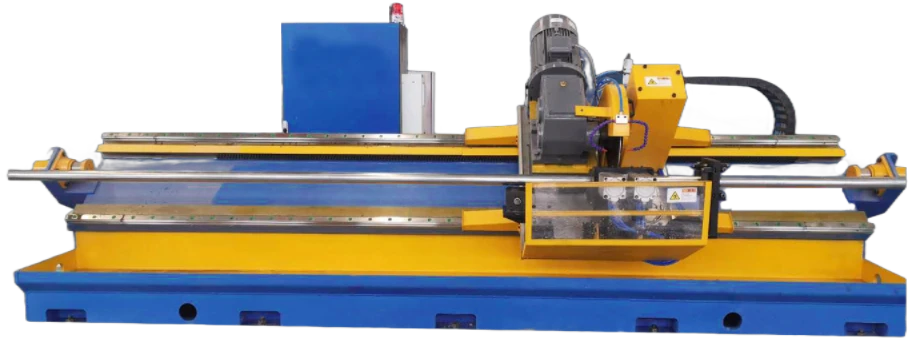
Automatic pipeline welding machines are designed with precision engineering, driven by sophisticated algorithms and controlled by computer systems that ensure consistent weld quality. This translates into a dramatic reduction in human error,
a key concern in manual welding. Human welders, though skilled, are susceptible to fatigue and inconsistency, especially in challenging environments. Automatic machines, on the other hand, operate tirelessly, executing each weld with exacting precision, thus ensuring the integrity and safety of the pipeline.
One distinctive advantage of these machines is their ability to work in a variety of environments and positions. Whether it's laying pipelines offshore or in remote desert locations, automatic welding machines can be adapted to weld pipelines at different angles and under various environmental conditions. This adaptability not only enhances their efficiency but also greatly broadens the scope of projects that can be undertaken with confidence. Additionally, they can work with different materials, accommodating steel, alloys, and even composite materials which are increasingly used in modern pipeline systems.
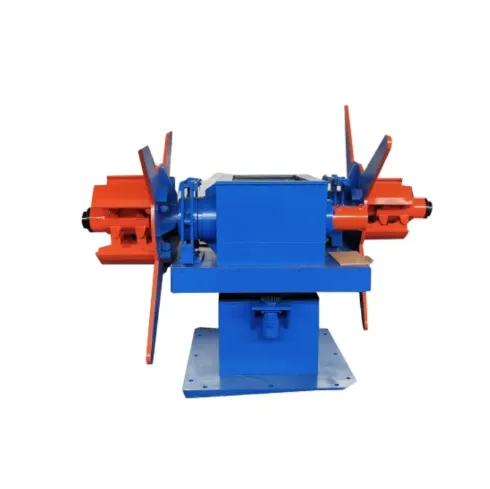
From an expertise standpoint, the machinery involves complex automation technology that requires minimal manual intervention. Their design incorporates advanced control systems, such as programmable logic controllers (PLCs), which oversee the welding process, ensuring optimal heat input and consistent penetration. These systems are coupled with real-time data feedback, providing operators with detailed diagnostics to make informed decisions on maintenance and operations, thus reducing downtime and enhancing productivity.
automatic pipeline welding machine
In terms of authoritativeness, the role of automatic pipeline welding machines is endorsed by industry leaders and regulatory bodies. Historically, manual welding was the standard in the industry, but the paradigm is shifting as more companies and authorities recognize the superior quality and reliability of automated systems. This shift is backed by research and case studies illustrating reduced project timelines and enhanced safety records on projects utilizing automatic welding technologies.
A key element of trustworthiness in automatic pipeline welding machines lies in their robust safety features. These machines are designed to prioritize operator safety, incorporating features such as emergency stop functions, sensor systems to prevent accidents, and protective enclosures to shield workers from welding arcs and fumes. Additionally, consistent quality monitoring reduces the likelihood of welding defects, which can be a source of catastrophic failures in pipeline systems. This enhances the credibility of projects executed using such machines, ensuring peace of mind for stakeholders.
Companies investing in automatic pipeline welding machines often find a swift return on investment. Despite the initial cost outlay, the increased welding speed, reduced labor costs, and minimized error rates contribute to significant cost savings over the lifecycle of a project. Welders in the field are transitioned to more supervisory roles, monitoring machine performance rather than executing the welds manually. This shift not only optimizes labor resources but also elevates the skill set required in the industry, potentially leading to better wages and job satisfaction for skilled workers.
In conclusion, automatic pipeline welding machines represent a paradigm shift in pipeline construction. Their contribution to efficiency, quality, safety, and cost-effectiveness makes them an indispensable asset in modern engineering projects. As technology evolves, so too will the capabilities of these machines, further cementing their role in the future of pipeline infrastructure.