Straightening bars is an integral part of many industrial and mechanical processes, demanding precision and efficiency. Enter the bar straightening tool, a specialized piece of equipment that not only simplifies this complex task but also enhances the quality and safety of the end product. This tool is essential in industries ranging from construction and automotive to aerospace and metal fabrication, where straightening bars accurately is non-negotiable.
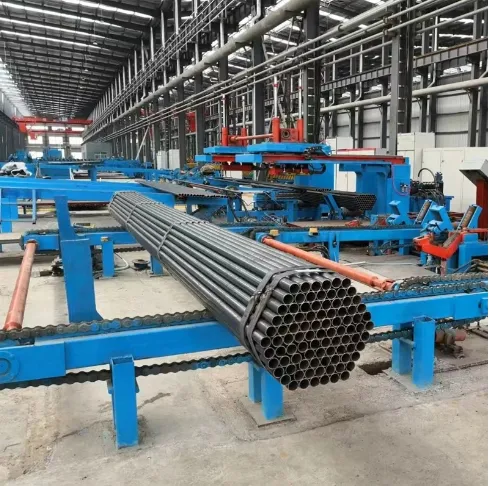
The primary purpose of a bar straightening tool is to correct any bends or imperfections in metal bars, rods, or tubes. This operation is crucial because even the slightest deformity can impact the structural integrity and performance of the final product. A well-straightened bar ensures that the material can withstand stress and load, fulfilling its intended design specifications.
When investing in a bar straightening tool, it is essential to consider its precision, adaptability, and user-friendliness. These are attributes only attainable from manufacturers that lead the industry in innovation and quality. A tool that scores high in these areas can drastically minimize downtime and increase productivity by reducing the need for rework and manual adjustments. Often constructed from high-grade, durable materials, these tools are designed to endure the rigorous demands of industrial use.
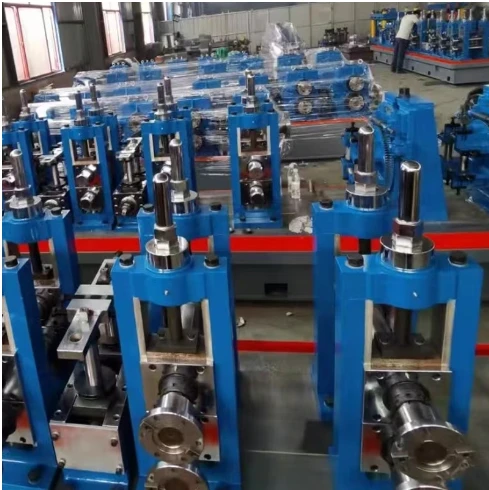
Using a bar straightening tool also significantly enhances safety in the workplace. Manual straightening can pose risks of physical strain and injury to workers, especially when dealing with heavy or unwieldy materials. Automated straightening tools mitigate these risks via push-button operations and safety features that reduce human intervention and error. In turn, they foster a safer working environment, which should always be a priority for operations of any scale.
Expert operators and industry veterans often highlight the role of this tool in ensuring uniformity and consistency in production. Automated systems come equipped with advanced technology that allows for continuous monitoring and adjustments, ensuring that each piece meets stringent quality standards. This level of control helps in maintaining the uniformity necessary for batch productions, ultimately translating to higher levels of customer satisfaction.
bar straightening tool
Technical advancements have made bar straightening tools more sophisticated and precise than ever. Modern tools offer CNC (Computer Numerical Control) integration, which allows for programmable settings and greater accuracy. This capability is particularly beneficial for industries requiring high precision, such as aerospace engineering and automotive manufacturing, where even minute deviations can lead to catastrophic failures.
Reliability and maintenance are considerations no business can afford to ignore. The latest generation of tools boasts self-diagnostic features that alert users to potential issues before they lead to downtime. In addition, manufacturers provide dedicated support and maintenance programs to assist in optimizing the tool's lifecycle. This backup ensures that operations remain uninterrupted and that the tool offers a high return on investment over time.
Case studies and testimonials often illustrate the transformative impact of bar straightening tools on businesses. Companies have reported measurable improvements in both efficiency and quality after upgrading their straightening equipment. These tools enable faster production times without compromising accuracy or safety, allowing organizations to meet higher demands and expand their operational capability.
Selecting the right bar straightening tool is not merely a matter of investment; it is a strategic decision that aligns with a company's long-term goals. The optimal tool is one that integrates seamlessly into current systems, maximizes output, and upholds the high standards of product integrity that define today's competitive marketplace.
In conclusion, bar straightening tools represent a pivotal technology for industries dependent on metal fabrications. They marry technological innovation with practical application, offering unmatched expertise, authority, and trustworthiness in their ability to enhance both productivity and safety in the workplace. Whether you are modernizing current operations or embarking on new projects, these tools are indispensable assets that deliver substantial benefits across the board.