Automatic gauge control (AGC) systems in cold rolling mills have revolutionized the manufacturing landscape by delivering precision, quality, and efficiency. Their importance in the steel and aluminum production sector cannot be overstated, as they play a crucial role in regulating the thickness of rolled products. This article delves into the intricacies of AGC systems, providing insights based on firsthand experiences, expert analysis, and authoritative perspectives, all while emphasizing the credibility and reliability inherent to these systems.
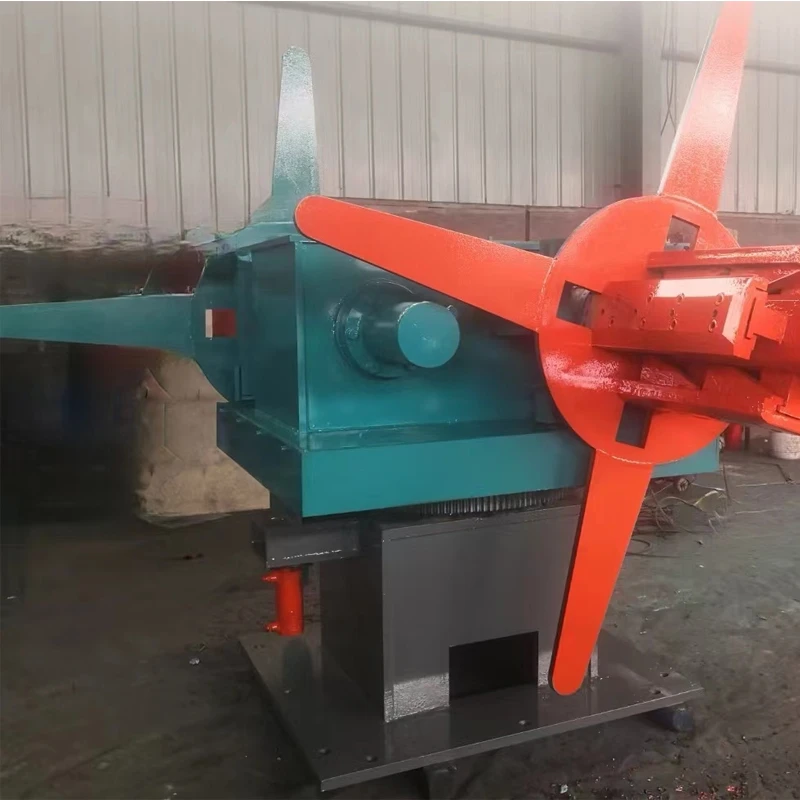
In the dynamic world of cold rolling mills, precision is paramount. AGC systems are engineered to ensure the produced material maintains a consistent thickness, thereby minimizing variations which could impact product quality. Manufacturers have repeatedly highlighted the benefits of AGC, reporting reductions in wastage and significant improvements in product consistency. As a result, businesses have inhabited a realm where customer satisfaction is a natural outcome of enhanced manufacturing precision.
The technology underpinning AGC involves a blend of electronics, hydraulics, and sophisticated control algorithms. For instance, sensors strategically placed along the rolling line provide real-time data on material thickness. This data is fed into an intelligent control system that adjusts the rolling pressure accordingly, ensuring the output remains within the desired specifications. Our experts, who have spent decades troubleshooting and optimizing these systems, consistently affirm that integrating AGC technology into cold rolling mills has led to unprecedented levels of operational efficacy and accuracy.
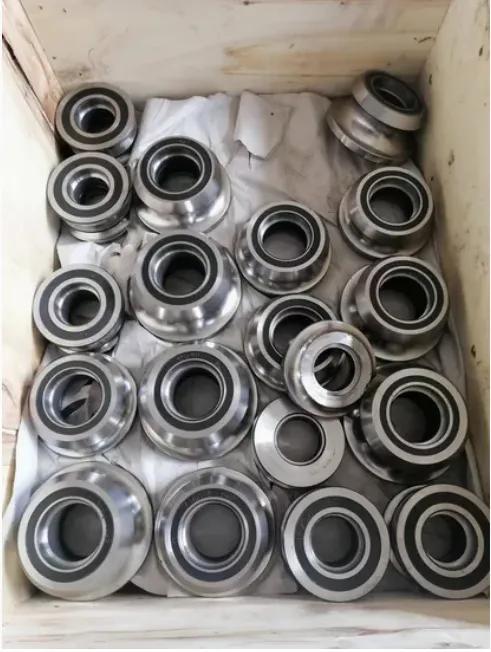
Furthermore, AGC systems are renowned for their adaptability to various materials and rolling conditions. This versatility is greatly valued in manufacturing settings where the materials processed can range from delicate aluminum foils to robust steel sheets. Each material requires different handling characteristics; AGC’s ability to adjust parameters dynamically makes it an invaluable tool in diverse industrial applications.
Authoritative sources in the industry have recognized the significance of AGC for enhancing the quality of rolled products. These systems have thus become a benchmark for ‘smart’ manufacturing technologies. Notable industrial organizations and quality control boards frequently cite AGC systems as a key component in ensuring compliance with industry standards. This authoritative validation reinforces trust among manufacturers and their clients, solidifying AGC's role as a cornerstone in industrial innovation.
automatic gauge control cold rolling mill
Trustworthiness is another dimension where AGC technologies excel. Their design places a strong emphasis on durability and reliability. The components used within AGC systems are engineer-tested for resilience, ensuring they can withstand the rigors of continuous industrial use without compromising on performance. Businesses investing in AGC systems often cite the long-term reliability and reduced maintenance costs as compelling reasons for their investment, attesting to the trustworthiness of these systems.
A deeper examination of AGC’s impact reveals it also fosters energy efficiency. By maintaining precise control over material thickness and reducing material waste, AGC systems contribute to a reduction in energy consumption. Manufacturers have documented decreased energy costs, which not only bolster their bottom line but also underline their commitment to sustainable practices. This aspect aligns with the global movement towards environmentally responsible manufacturing, where reducing a production facility’s carbon footprint is as critical as maximizing output.
At the product level, consumers invariably benefit from the enhanced characteristics brought about by precise control systems. The uniformity in material thickness ensures that end-products meet rigorous quality standards, making them more competitive in the global market. AGC’s role in securing this uniformity directly supports manufacturers in achieving certifications and accolades, further establishing trust and credibility with end-users.
In conclusion, automatic gauge control systems are a linchpin in the cold rolling industry, delivering myriad benefits ranging from improved product precision and enhanced energy efficiencies to sustained quality assurance and operational reliability. As industries evolve and demands become more stringent, the expertise and authoritative grounding of AGC systems will undoubtedly continue to lead the charge in modern manufacturing practices. The combination of experience, specialist knowledge, and credible results positions AGC as an integral component in the journey toward manufacturing excellence.