The process of cold rolling aluminium is a sophisticated technique that holds immense value in the manufacturing industry, especially for those seeking to create high-performance aluminium components with precise tolerances. This technique is built upon years of engineering expertise and extensive industry experience, positioning it as a cornerstone in creating high-quality aluminium products.
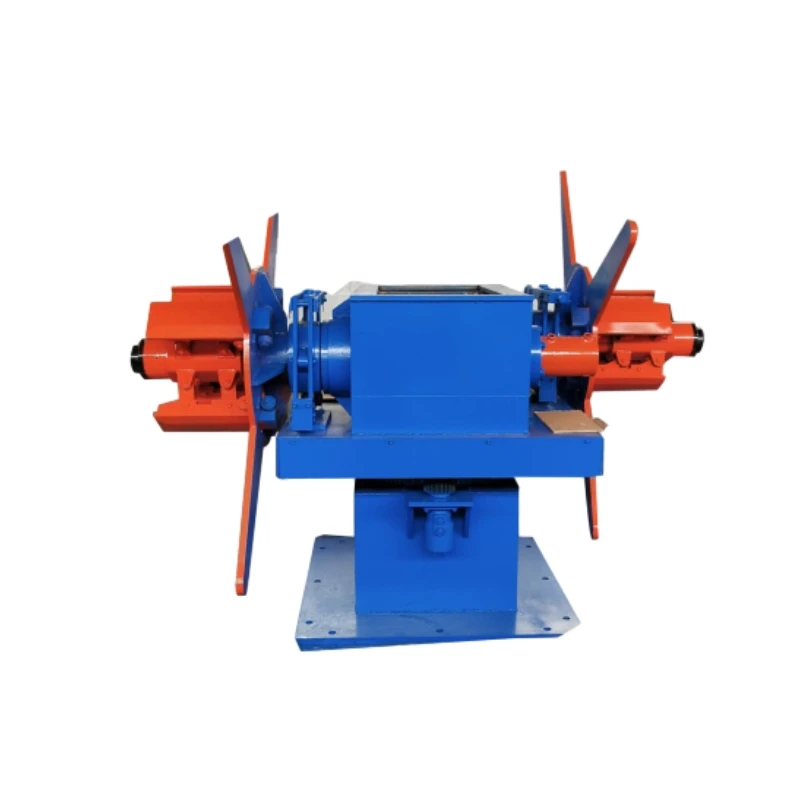
Cold rolling is a process by which aluminium sheets or strips are passed through rollers at temperatures below the recrystallization temperature of the metal. Unlike hot rolling, cold rolling offers enhanced dimensional accuracy and an improved surface finish, critical components for industries like aerospace, automotive, and electronics, where precision is non-negotiable.
Practically speaking, the cold rolling process starts with the preparation of aluminium sheets that have typically been pre-cooled. Once prepared, the aluminium strip enters a rolling mill, where rollers exert high pressure. This compression alters the microstructure, resulting in a product with increased hardness and strength, attributes highly sought after in structural applications.
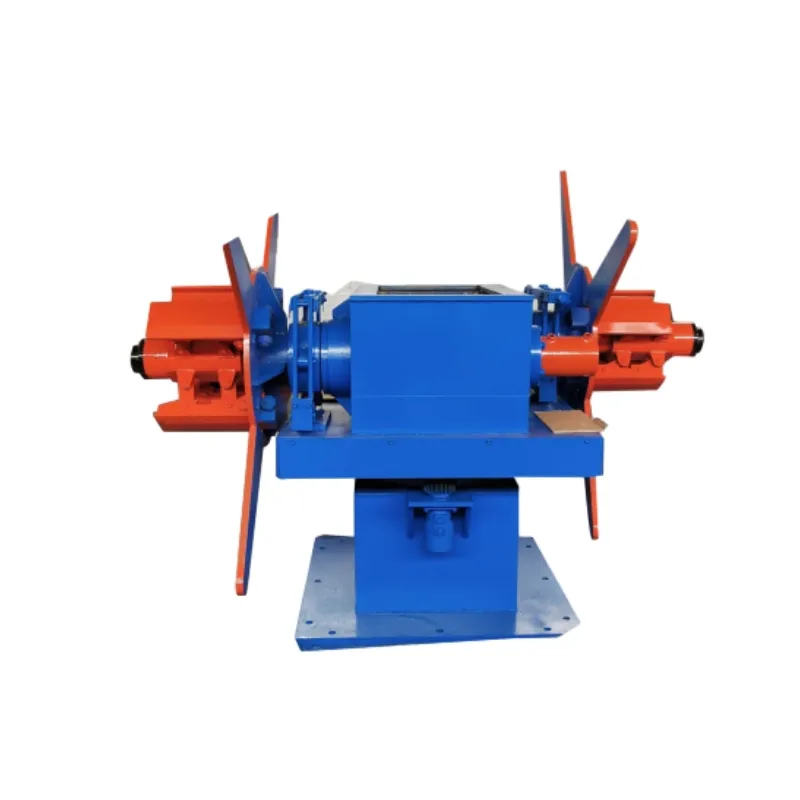
Industry specialists emphasize the importance of lubricants during the cold rolling process. They play a crucial role in reducing friction, preventing overheating, and ensuring the longevity of the rollers. This attention to detail in the process not only embodies an expert understanding but also fosters trust in the manufactured products.
Additionally, cold rolling improves the mechanical properties of aluminium, which includes its yield strength and tensile strength, making it more desirable for specific functionalities. For instance, the aerospace industry benefits from cold rolled aluminium’s enhanced fatigue resistance, which is vital for the safety and durability of aircraft components.
Moreover,
the surface finish obtained through cold rolling is of superior quality. This is essential for applications where aesthetic value is as important as functional performance, such as in the consumer electronics industry, where aluminium must retain an impeccable appearance coupled with robustness.
cold rolling aluminium
Manufacturers who have mastered the cold rolling technique often hold an authoritative position within the industry, partly because of their commitment to quality control throughout the fabrication process. They employ state-of-the-art machinery equipped with advanced sensors to monitor dimensions and surface quality constantly. This real-time data acquisition allows for immediate adjustments, minimizing waste and ensuring product consistency, thus earning the trust of discerning clients.
Environmental considerations have increasingly become paramount in manufacturing processes. Cold rolling is inherently a more sustainable method compared to its hot rolling counterpart due to its lower energy consumption. By leveraging this process, companies not only contribute to a reduction in their carbon footprint but also align themselves with global sustainability goals, reinforcing their reputation as responsible industry leaders.
From an industry-focused viewpoint, the expertise involved in cold rolling aluminium cannot be overstated. Skilled technicians and engineers are crucial to tailoring the process for specific applications, ensuring that every batch adheres to stringent specifications. Their extensive experience enables them to forecast potential challenges and implement preemptive measures, mitigating defects and ensuring the final product's integrity.
Trustworthiness in this domain is further enhanced by adhering to internationally recognized standards, such as ISO certifications. These standards provide clients with the assurance that the products have undergone rigorous quality assessments and comply with global benchmarks for performance and safety.
In conclusion, cold rolling of aluminium is not merely a technical process but a sophisticated blend of experience, expertise, authoritativeness, and trustworthiness. Mastery of this technique ensures the production of superior aluminium products that meet the exacting demands of modern industrial applications, solidifying a firm’s standing as a leader in the field. Integrating innovative practices alongside traditional expertise can propel a company towards achieving unparalleled product excellence and market leadership.