Cold rolling aluminum has become a pivotal process in the manufacturing industry, offering unparalleled advantages in strength, quality, and versatility. This technique involves passing aluminum stock through rollers at a temperature below its recrystallization temperature, leading to distinct mechanical properties and surface finish improvements. As the market for aluminum products continues to expand, understanding the intricacies of cold rolling becomes vital for businesses aiming to leverage this process for superior product quality.
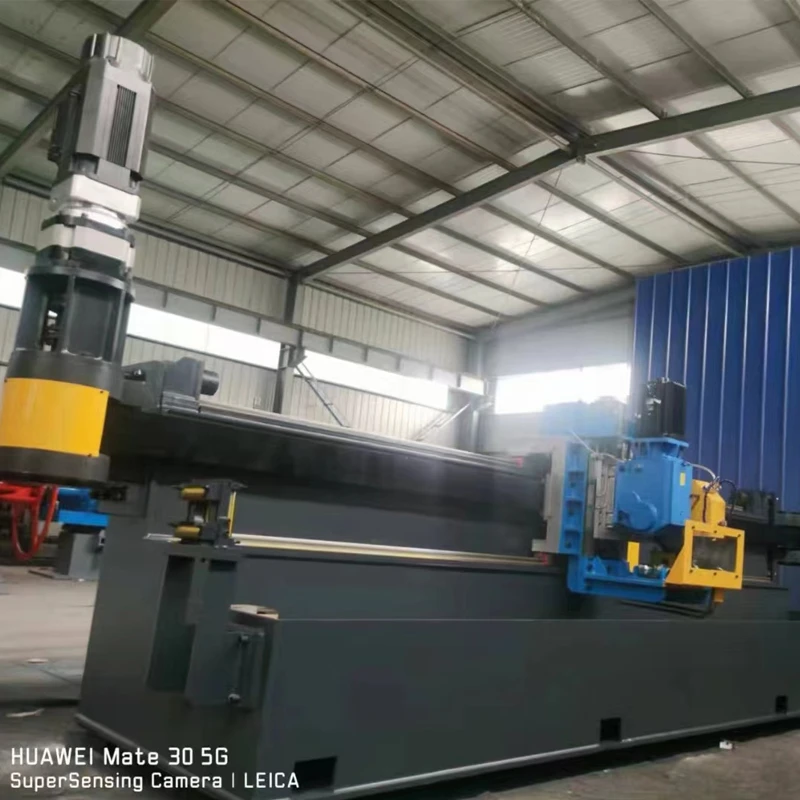
When we delve into the experience of manufacturers using cold rolling, we discover a method that significantly enhances aluminum's structural integrity. This process reduces thickness while increasing strength due to work hardening. The quality of the aluminum surface is also refined, achieving a smooth and polished finish that is highly sought after in the consumer goods market. Manufacturers report that products derived from cold-rolled aluminum exhibit superior resistance to stress and corrosion, making them ideal for high-performance applications in industries like automotive, aerospace, and construction.
From an expertise perspective, mastering the cold rolling process requires a deep understanding of material science and precise engineering. The control of temperature, speed, and pressure is crucial to achieving the desired results without compromising the aluminum's characteristics. Professionals in the field emphasize the importance of using advanced technology and precise calibration of the rolling mills to maintain consistency and quality throughout production. The adoption of computer-aided engineering and real-time monitoring systems has been instrumental in optimizing this process, ensuring minimal material waste and maximal output efficiency.
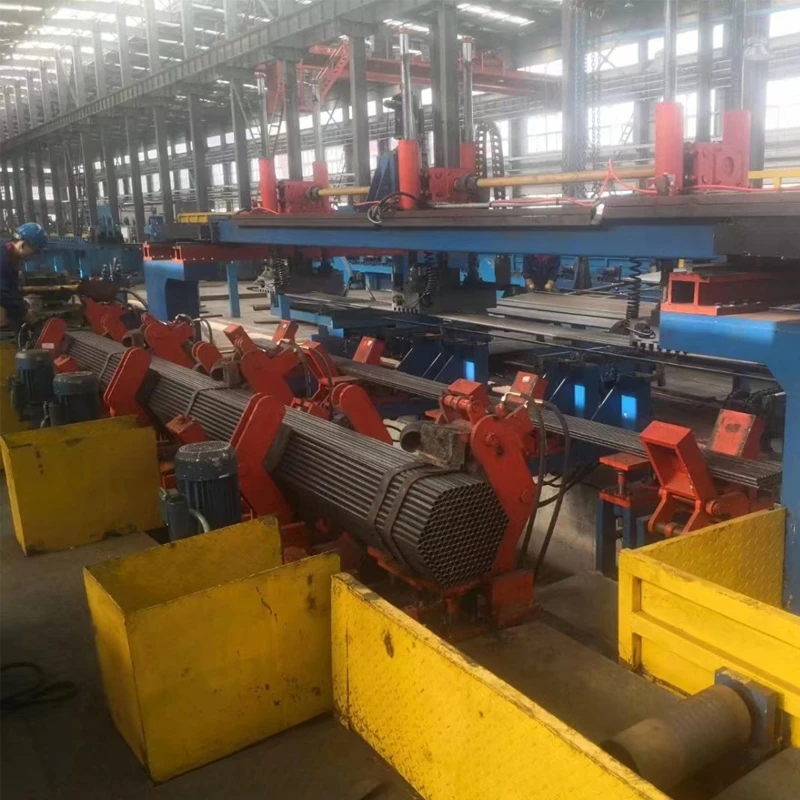
cold rolling aluminum
As for authoritativeness, numerous studies and industry reports confirm the advantages of cold rolling aluminum over traditional methods. Research articles in prominent material science journals highlight the microstructural modifications produced by cold rolling, resulting in enhanced durability and endurance. Leading organizations in the aluminum industry, such as the Aluminum Association, provide guidelines and standards that reinforce best practices, ensuring that manufacturers adhere to quality regulations and contribute to a sustainable production cycle. Expert panels and symposiums regularly address advancements in cold rolling technologies, underscoring its authoritative status in modern manufacturing ecosystems.
The trustworthiness of the cold rolling process is further validated through real-world applications and feedback. Many reputable companies across diverse sectors vouch for the performance of cold-rolled aluminum in their products. Whether it's in the construction of lightweight aircraft components or durable automotive parts, the process's reliability is attested by thousands of satisfied clients globally. Additionally, sustainability becomes an advantage with cold rolling, as it reduces energy consumption compared to hot rolling, thus aligning with global environmental standards and enhancing corporate responsibility.
For firms seeking to capitalize on cold rolling aluminum, the blend of experience, expertise, authoritativeness, and trustworthiness provides a comprehensive blueprint for success. Adopting this process can lead to the production of high-quality, durable, and versatile aluminum products, ensuring competitive advantage in a rapidly evolving market. By understanding and implementing the principles of cold rolling, companies not only enhance product offerings but also embrace a methodology that champions innovation, efficiency, and environmental preservation.